In the fields of transparent packaging, electronics, and consumer goods, PS (polystyrene) has become a mainstream choice for customized plastic parts due to its excellent light transmittance, easy processability, and cost advantages. This article systematically explores the technical logic of custom PS plastic parts, covering material characteristics, processing technologies, customization processes, and application scenarios, to provide efficient solutions for packaging, electronics, toys, and other industries.
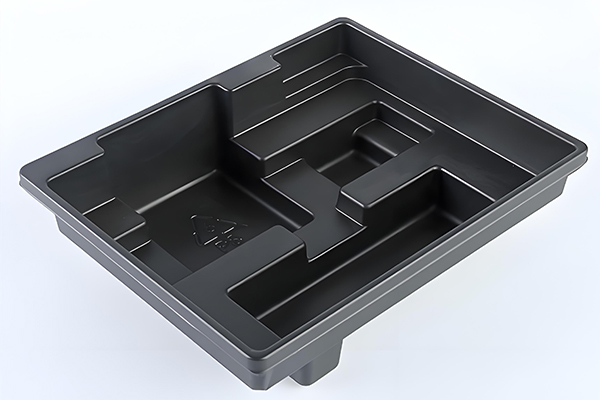
1. Material Characteristics: The Golden Combination of High Transparency and Low Cost
PS (polystyrene) forms two main systems—GPPS (General Purpose Polystyrene) and HIPS (High Impact Polystyrene)—through molecular structure optimization and modification technologies, with core properties and application advantages as follows:
1. Base Property Comparison and Modification Directions
Property | GPPS (General Purpose Polystyrene) | HIPS (High Impact Polystyrene) | Modified PS (Flame Retardant) | Core Advantages | Application Value |
---|---|---|---|---|---|
Light Transmittance | ≥88% | ≥85% | ≥80% | Exceptional clarity, comparable to glass | Transparent packaging, optical lenses |
Tensile Strength | 40-50 MPa | 25-35 MPa | 30-40 MPa | HIPS impact resistance 3x higher, reducing brittleness | Toy components, electronic housings |
Heat Deflection Temp. | 70-90℃ | 80-100℃ | 85-105℃ | Suitable for normal temperatures, short-term 120℃ resistance | Home appliance parts, food packaging |
Density | 1.04-1.06 g/cm³ | 1.05-1.07 g/cm³ | 1.06 g/cm³ | Moderate density balances lightness and cost | Weight-sensitive consumer goods, disposables |
Molding Shrinkage | 0.4%-0.7% | 0.5%-0.8% | 0.6% | Low shrinkage ensures dimensional stability | Precision gears, electronic connectors |
2. Modification Technologies for Expanded Applications
- Impact Resistance Modification (HIPS):
Incorporating butadiene rubber particles increases impact strength from 15 kJ/m² to 35 kJ/m², ideal for drop-resistant toy parts (e.g., building blocks, model accessories). - Flame Retardant Modification:
Adding brominated flame retardants (e.g., decabromodiphenyl ethane) achieves UL94 V-0 rating (1.6mm thickness), meeting fire safety requirements for electronic enclosures. - Antistatic Modification:
Conductive carbon powder composite reduces surface resistance to 10⁶-10⁹Ω, preventing dust adsorption for precision electronic component trays.
2. Processing Technology: Diverse Molding and Surface Treatment Solutions
1. Core Molding Process Comparison
Process | Precision (mm) | Daily Capacity (pcs) | Suitable Scenarios | Typical Parts | Key Parameter Control |
---|---|---|---|---|---|
Injection Molding | ±0.05 | 8,000-30,000 | Complex and precision parts | Electronic housings, gears, optical lenses | Material temp 200-240℃, mold temp 40-60℃, holding time 10-15s |
Extrusion | ±0.1 | 15,000+ | Sheets, pipes, profiles | Transparent sheets, CD cases, packaging tubes | Screw speed 20-50rpm, traction speed 8-15m/min |
Thermoforming | ±0.3 | 10,000-25,000 | Thin-walled transparent packaging | Food trays, electronic screen protectors | Heating temp 150-180℃, forming pressure 0.5-1.0MPa |
Blow Molding | ±0.2 | 5,000-20,000 | Hollow containers, thin-walled products | Disposable cups, cosmetic bottles | Blowing pressure 0.6-1.2MPa, cooling time 8-12s |
2. Surface Treatment and Functional Enhancement
- Printing Processes:
- Silk/Pad Printing: Good adhesion without pretreatment (3M tape test peeling ≤5%), supports CMYK full-color for logo customization and graphics.
