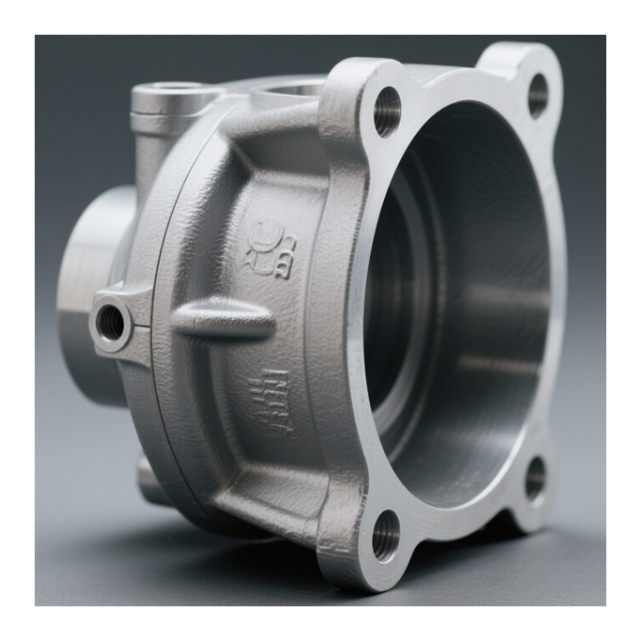
Table of Contents
- Water Pump Housing Die Castings: The Core of Fluid Conveyance Systems
- Custom Material Selection: Decoding the Material Code for Pump Housing
- Precision Manufacturing Processes: The Transformation from Liquid Metal to High – performance Pump Housings
- Core Technological Breakthroughs: Overcoming Challenges of Pressure, Corrosion, and Sealing
- Full – Process Quality Control: The Pursuit of Perfection under Strict Standards
- Agile Service System: Meeting the Diverse Needs of the Pump Industry
- Water Pump Housing Die Casting FAQs: Professional Answers to Key Customization Questions
1. Water Pump Housing Die Castings: The Core of Fluid Conveyance Systems
- High – pressure Adaptation: Capable of withstanding working pressures ranging from 0.5 – 10MPa, depending on the application. Aluminum alloy die castings, for example, require a tensile strength of ≥250MPa to ensure the housing remains intact under pressure, especially in high – lift pumping scenarios.
- Complex Structure Integration: Integrated die casting can form complex internal flow channels, mounting holes, and sealing surfaces. The tolerance of key dimensions such as hole diameters is controlled within ±0.03mm, reducing assembly processes by 30% and improving the overall sealing performance (leakage rate ≤3cc/min).
- Corrosion Resistance: Operating in various fluid environments, including tap water, seawater, and chemical solutions, the housing materials must have excellent corrosion resistance. After 1000 hours of salt spray testing, the corrosion depth of qualified pump housing die castings should be ≤15μm.
2. Custom Material Selection: Decoding the Material Code for Pump Housing
1. Main Alloy Properties and Typical Applications
Alloy Type
|
Typical Grade
|
Core Performance Indicators
|
Pump Housing Applications
|
Aluminum Alloy
|
ADC12
|
Tensile strength ≥260MPa, thermal conductivity ≥180W/(m·K), good casting fluidity
|
General water supply pumps, cooling pumps
|
Ductile Iron
|
QT400 – 18
|
Tensile strength ≥400MPa, excellent shock resistance, high pressure – bearing capacity
|
High – pressure industrial pumps, deep – well pumps
|
Stainless Steel
|
304
|
Outstanding corrosion resistance, good mechanical properties, suitable for corrosive fluids
|
Chemical pumps, seawater – resistant pumps
|
2. Custom Material Design
- Seawater – used Pumps: For pump housings used in seawater environments, adding 2 – 3% Mo to stainless steel grades can enhance pitting corrosion resistance by 40%, ensuring long – term stable operation.
- High – temperature Pumps: In aluminum alloy for high – temperature applications, incorporating 0.5% Mg and 0.3% Ni can increase the material’s strength retention rate at 200℃ by 25%, meeting the requirements of high – temperature fluid conveyance.
3. Precision Manufacturing Processes: The Transformation from Liquid Metal to High – performance Pump Housings
1. Mold Design: 0.01mm – Level Precision Control
- Flow Channel Optimization Design:
-
- Designing conformal cooling channels with a spacing of 3 – 5 times the pipe diameter to keep the mold temperature fluctuation within ±5℃, avoiding deformation caused by uneven cooling of the pump housing (shrinkage rate controlled at 0.8 – 1.2%).
-
- Using high – hardness carbide inserts (hardness HRC60) for deep – hole forming to ensure the coaxiality of 8mm deep holes is ≤0.02mm, such as for the installation of shaft sleeves.
- Mold Flow Analysis: Simulating the filling process (injection speed 40 – 60m/s) through Moldflow to optimize the gate position (≥6mm from thick – wall areas), reducing the occurrence rate of shrinkage cavities from 6% to 1%.
2. Die Casting: Pump Housing – Specific Processes
- Vacuum Die Casting Technology:
-
- Maintaining a vacuum degree of ≤80mbar, combined with two – stage pressure boosting (initial pressure 80MPa → final pressure 120MPa), to make the internal density of the pump housing ≥99.2%, and the defect rate detected by X – ray flaw detection <0.5%.
-
- Precise mold temperature control (for aluminum alloy molds, 180±3℃) to ensure that the dimensional deviation of key surfaces, such as the sealing flange, is ≤±0.03mm.
