In high-end manufacturing and precision engineering, resin-based plastics have become core materials for customized parts due to their exceptional comprehensive properties, diverse material systems, and flexible forming processes. This article systematically explores the technical logic of custom resin plastic parts, covering material characteristics, processing technologies, customization processes, and application scenarios, to provide professional solutions for industries such as aerospace, electronics, and medical devices.
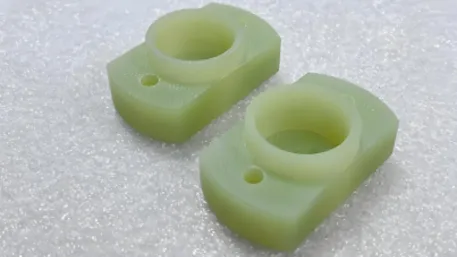
Resin materials form a complete system including thermosets, thermoplastics, and composite resins through molecular design and modification, with core properties and application advantages as follows:
Resin Type |
Representative Material |
Tensile Strength (MPa) |
Temperature Resistance (℃) |
Core Advantages |
Typical Applications |
Thermoset Resins |
Epoxy Resin (EP) |
80-150 |
-50~180 |
High strength, chemical resistance, excellent electrical insulation |
Electronic packaging, structural adhesives |
Unsaturated Polyester |
Polyester Resin (UP) |
60-100 |
-40~120 |
Strong weather resistance, low cost, easy molding |
Automotive exteriors, fiberglass products |
Thermoplastic Resins |
Polymethyl Methacrylate (PMMA) |
70-90 |
-30~90 |
High light transmittance (≥92%), easy to color |
Optical lenses, advertising light boxes |
Composite Resins |
Carbon Fiber Reinforced Polymer (CFRP) |
200-400 |
-60~200 |
High strength, low density (1.5g/cm³) |
Aerospace structures, high-end sports equipment |
- Reinforcement Modification:
Carbon/glass fiber reinforcement increases tensile strength by 100%-300%, e.g., CFRP reaches 350MPa, suitable for aerospace load-bearing components.
- Functional Modification:
Carbon nanotube-filled conductive resins achieve surface resistance ≤10⁶Ω for ESD protection in electronic components; flame-retardant resins meet UL94 V-0 (0.8mm thickness) for lithium battery cases.
- Weather Resistance Modification:
UV absorber-modified PMMA enhances weather resistance by 50%, with transmittance loss ≤10% after 10 years of outdoor use, ideal for optical instrument housings.
- Injection Molding (Thermoplastics):
- Precision injection: Mold accuracy ±0.01mm, forming 0.3mm thin-wall parts with dimensional tolerance ±0.03mm, suitable for PMMA optical lenses.
- Reaction injection (Thermosets): Two-component mixing injection reduces curing time to 5 minutes, used for epoxy electronic encapsulation.
- Compression Molding:
- Hot pressing: 10-30MPa pressure, 120-180℃ temperature, forming CFRP composite parts with 60% fiber volume fraction and flexural strength ≥400MPa.
- Low-pressure RTM: Mold pressure ≤0.5MPa, suitable for large composite components (e.g., wind turbine blades) with dimensional accuracy ±0.5mm.
- 3D Printing:
- SLA Stereolithography: Layer thickness 50-100μm, surface roughness Ra≤1.6μm, rapidly prototyping complex structures (e.g., medical implant models).
- FDM Fused Deposition: Compatible with ABS/nylon resins, supports multi-material printing for functional prototype verification.
- Optical Treatment:
Nano-coating on PMMA parts increases transmittance to 95% and haze ≤1%, meeting AF (anti-fingerprint)/AR (anti-reflective) requirements for optical lenses.
- Wear Resistance Treatment:
PTFE coating on epoxy parts reduces friction to 0.15 and wear by 40%, suitable for precision gears.
- Conductive Treatment:
Electroless nickel plating achieves surface resistivity ≤10Ω·cm for EMI shielding cases, with shielding effectiveness ≥60dB (1GHz band).
- Application Analysis: Clarify load type (static/dynamic), environmental conditions (temperature/humidity/corrosion), and precision level (IT5 tolerance or functional tolerance).
- Material Selection: Provide resin recommendations within 2 business days, e.g., epoxy for high-temperature scenes (resists 180℃) and PMMA for optical applications (transmittance ≥92%).
- Structural Optimization:
ANSYS finite element analysis optimizes CFRP fiber layup angles (0°/45°/90° mix), increasing flexural strength by 25% and reducing weight by 15%.
- Rapid Prototyping:
- SLA Prototypes: 3-day delivery of optical resin parts with ±0.1mm precision for LiDAR lens verification.
- Silicone Mold Small Batch (50-piece minimum): Replicates thermoset mechanical properties for high-temperature aging tests (150℃, 1000 hours).