- Electroplating:
- Electroless nickel/chrome plating (10-15μm thickness), 48-hour salt spray resistance, endow PS parts metallic finishes (e.g., toy car shells, decorative items).
- Coating Modification:
- Scratch-resistant coating (3H hardness), 500-cycle friction test with no wear, used for phone cases and optical lens reinforcement.
3. Customization Process: End-to-End Control for Precise Delivery
1. Requirement Diagnosis (1-2 Business Days)
- Application Definition: Clarify part use (transparent packaging/structural/aesthetic), environmental conditions (humidity/light/mechanical load), and precision level (general tolerance ±0.1mm or precision ±0.03mm).
- Material Selection: Provide material proposals within 1 business day, e.g., high-transparency GPPS (≥88% transmittance) or impact-resistant HIPS (35 kJ/m² impact strength), with cost comparison (GPPS $0.07-$0.14/piece, HIPS $0.11-$0.21/piece).
2. Design and Validation (5-7 Business Days)
- Structural Optimization:
Moldflow simulation optimizes filling for PS fluidity, designing thin walls (1-2mm thickness) and ribs (spacing ≤12mm) to enhance rigidity and avoid stress cracking. - Rapid Prototyping:
- 3D Printing (SLA): 24-hour transparent PS prototype delivery with ±0.15mm precision for optical performance verification.
- Silicone Mold Small Batch (100-piece minimum): Replicates HIPS drop resistance for 1.5m fall test (breakage rate ≤5%).
3. Mass Production and Quality Inspection
- Process Control:
- Injection Molding Smart Monitoring: Temperature fluctuation ≤2℃, pressure fluctuation ≤5%, mold temperature controlled via chiller (error ±1℃) to reduce sink marks (depth ≤0.1mm).
- Extrusion Line: Online thickness gauge maintains uniformity error ≤3%, ensuring consistent transparency for packaging.
- Inspection System:
Inspection Item Standard Requirements Equipment/Method Pass Criteria Light Transmittance GPPS≥88%, HIPS≥85% Haze meter 100% compliance Impact Strength HIPS≥30 kJ/m² Izod impact tester 100% compliance Dimensional Accuracy Critical dimensions ±0.05mm Coordinate Measuring Machine CPK≥1.33
4. Application Scenarios: Custom Solutions for All Industries
1. Packaging & Display
- Transparent Packaging:
- GPPS blister packs: ≥88% transmittance, haze ≤5%, UV blocking rate 90% (with UV absorber), ideal for jewelry and cosmetic display to prevent aging.
- HIPS folding boxes: 35 kJ/m² impact strength, 50kg compression resistance, suitable for transporting home appliance parts and industrial components.
- Food-Contact Packaging:
Food-grade PS (FDA 21 CFR 177.1640 compliant) disposable containers, heavy metal migration ≤0.1ppm, 80℃ heat resistance for cold food and salad packaging.
2. Electronics & Electricals
- Electronic Housings:
Flame-retardant HIPS (UL94 V-0) router enclosures, 10⁹Ω surface resistance, no deformation at 70℃ for 24 hours, meeting 3C safety certifications (CCC, CE). - Optical Components:
GPPS optical lenses with surface accuracy PV≤λ/4 (λ=632.8nm), 90% light diffusion rate for LED diffusers, uniformity error ≤5%.
3. Toys & Consumer Goods
- Toy Parts:
HIPS building blocks with 35 kJ/m² impact strength, rounded edges ≥2mm, compliant with GB 6675 toy safety standards, colorfast for 5+ years (with light stabilizer). - Daily Products:
PS makeup mirror housings with electroplated gloss ≥90GU, 48-hour salt spray resistance, and IMD in-mold decoration for one-step personalized patterns.
