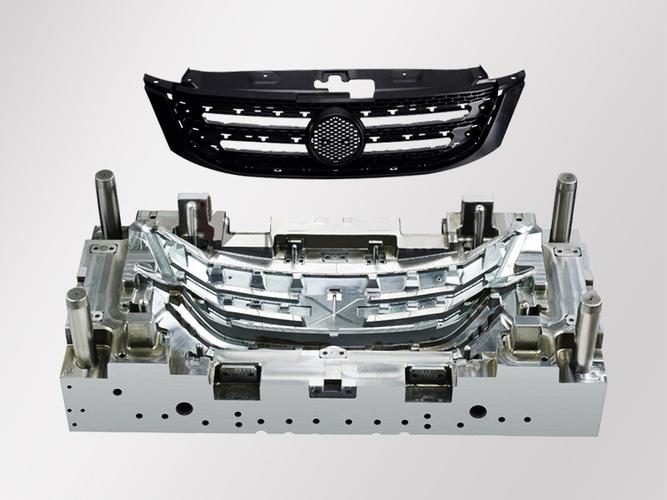
1. Why Custom Automotive Bumper Molds
2. Automotive Bumper Mold Processing Technologies
- 5-Axis CNC Milling: Shapes large, complex mold cavities with 3D contours (curved surfaces, undercuts) and tight tolerances (±0.05mm), ensuring uniform wall thickness and precise alignment of mounting features.
- EDM (Electrical Discharge Machining): Creates intricate details (sensor mounting recesses, decorative textures) in hardened steel, preserving sharp edges that transfer clearly to bumper surfaces during molding.
- Large-Format Injection Mold Base Fabrication: Constructs robust mold bases (up to 3m in length) with integrated cooling channels, ensuring even temperature distribution across the large surface area of bumpers.
- 3D Scanning & Reverse Engineering: Captures vehicle body data to design molds that perfectly match existing contours, critical for aftermarket or replacement bumper production.
- Prototype Molding (3D Printing): Builds temporary molds or prototypes from high-temperature resins to test fit and design before final steel mold production, reducing development risks.
3. Automotive Bumper Mold Processing Flow
- Design & Engineering: Collaborate with automakers to define specifications (vehicle model, material type, safety requirements) and design goals (aerodynamics, impact resistance). Use CAD/CAE software to simulate mold flow, optimize cooling, and validate structural integrity.
- Material Selection: Choose mold materials based on production volume—P20 steel for medium runs (50,000+ units), H13 tool steel for high-volume production (100,000+ units), or aluminum for low-volume specialty vehicles.
- Mold Base Construction: Fabricate large steel frames (up to 5 tons) with guide pins, ejector systems, and cooling channel networks to maintain consistent mold temperatures (180–220°C) during injection.
- Cavity & Core Machining: Use 5-axis CNC milling to shape the mold’s cavity (bumper exterior) and core (inner surface), incorporating features like mounting bosses, reinforcement ribs, and sensor ports.
- Heat Treatment: Harden mold components to 45–50 HRC through quenching and tempering, enhancing wear resistance for prolonged use with abrasive materials (glass-filled plastics).
- Surface Finishing: Polish cavity surfaces to Ra 0.8μm or better to prevent material sticking and ensure bumper surfaces are free of defects (sink marks, flow lines).
- Assembly & Testing: Assemble mold components, then conduct trial injections with production materials to verify dimensional accuracy, surface quality, and cooling efficiency. Adjustments are made to optimize part quality.
4. Automotive Bumper Mold Materials
- P20 Tool Steel: A pre-hardened alloy steel (30–35 HRC) offering good machinability and durability, ideal for medium-volume production of bumpers for passenger cars and SUVs. Balances cost and performance for 50,000–100,000 units.
- H13 Tool Steel: A heat-resistant, high-strength steel (45–50 HRC) suitable for high-volume production (100,000+ units) and abrasive materials (GFRP, carbon-fiber composites). Resists thermal fatigue from repeated heating/cooling cycles.
- 7075 Aluminum: A lightweight option for low-volume or prototype molds, enabling faster machining and reduced energy consumption during production. Best for specialty vehicles or limited-edition models.
- Stainless Steel (420): Used for mold components exposed to corrosive materials or cleaning agents, preventing rust and ensuring long-term dimensional stability in humid production environments.
5. Automotive Bumper Mold Applications
- Passenger Cars & Sedans: Molds for sleek, aerodynamic bumpers with integrated fog lights and ADAS sensor housings, using PP or TPO (thermoplastic olefin) for impact resistance and paintability.
- SUVs & Crossovers: Heavy-duty molds for larger bumpers with reinforced ribs and tow-hook provisions, often using GFRP to balance strength and weight.
- Trucks & Commercial Vehicles: Rugged molds for bumpers with enhanced impact zones and step pads, designed to withstand heavy loads and minor collisions using high-strength composites.
- Electric Vehicles (EVs): Aerodynamically optimized molds for lightweight bumpers that reduce drag, incorporating features like charging port cutouts and underbody shielding.
- Off-Road Vehicles: Specialized molds for bumpers with winch mounts, skid plates, and rock-sliders, using thick-walled designs and impact-absorbing structures to handle off-road hazards.
6. Automotive Bumper Mold Performance Additions
- Cooling Optimization: Strategic placement of water channels (8–12mm diameter) ensures uniform cooling across large bumper surfaces, reducing cycle times by 15–20% and preventing warpage.
- Texturing & Branding: Laser-etched surface patterns (matte finishes, grain textures) or embossed logos that transfer to bumper surfaces, enhancing aesthetics and brand recognition without secondary operations.
- Insert Integration: Mold cavities designed to accommodate metal or plastic inserts (threaded bushings, sensor mounts) during injection, eliminating post-assembly steps and improving part integrity.
- Draft Angle Optimization: Precision-engineered draft angles (1–3°) on vertical surfaces to facilitate easy ejection, reducing stress on the mold and preventing damage to delicate features (grille openings).
- Impact Simulation Validation: Mold designs validated through FEA (Finite Element Analysis) to ensure bumpers meet crash-test requirements, with rib patterns optimized to absorb energy during collisions.
7. Automotive Bumper Mold Common Questions
What is the typical lifespan of a custom bumper mold?
Lifespan depends on material and production volume: H13 steel molds last 300,000–500,000 cycles; P20 steel molds 100,000–300,000 cycles; aluminum molds 50,000–100,000 cycles. Proper maintenance (cleaning, lubrication) extends life by 20–30%.
How do molds accommodate different bumper materials?
Molds are engineered with material-specific features: higher injection pressures for glass-filled plastics, specialized vents for low-viscosity TPO, and surface treatments (chrome plating) to prevent sticking with adhesives or paints.
What factors affect bumper mold cost?
Size (larger molds for trucks cost 30–50% more than car molds), complexity (integrated sensors/additional features add 20–30%), and material (H13 steel costs 40–60% more than P20). Custom molds typically range from (150,000 to )500,000+.
How long does it take to produce a custom bumper mold?
Simple molds for standard vehicles take 12–16 weeks; complex molds with integrated features or large sizes require 20–24 weeks. Rush production is possible in 8–12 weeks with expedited machining.
Can molds be modified for design changes?
Yes—modular mold designs allow for replaceable inserts (e.g., grille openings, sensor housings) to accommodate mid-cycle updates, reducing retooling costs by 40–60% compared to full mold replacement.