In industrial manufacturing and consumer sectors, PVC (polyvinyl chloride) stands out as a mainstream material for customized plastic parts due to its excellent cost-effectiveness, chemical resistance, and processing flexibility. This article systematically explores the core advantages of custom PVC plastic parts, covering material characteristics, processing technologies, application scenarios, and quality control, to provide efficient and economical solutions for diverse industries.
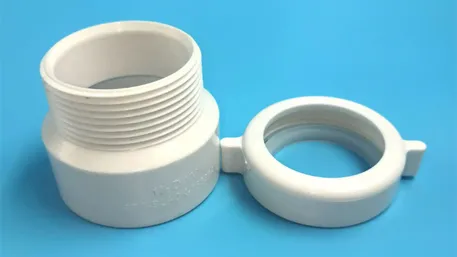
Property |
Typical Parameters (Rigid PVC) |
Flexible PVC (30% Plasticizer) |
Core Advantages |
Application Value |
Tensile Strength |
45-55 MPa |
15-25 MPa |
Wide strength range for different loads |
Structural parts (rigid), flexible components (flexible) |
Heat Deflection Temp. |
75-85℃ |
50-60℃ |
Flexible PVC resists low temps (-10℃); rigid PVC suits normal heat |
Outdoor equipment (flexible), general industrial parts (rigid) |
Density |
1.3-1.4 g/cm³ |
1.1-1.3 g/cm³ |
Moderate density balances cost and lightness |
Weight-sensitive consumer goods, construction fittings |
Chemical Resistance |
Excellent to acids/bases/salts |
Improved oil resistance |
Corrosion resistance for harsh environments |
Chemical pipelines, bathroom fixtures, anti-corrosion equipment |
Melt Flow Rate |
Moderate (MFR 2-5 g/10min) |
Excellent (MFR 8-12 g/10min) |
Easy processing for complex structures |
Precision injection parts, extruded profiles |
- Plasticizer Modification:
Adding phthalates (e.g., DOP) creates flexible PVC with 300% elongation at break, ideal for seals, wire sheaths, and other flexible parts.
- Flame Retardant Modification:
Antimony trioxide compound systems achieve UL94 V-0 rating (1.6mm thickness), meeting fire safety standards for electronics.
- Weather Resistance Modification:
UV absorbers (e.g., UV-531) enhance weather resistance by 50%, extending outdoor service life to 5+ years.
- Lead-Free Trend:
RoHS/REACH-compliant lead-free PVC (lead content <100ppm) eliminates heavy metal risks, suitable for food contact and medical applications.
- Cost Efficiency:
Material cost is 70% of ABS and 50% of PA, making it ideal for mass production and cost-sensitive projects.
- Injection Molding:
- Parameters: Barrel temperature 180-200℃, injection pressure 60-80MPa, suitable for precision parts (e.g., electronic connectors, gears) with dimensional tolerance ±0.05mm.
- Mold Design: Beryllium copper cooling inserts shorten cycle time by 20% and reduce sink marks (depth ≤0.1mm).
- Extrusion Molding:
- Applications: Pipes, profiles (e.g., PVC-U drain pipes, custom extrusions), line speed 5-10m/min, wall thickness tolerance ±0.1mm.
- Energy-Saving: Electromagnetic heating saves 30% energy vs. traditional resistance heating, with temperature control ±1℃.
- Calendering:
- Film/Sheet Production: Thickness 0.1-2mm, surface roughness Ra≤0.4μm, used for packaging sheets and transparent window components.
- Printing Processes:
- Silk/Pad Printing: Precision ±0.1mm, supports CMYK full-color, passes 3M tape test (peeling ≤5%) for logo and pattern customization.
- Coating Technologies:
- Antibacterial Coating: Silver ion additives achieve ≥99% bacteriostasis, used for medical trays and food packaging.
- Wear-Resistant Coating: PTFE coating reduces friction to 0.2, extending moving part life by 15%.
- Electroplating/Coating:
- Electroplatable PVC: Surface roughening enables nickel plating with 5N/cm² adhesion, achieving metallic finishes for bathroom hardware.
- Application Definition: Clarify part use (structural/aesthetic/functional), environmental conditions (moisture/corrosion/outdoor), and precision level (general tolerance ±0.1mm or precision ±0.03mm).
- Solution Design: Provide material type (rigid/flexible/modified PVC), process route (injection/extrusion/calendering), and cost estimates (e.g., rigid PVC parts $0.07-$0.70/piece) within 1 business day.
- 3D Modeling: Use SolidWorks for structural optimization, e.g., thin-wall thickness 1-3mm, rib spacing ≤10mm to enhance rigidity and avoid stress concentration.
- Rapid Prototyping:
- 3D Printing (FDM): 24-hour prototype delivery for structural verification, precision ±0.2mm.
- Silicone Mold Small Batch (100-piece minimum): Replicates final material properties for functional testing (e.g., sealing, temperature resistance).
