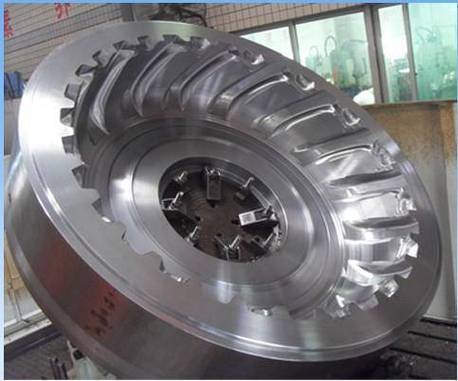
1. Why Custom Automotive Tire Molds
2. Automotive Tire Mold Processing Technologies
- 5-Axis CNC Milling: Shapes complex tread patterns, grooves, and sipes with high precision, creating 3D features (variable groove depths, asymmetric tread blocks) and ensuring uniform pattern alignment across mold segments.
- EDM (Electrical Discharge Machining): Uses electrical discharges to cut intricate details (fine sipes, micro-textures) in hardened steel, preserving sharp edges that transfer to tire rubber during vulcanization.
- Laser Engraving: Creates precise sidewall lettering, logos, and serial numbers with micron-level accuracy, ensuring consistent branding and compliance with regulatory markings (load index, speed rating).
- Segmented Mold Assembly: Fabricates molds in 2–8 interlocking segments (depending on tire size) that fit together seamlessly, allowing easy removal of finished tires while maintaining pattern continuity.
- 3D Scanning & Reverse Engineering: Captures existing tire designs or prototypes to replicate or modify mold patterns, accelerating development for retrofits or design iterations.
3. Automotive Tire Mold Processing Flow
- Design & Engineering: Collaborate with tire manufacturers to define specifications (tread pattern, tire size, load capacity) and performance goals (wet grip, noise reduction). Use CAD and simulation software to optimize tread block geometry and predict wear patterns.
- Material Selection: Choose high-strength steel alloys based on production volume and tire type—S50C or 42CrMo for standard tires; H13 tool steel for high-volume or performance tire molds requiring superior wear resistance.
- Segment Fabrication: Cut mold segments from steel blocks using CNC cutting machines, then machine mating surfaces to ensure tight alignment (gap < 0.05mm) when assembled.
- Pattern Machining: Use 5-axis CNC milling and EDM to cut tread grooves, sipes, and sidewall details into each segment, ensuring pattern consistency across all mold sections.
- Heat Treatment: Harden mold segments through quenching and tempering to achieve surface hardness (45–50 HRC), enhancing wear resistance during repeated vulcanization cycles (up to 100,000+ tires).
- Finishing & Polishing: Smooth mold surfaces to Ra 1.6μm or better, preventing rubber sticking and ensuring clean transfer of tread patterns to the tire.
- Assembly & Testing: Assemble segments into a complete mold, then test with rubber samples to verify pattern clarity, dimensional accuracy, and pressure distribution during vulcanization.
4. Automotive Tire Mold Materials
- 42CrMo Alloy Steel: A medium-carbon alloy steel offering good strength (800–1000 MPa tensile) and machinability, ideal for standard passenger car tire molds with moderate production volumes (50,000–100,000 tires).
- H13 Tool Steel: A hot-work tool steel with excellent heat resistance and toughness, suitable for high-volume production (100,000+ tires) or performance tires requiring repeated exposure to vulcanization temperatures (160–180°C).
- S50C Carbon Steel: A cost-effective option for low-to-medium volume molds, providing adequate hardness (30–35 HRC) for light-truck or entry-level passenger car tires.
- Surface Coatings: Chromium plating or nitriding treatments are applied to mold surfaces to reduce friction, enhance corrosion resistance, and extend lifespan by 30–50% in high-humidity vulcanization environments.
5. Automotive Tire Mold Applications
- Passenger Car Tires: Molds for all-season, summer, and winter tires, featuring tread patterns optimized for comfort, fuel efficiency, and wet/dry grip (e.g., symmetric patterns for quiet rides, asymmetric for sporty handling).
- Truck & SUV Tires: Heavy-duty molds for light-truck, off-road, and commercial vehicle tires, with deep tread grooves, reinforced sidewalls, and stone-ejector features to withstand heavy loads and rough terrain.
- Racing Tires: High-precision molds for Formula 1, NASCAR, or rally tires, featuring aggressive tread patterns, soft rubber compounds, and lightweight designs for maximum traction and speed.
- Specialty Tires: Molds for run-flat tires (with reinforced sidewall patterns), self-sealing tires, or eco-friendly tires (low-rolling-resistance treads), accommodating unique structural features and materials.
- Industrial & Agricultural Tires: Large-format molds for construction equipment, tractor, or forklift tires, with heavy-duty treads and reinforced casings to handle extreme loads and uneven surfaces.
6. Automotive Tire Mold Performance Additions
- Tread Pattern Optimization: Computer-aided design of variable groove depths, sipe angles, and block shapes to reduce noise (via pitch sequencing) and improve water evacuation (reducing hydroplaning risk).
- Heating Uniformity: Embedded heating elements and thermal sensors ensure consistent temperature distribution (±2°C) across the mold, preventing rubber curing inconsistencies and ensuring uniform tire hardness.
- Quick-Change Systems: Modular sidewall inserts that allow fast switching between tire sizes or branding elements, reducing downtime for manufacturers producing multiple tire models.
- Wear-Resistant Coatings: Titanium nitride (TiN) or ceramic coatings on mold surfaces to reduce friction with rubber, extending mold life and maintaining pattern sharpness over thousands of cycles.
- Alignment Precision: Precision-machined guide pins and locating holes ensure mold segments align within 0.03mm, preventing pattern misalignment that could cause tire vibration or irregular wear.
7. Automotive Tire Mold Common Questions
How long does a custom tire mold last?
Lifespan depends on material and usage: H13 steel molds last 100,000–200,000 tire cycles; 42CrMo molds 50,000–100,000 cycles. Regular maintenance (cleaning, re-polishing) can extend life by 20–30%.
What factors affect tire mold cost?
Complexity (tread pattern intricacy, number of segments), material (H13 steel costs 30–50% more than 42CrMo), and size (larger molds for 22-inch+ tires) drive costs. Custom molds typically range from (50,000 to )200,000+.
How long does it take to produce a custom tire mold?
Simple molds for standard tires take 8–12 weeks; complex molds with intricate tread patterns or large sizes (truck tires) require 16–20 weeks. Rush production is possible in 6–10 weeks with expedited machining.
Can one mold produce multiple tire sizes?
No—molds are engineered for specific tire dimensions (diameter, width, aspect ratio). However, modular sidewall inserts can adapt a mold to different branding or size markings within the same tire specification (e.g., 225/50R17 vs. 225/55R17).
How do molds impact tire performance?
Tread pattern accuracy directly affects grip and noise; uniform mold heating ensures consistent rubber curing, preventing soft spots that reduce durability. Precise alignment eliminates tread irregularities that cause vibration or uneven wear.