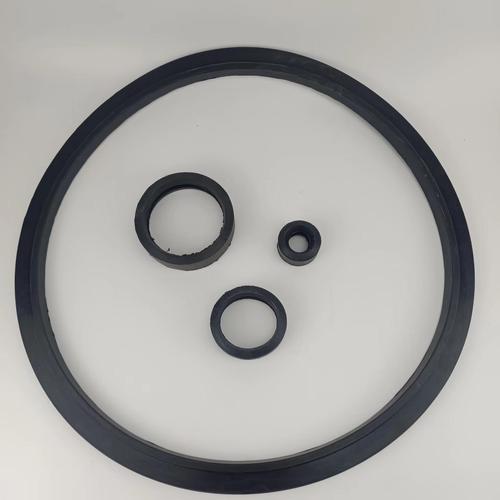
I. Core Material Properties and Application Advantages
(A) Comparison of Mainstream Material Properties
Material Type
|
Density (g/cm³)
|
Temperature Range (℃)
|
Shore A Hardness
|
Chemical Resistance (Typical Media)
|
Core Advantages
|
Typical Certifications
|
Nitrile Butadiene Rubber (NBR)
|
1.2–1.4
|
-40~120
|
40–90
|
Mineral oil, hydraulic oil
|
Excellent oil resistance, high elasticity
|
ISO 16232 Automotive Certification
|
Silicone Rubber (SIL)
|
1.1–1.3
|
-60~200
|
20–80
|
Extreme temperature, weathering
|
Non-toxic, electrical insulation, environmental friendly
|
FDA Food Contact Certification
|
Fluorine Rubber (FKM)
|
1.8–2.0
|
-20~250
|
60–90
|
Strong acid, alkali, fuel oil
|
Excellent high-temperature and chemical resistance
|
ASTM D2000 Performance Certification
|
Ethylene Propylene Diene Monomer (EPDM)
|
0.9–1.1
|
-50~150
|
40–80
|
Water vapor, UV radiation
|
Outstanding weather and aging resistance
|
EN 681-1 Sealing Standard Certification
|
Hydrogenated Nitrile Butadiene Rubber (HNBR)
|
1.2–1.3
|
-30~150
|
50–90
|
Ozone, high-pressure oil
|
High strength, low-temperature impact resistance
|
IATF 16949 System Certification
|
(B) Driving Forces of Customization Requirements
1. Sealing Performance Requirements
- Pressure Resistance: Static sealing pressure ≥10MPa (hydraulic systems), dynamic sealing pressure ≥5MPa (rotating shaft seals).
- Leakage Rate: Helium mass spectrometer detection, leakage ≤1×10⁻⁹ mbar·L/s (high-vacuum environments).
- Compression Set: 150℃×22h test, deformation rate ≤20% (GB/T 7759.1 standard).
2. Environmental Adaptability
- Thermal Shock Resistance: -40℃~120℃ cycling 50 times, hardness change ≤±5 Shore A.
- Weather Resistance: QUV-A aging test for 1000 hours, cracking grade ≤1 (GB/T 16422.3).
- Chemical Resistance: Immersion in 10% sulfuric acid/sodium hydroxide for 72 hours, volume change rate ≤5%.
3. Structural Adaptability
- Dimensional Accuracy: Inner/outer diameter tolerance ±0.1mm, thickness tolerance ±0.05mm (GB/T 3452.1 standard).
- Surface Roughness: Sealing surface Ra≤1.6μm to reduce micro-leakage paths.
II. Analysis of Four Core Processing Technologies
(A) Compression Molding: High-Precision Seal Processing
- Technical Advantages
-
- Enables one-step molding of complex sections such as O-rings and flange gaskets, dimensional accuracy ±0.05mm.
-
- Multi-cavity design (8–32 cavities per mold), production efficiency 500–2000 pieces/hour, compatible with GB, ASME, JIS standards.
- Process Parameters
-
- Vulcanization temperature 150–200℃, pressure 10–30MPa, vulcanization time 3–10 minutes (adjusted by thickness).
-
- Mold surface roughness Ra≤0.8μm to ensure sealing surface smoothness.
(B) Injection Molding: Automated Mass Production
Process Type
|
Typical Application Scenarios
|
Technical Highlights
|
Cold Runner Injection
|
High-precision O-rings
|
Material utilization ≥95%, flash thickness ≤0.05mm
|
Liquid Silicone Rubber (LSR) Injection
|
Medical-grade seals
|
Cleanroom production (Class 100,000), compliant with ISO 13485 standard
|
- Technical Advantages
-
- Fully automated production line integrates material to finished product, defect rate ≤0.3%.
-
- Supports thin-wall design (thickness ≥0.5mm) for micro-seal precision requirements.
(C) Extrusion Molding: Custom Long Sealing Parts
- Process Advantages
-
- Suitable for continuous seals like weather strips and rubber hoses, length error ≤0.1%.
-
- Multi-layer co-extrusion technology combines wear-resistant/oil-resistant layers, extending life by 30%.
- Key Parameters
-
- Extrusion speed 5–15m/min, temperature control accuracy ±2℃.
-
- Cross-sectional dimension tolerance ±0.2mm, adaptable to complex sealing structures.
(D) Secondary Processing: Functional Enhancement
- Surface Modification
-
- PTFE coating: Friction coefficient reduced by 40% (to <0.15), suitable for high-speed rotating seals.
-
- Conductive coating: Surface resistance ≤10⁶Ω to prevent static accumulation (electronic device sealing).