- Process Control:
- Injection Molding Smart Temperature Control: Temperature fluctuation ≤1℃, pressure fluctuation ≤3%, ensuring PMMA transmittance consistency (deviation ≤2%).
- Compression Molding Pressure Monitoring: Real-time pressure sensor feedback ensures CPK≥1.67 for uniform fiber distribution in CFRP parts.
- Inspection System:
Inspection Item |
Standard Requirements |
Equipment/Method |
Pass Criteria |
Dimensional Accuracy |
Critical dimensions ±0.02mm |
Coordinate Measuring Machine (CMM) |
100% full-size pass rate |
Light Transmittance |
PMMA parts ≥90% |
Haze meter |
100% compliance |
Flame Retardancy |
UL94 V-0 (0.8mm) |
Vertical burn tester |
Self-extinguishing time ≤10s |
- Structural Components:
CFRP resin-based composite wing ribs with 300MPa tensile strength and 1.6g/cm³ density, 40% lighter than aluminum, meeting aerospace lightweight requirements.
- Interior Parts:
Flame-retardant epoxy panels with smoke density ≤50 (ASTM E662), suitable for aircraft cabin interiors, compliant with FAA FAR 25.853 fire standards.
- Optical Parts:
PMMA precision lenses with surface accuracy PV≤λ/4 (λ=632.8nm), used in LiDAR systems with ranging error ≤0.5%.
- Electronic Packaging:
Epoxy encapsulants with volume resistivity ≥10¹⁴Ω·cm and water absorption ≤0.1%, protecting 5G power amplifier chips from moisture.
- Implants:
Biocompatible polyurethane resin artificial joints with wear rate ≤0.05mm³/million cycles, compliant with ISO 10993 biological safety standards.
- Diagnostic Equipment:
Transparent resin microfluidic chips with channel dimension accuracy ±5μm, used in IVD devices with liquid flow control error ≤2%.
- High-End Watches:
Ceramic resin watch cases with hardness HV≥1200 and 9H scratch resistance, 60% lighter than stainless steel for improved wear comfort.
- Industrial Sensors:
Low-temperature-resistant resin housings (-60℃), IP68 protection, used for pipeline monitoring sensors in permafrost areas with 10+ year lifespan.
- Bio-Based Resins:
Castor oil-derived polyurethane with 40% bio-content reduces carbon emissions by 30%, suitable for eco-friendly consumer designs.
- Nanocomposite Resins:
Graphene-reinforced epoxy increases thermal conductivity 3x (1.2W/m·K), solving heat dissipation for high-density ICs.
- Digital Twin Molds:
AI-optimized mold flow analysis reduces trial molds by 70%, shortening mold development to 15 days and R&D costs by 40%.
- Closed-Loop Quality Control:
Machine vision real-time inspection (500 pieces/minute) with 0.05mm defect recognition precision, miss rate <0.01% for zero-defect production.
- Smart Response Resins:
Shape-memory resins restore preset shapes at 60℃, used for satellite deployment structures to enable self-assembly in space.
- Energy-Harvesting Resins:
Piezoelectric resin films convert vibration to electricity (5μW/cm² output), providing self-power solutions for IoT sensors.
Q1: What is the maximum temperature resistance of resin parts?
A: Thermosets (e.g., epoxy) withstand ≤180℃ long-term; thermoplastics (e.g., modified PPS) reach 260℃; specialty resins (e.g., polyimide) exceed 300℃—choose based on application conditions.
Q2: How to minimize dimensional shrinkage in resin parts?
A: Mold flow analysis optimizes gate design to control shrinkage: thermosets ≤0.3%, thermoplastics ≤0.5%. Precision parts use secondary CNC machining for final accuracy.
Q3: What’s the minimum order quantity for small batches?
A: 100 pieces minimum, using quick molds (aluminum/silicone), 20% higher cost than steel molds—ideal for R&D prototyping and small-scale trials.
Q4: What certifications are required for medical-grade resins?
A: Require ISO 10993 biocompatibility, FDA 510 (k) (US), or CE MDR (EU), ensuring cytotoxicity ≤Grade 1 and sensitization rate <0.1%.
“Collaborating with the team for 5,000 aerospace-grade CFRP parts, we achieved delivery in just 45 days. Parts retained 95% strength after 1,000 hours of high-temperature aging (180℃), with dimensional accuracy ±0.03mm and 35% weight reduction vs. aluminum. Fiber layup optimization increased fatigue life by 20%, fully meeting the strict requirements for aerospace structures. Their professional material selection and process control delivered a transformative solution for our UAV project!” ——R&D Director of an Aerospace Technology Company
Whether for lightweight aerospace structures or high-transmittance optical components, we leverage resin material expertise and intelligent processes to deliver end-to-end solutions. Contact us for a tailored proposal and unlock the full potential of resin parts—where high performance meets precision engineering.