- Process Control:
- Injection Molding: Real-time monitoring of pressure (fluctuation ≤5%) and temperature (fluctuation ≤2℃), ensuring uniform filling with defect rate ≤0.3%.
- Extrusion Line: Online thickness gauge maintains wall uniformity error ≤3%, ensuring pipe pressure resistance (e.g., PN10 rating).
- Inspection System:
Inspection Item |
Standard Requirements |
Equipment/Method |
Pass Criteria |
Dimensional Accuracy |
Critical dimensions ±0.05mm |
Coordinate Measuring Machine |
CPK≥1.33 |
Weather Resistance |
QUV aging 1000 hours ΔE≤3 |
UV weathering chamber |
Color change compliant |
Sealing Performance |
No leakage at 10kPa pressure |
Air tightness tester |
Leakage rate = 0 |
- Pipeline Systems:
- UPVC Drain Pipes: Smooth inner surface (Ra≤0.2μm), low flow resistance, acid/alkali resistance, 50+ year lifespan, 40% cheaper than cast iron.
- Window/Door Profiles: Weather-resistant PVC with titanium dioxide, UV resistance grade 8, no cracking after 50 thermal cycles (-30℃~70℃), compliant with GB/T 8814.
- Decorative Fittings:
Flexible PVC baseboards, easy to install, 5000-cycle wear test with no surface damage, customizable wood/stone textures.
- Equipment Housings:
Flame-retardant PVC (UL94 V-0) distribution box enclosures, arc resistance ≥120 seconds, IP54 protection, suitable for humid environments.
- Wiring Components:
Flexible PVC insulation sleeves, breakdown voltage ≥20kV, temperature resistance -40℃~105℃, VDE 0282 certified for automotive wiring.
- Medical Consumables:
Phthalate-free PVC infusion bags, ISO 10993 biocompatible, extractable residue ≤0.1μg/mL for safe drug delivery.
- Toys & Daily Products:
Eco-friendly PVC children’s toys, compliant with GB 6675, rounded edges ≥2mm, plasticizer migration ≤0.05mg/kg for child safety.
- Mechanical Parts:
Rigid PVC gears, noise ≤70dB, resistant to lubricating oil, 70% cheaper than metal gears for low-speed transmission.
- Agricultural Irrigation:
PVC irrigation pipes, smooth inner wall for high flow, 1.6MPa water pressure resistance, soil corrosion resistance, 15+ year lifespan, low maintenance cost.
- Bio-Based PVC:
Corn starch-derived plasticizers with 30% bio-content reduce carbon emissions by 25%, suitable for green packaging and degradable products.
- Circular Economy:
Mature recycled PVC technology retains ≥80% performance for non-food contact parts like construction pipes and industrial pallets.
- Micro-Injection Molding:
Forms parts <0.5g with ±0.03mm tolerance, meeting precision needs for MEMS sensor housings.
- Smart Factory Solutions:
MES systems track production data in real time, 90% accurate mold life prediction, 20% higher overall equipment effectiveness (OEE).
- Conductive PVC:
Carbon black-filled antistatic PVC, surface resistance ≤10⁹Ω, used for electronic component turnover box to prevent ESD damage.
- Thermo-Sensitive PVC:
Shape-memory additives restore preset shape at 60℃, applied in intelligent pipeline valve control.
Q1: What is the temperature range for PVC parts?
A: Rigid PVC operates ≤60℃ long-term; flexible PVC ≤50℃; modified CPVC resists 100℃, ideal for hot water pipes.
Q2: How to minimize plasticizer migration in PVC?
A: Use eco-friendly plasticizers (e.g., citrate esters) with migration ≤0.1mg/kg, compliant with food contact standards (e.g., FDA 21 CFR 175.300).
Q3: What’s the minimum order quantity for small batches?
A: 500 pieces minimum, using quick aluminum molds (7-day lead time), 15% higher cost than steel molds—perfect for samples and small-scale trials.
Q4: What certifications are needed for food-grade PVC?
A: Require FDA, EU 10/2011, and China GB 4806.7 certifications, ensuring vinyl monomer residue ≤1ppm for food packaging and drinking water systems.
“Partnering with the team for 100,000 PVC electronic enclosures, we achieved delivery in just 30 days. Parts met UL94 V-0 flame rating, ±0.05mm precision, and 48-hour salt spray resistance. Mold runner optimization improved yield from 90% to 96%, cutting costs by 12% below expectations. Their professional eco-material solutions and fast delivery provided a reliable, low-cost answer for our security equipment project!” ——A Security Equipment Manufacturer
Whether for corrosion-resistant pipe fittings in construction or flame-retardant enclosures in electronics, we leverage formulation design and intelligent processes to deliver end-to-end solutions. Contact us for a tailored proposal and unlock the versatile potential of PVC parts—where cost-effectiveness meets reliability.