4. Industrial & Agricultural
- Industrial Components:
Antistatic PS electronic trays with 10⁸Ω surface resistance, passing ESD ±8kV contact discharge testing to protect precision chips in the semiconductor industry. - Agriculture:
PS seedling labels with 500-hour QUV weather resistance (ΔE≤3), 4B ink adhesion, and 2-year outdoor legibility without fading.
5. Industry Trends & Technological Innovations
1. Sustainability and Green Development
- Bio-Based PS:
Pine fiber-derived bio-based PS with 40% bio-content, ≥60% degradability, suitable for recyclable packaging and eco-friendly consumer designs. - Recycling Technology:
Post-consumer recycled PS (PCR-PS) retains ≥85% performance for non-food contact parts (e.g., industrial packaging), compliant with EU Packaging Law (PPW).
2. High-Performance Modification Breakthroughs
- High-Temperature PS:
SAN (Styrene-Acrylonitrile) modified PS, heat deflection temperature increased to 110℃, ideal for coffee machines and microwave accessories. - Conductive PS:
Carbon nanotube-modified PS with surface resistance ≤10⁶Ω, shielding effectiveness ≥30dB (1GHz), 60% weight reduction vs. metal for EMI shields.
3. Intelligent Manufacturing Upgrades
- Digital Twin Molds:
AI-optimized gate location reduces trial molds by 40%, shortens mold development to 15 days, and improves transparent part transmittance consistency to 98%. - Green Production:
Waterless cooling saves 70% water, 95% scrap recycling rate, compliant with ISO 14001 environmental management.
6. Frequently Asked Questions (FAQ)
Q1: What is the temperature resistance range for PS parts?
A: General PS withstands ≤70℃ long-term, HIPS ≤80℃, modified SAN-PS up to 110℃, with short-term resistance up to 120℃—suitable for normal to moderate temperature applications.
A: General PS withstands ≤70℃ long-term, HIPS ≤80℃, modified SAN-PS up to 110℃, with short-term resistance up to 120℃—suitable for normal to moderate temperature applications.
Q2: How to address PS brittleness?
A: Choose HIPS for higher impact resistance (35 kJ/m²) or improve structural design with rounded corners (R≥2mm) and ribs to reduce stress concentration.
A: Choose HIPS for higher impact resistance (35 kJ/m²) or improve structural design with rounded corners (R≥2mm) and ribs to reduce stress concentration.
Q3: What certifications are needed for food-grade PS?
A: Requires FDA 21 CFR 177.1640, EU EU 10/2011, and China GB 4806.7, ensuring total migration ≤10mg/dm² for direct food contact.
A: Requires FDA 21 CFR 177.1640, EU EU 10/2011, and China GB 4806.7, ensuring total migration ≤10mg/dm² for direct food contact.
Q4: What’s the minimum order quantity for small batches?
A: 500 pieces minimum, using quick aluminum molds (7-day lead time), 15% higher cost than steel molds—ideal for samples (e.g., 1,000 GPPS parts at ~$0.11/piece).
A: 500 pieces minimum, using quick aluminum molds (7-day lead time), 15% higher cost than steel molds—ideal for samples (e.g., 1,000 GPPS parts at ~$0.11/piece).
7. Customer Testimonial
“Partnering with the team for 20,000 HIPS toy housings, we achieved delivery in just 30 days. Parts had 35 kJ/m² impact strength, only 3% breakage in 1.5m drops, and 85% transmittance for visual appeal. Mold runner optimization shortened cycle time by 15%, yielding 97% good parts. The cost-effective HIPS material and fast delivery gave us a competitive edge in children’s toy projects!” ——Purchasing Manager of a Toy Manufacturer
Start Your Customization Journey Today
Whether for high-transparency packaging, drop-resistant toys, or flame-retardant electronics, we leverage PS material expertise and intelligent processes to deliver end-to-end solutions. Contact us for a tailored proposal and unlock the versatile potential of PS parts—where clarity meets cost-effectiveness.