- Structural Optimization
-
- Metal skeleton embedding: Tensile strength increased by 50%, suitable for high-pressure applications (e.g., hydraulic cylinder seals).
-
- Lip chamfer design: Sealing lip angle 30°±5°, contact pressure uniformity improved by 20%.
III. Full-Process Customization Solutions
(A) Design and Material Engineering
1. Multi-Dimensional Design Support
- Structural Optimization
-
- FEA simulation of sealing surface pressure distribution ensures contact stress ≥3MPa (leakage critical value).
-
- Lip seal lip thickness designed at 1.5–2.5mm, dynamic sealing life ≥1000 hours (GB/T 13871.4 standard).
- Functional Customization
-
- Self-lubricating gaskets: Embedded molybdenum disulfide particles, friction power consumption reduced by 30% (high-speed equipment).
-
- Smart monitoring seals: Integrated pressure sensor slots, accuracy ±1%FS (industrial IoT scenarios).
- Tolerance Design
-
- Static seal compression rate controlled at 15%–30%, dynamic seal fit clearance ≤0.1mm (per GB/T 20082 standard).
2. Precise Material Selection
- Automotive Engine Sealing: FKM material, resistant to 150℃ high temperature and fuel erosion, compliant with SAE J2005 standard.
- Drinking Water Systems: SIL material, NSF 61 certified, heavy metal leaching ≤0.1ppm.
- High-Pressure Hydraulic Systems: HNBR material, tear strength ≥25kN/m, suitable for -30℃~120℃ conditions.
3. Pre-Processing Technology
- Raw material mixing: Twin-screw extruder mixing uniformity ≥98% to ensure consistent vulcanization performance.
- Mold pre-treatment: Teflon release agent coating reduces demolding force by 50%, minimizing surface defects.
(B) Production and Quality Control
1. Flexible Manufacturing Capability
- Rapid Prototyping
-
- 3D printed silicone samples delivered in 24 hours, mold development cycle 7–15 days (simple mold).
-
- Supports minimum order quantity of 100 pieces for small-to-medium batch customization.
- Mass Production
-
- Intelligent production lines: Equipped with visual inspection robots, dimensional detection accuracy ±0.03mm, defect recognition rate ≥99.5%.
-
- Capacity: 100,000 pieces/day for standard O-rings (compression molding), 50,000 pieces/day for medical-grade seals (LSR injection).
2. Comprehensive Inspection System
- Sealing Performance
-
- Water pressure test: 1.5x rated pressure for 30 minutes, pressure drop ≤1% (GB/T 14153 standard).
-
- Air tightness test: 50kPa pressure maintained for 10 minutes, leakage ≤5ml/min.
- Physical Properties
-
- Tensile strength/elongation at break: Compliant with GB/T 528, test accuracy ±2%.
-
- Hardness test: Shore durometer detection, tolerance ±2 Shore A (GB/T 531.1 standard).
- Environmental Performance
-
- Oil resistance test: Immersion in ASTM No.3 oil at 70℃×168h, volume change rate ≤10%.
-
- Fire resistance test: Oxygen index ≥28%, compliant with UL94 HB (special application requirements).
- Certification Support: Provides FDA, RoHS, IATF 16949, and other certification reports for global market access.
IV. Multi-Scenario Application Solutions
(A) Industrial Equipment Sector
- Valve Sealing Gaskets: EPDM material, resistant to water vapor (150℃×1000h no aging), suitable for DN50–DN1000 flange specifications.
- Compressor Seals: HNBR material, high-pressure resistance (20MPa) and ozone resistance (50pphm×100h no cracking), used in refrigeration equipment.
(B) Automotive Industry
- Engine Oil Pan Sealing: FKM + metal skeleton, resistant to 180℃ high temperature and engine oil, leakage rate ≤5×10⁻⁸ mbar·L/s.
- New Energy Vehicle Battery Sealing: SIL material, resistant to electrolyte corrosion (pH 3–11), fire rating V-0 (UL94 standard).
(C) Medical Devices
- Medical Pipeline Sealing: LSR liquid silicone rubber, ISO 10993 biocompatibility certified, extractables ≤0.01μg/ml.
- Surgical Equipment Sealing: Transparent silicone material, light transmittance ≥90%, suitable for precision instruments like endoscopes.
(D) New Energy Sector
- PV Inverter Sealing: EPDM + UV-resistant additives, weather resistance grade 4 (QUV-A 2000h color difference ΔE≤3), IP68 waterproof rating.
- Fuel Cell Sealing: Perfluoroelastomer (FFKM), resistant to 200℃ high temperature and hydrogen permeation, compliant with ISO 21247 standard.
V. Technology Selection Guide
Requirement Type
|
Preferred Technology
|
Material Selection
|
Core Indicators
|
Delivery Cycle
|
High-Pressure Sealing
|
Compression Molding + FKM
|
Fluorine Rubber
|
250℃ resistance, 20MPa pressure tolerance
|
Prototype in 5 days, mass production in 25 days
|
Food & Medical Grade
|
LSR Injection + SIL
|
Silicone Rubber
|
Non-toxic certification, biocompatibility
|
Prototype in 7 days, mass production in 30 days
|
Large-Scale Standard Production
|
Injection Molding + NBR
|
Nitrile Rubber
|
Oil resistance, cost-effective
|
Prototype in 5 days, mass production in 20 days
|
Weather & Aging Resistance
|
Extrusion Molding + EPDM
|
EPDM Rubber
|
UV resistance, water vapor resistance
|
Prototype in 6 days, mass production in 22 days
|