- Low – Pressure Die Casting: For ductile iron pump housings, low – pressure die casting can reduce gas porosity by 50%, improve the compactness of the casting, and enhance the overall pressure – bearing capacity.
3. Post – Processing: Function Enhancement and Precision Assurance
- Precision Machining:
-
- Machining the sealing surface of the pump housing with a five – axis CNC machine (flatness ≤0.02mm/100mm) to ensure a tight seal.
-
- Boring the impeller mounting hole (roundness ≤0.01mm) to improve the concentricity with the impeller, reducing vibration and noise during pump operation.
- Surface Treatment:
-
- Anodizing aluminum alloy pump housings (film thickness 15 – 25μm) to increase surface hardness to ≥180HV, improving wear and corrosion resistance.
-
- Applying anti – corrosion coatings to ductile iron and stainless steel housings (coating thickness 50 – 80μm), which can pass 1200 hours of salt spray testing without corrosion.
4. Core Technological Breakthroughs: Overcoming Challenges of Pressure, Corrosion, and Sealing
1. High – pressure Resistance Enhancement Technology
- Structural Reinforcement Design: Adopting a variable – wall – thickness design in high – stress areas of the pump housing, increasing the wall thickness from 3mm to 5mm, and adding triangular reinforcing ribs (height 3mm) to enhance the pressure – bearing capacity by 30%.
- Material Optimization: Through heat treatment of ductile iron, such as austempering, the tensile strength can be increased from 400MPa to 550MPa, significantly improving the high – pressure resistance of the pump housing.
2. Corrosion Prevention and Control Technology
- Composite Coating Technology: Developing a multi – layer composite coating, combining a primer layer, a middle anti – corrosion layer, and a top protective layer. This can increase the corrosion resistance of the pump housing in harsh environments by 50%, extending the service life from 5 years to 8 years.
- Electrochemical Protection: Installing sacrificial anodes on the inner surface of the pump housing for seawater – used pumps, which can reduce the corrosion rate of the housing by 60%.
3. Precision Sealing Technology
- Integrated Sealing Structure Design: Designing an integrated sealing groove in the mold, reducing the number of sealing components by 20%. The sealing groove dimensions are controlled with a tolerance of ±0.02mm, improving the sealing reliability.
- Sealing Surface Treatment: Using super – finishing technology for the sealing surface, reducing the surface roughness to Ra≤0.4μm, ensuring zero leakage under rated working pressure.
5. Full – Process Quality Control: The Pursuit of Perfection under Strict Standards
1. Raw Material Control
- Spectral Analysis: Conducting batch – by – batch alloy composition testing (accuracy 0.01%). For aluminum alloy, controlling the Si content within 11.5 – 13.5% and Fe≤1.0% to ensure stable material performance.
- Incoming Inspection: Performing visual inspection, dimensional inspection, and hardness testing on raw materials. Rejecting any materials with surface defects, out – of – tolerance dimensions, or unqualified hardness.
2. Process Monitoring
- IoT Data Collection: Real – time monitoring of injection pressure (fluctuation ≤2%), mold temperature (deviation ±2℃), and cycle time (error ≤3 seconds). Automatic alarm and machine stop for abnormal data, with a response time of ≤10 seconds.
- First Article Inspection: Using a coordinate measuring machine to measure 40 + key dimensions (Cpk≥1.33), including hole positions, wall thicknesses, and flange flatness. Only when the first article is qualified can mass production begin.
3. Finished Product Inspection
Inspection Item
|
Inspection Method
|
Strict Standard
|
Compliance Rate
|
Dimensional Accuracy
|
Coordinate Measuring Machine
|
Key dimensions ±0.03mm
|
99.7%
|
Internal Defects
|
X – ray and Ultrasonic Testing
|
0 tolerance for defects ≥0.3mm
|
100%
|
Pressure Resistance
|
Hydrostatic Pressure Testing
|
1.5 times the rated pressure for 30 minutes without leakage
|
99.5%
|
Corrosion Resistance
|
Salt Spray Testing
|
No obvious corrosion after 1000 hours
|
99.2%
|
6. Agile Service System: Meeting the Diverse Needs of the Pump Industry
1. Collaborative R&D
- Early Design Participation: Participating in the early – stage design of pump products, providing professional suggestions on housing structure, material selection, and processability. For example, optimizing the housing structure to reduce the weight by 15% without affecting performance.
- Joint Material Development: Collaborating with material suppliers to develop new materials suitable for special pump applications. Such as developing a new type of high – temperature – resistant and corrosion – resistant aluminum alloy for high – temperature chemical pumps.
2. Fast Delivery
- Rapid Prototyping: Using 3D printing and aluminum – based simple molds to deliver the first samples within 7 days, which shortens the product development cycle by 40% compared to traditional methods.
- Mass Production: Equipped with a series of die – casting machines ranging from 300T to 1000T, with a monthly production capacity of 100,000 pieces. For urgent orders, the delivery cycle can be shortened by 30%.
3. After – Sales Service
- Quality Traceability: Assigning a unique traceability code to each batch of pump housing die castings, which is associated with raw material information, production parameters, and inspection records. Enabling quick problem – solving within 24 hours.
- Technical Support: Providing on – site technical support for customers, helping to solve problems such as installation, commissioning, and maintenance. Regularly conducting customer satisfaction surveys to continuously improve service quality.