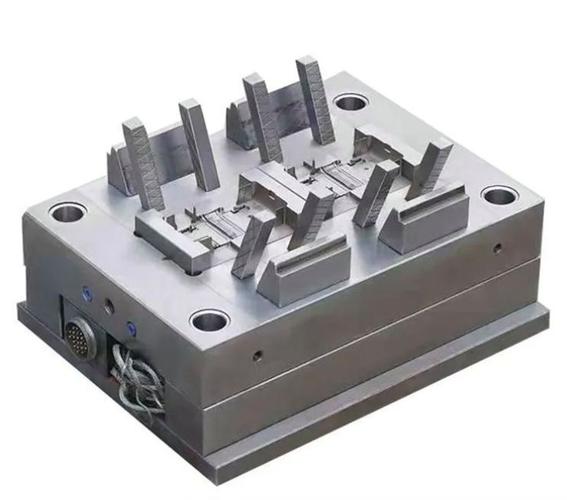
1. Why Custom Plastic Bottle Injection Molds
2. Plastic Bottle Injection Mold Processing Technologies
- CNC Milling (3-Axis & 5-Axis): Shapes mold cavities and cores from solid blocks, creating precise bottle contours, threads, and surface details. 5-axis milling handles complex curves (e.g., hourglass-shaped bottles) in one setup, ensuring accuracy.
- EDM (Electrical Discharge Machining): Uses electrical discharges to cut intricate features like fine threads or embossed text in hardened steel, achieving tolerances as tight as ±0.002mm—critical for leak-proof bottle necks.
- Wire EDM: Cuts thin sections or sharp edges (e.g., bottle lip seals) with minimal material waste, ideal for molds requiring precise parting lines to avoid flash (excess plastic).
- Polishing: Finishes mold cavities to mirror-like surfaces (Ra 0.02μm) to ensure bottles have smooth exteriors, enhancing printability for labels or decorations.
- 3D Printing: Rapidly prototypes mold inserts or cavity prototypes for design testing, allowing quick adjustments before final mold production.
3. Plastic Bottle Injection Mold Processing Flow
- Design & Engineering: Collaborate with clients to finalize bottle specs (volume, dimensions, wall thickness) and production goals (volume, material type). Use CAD software to design mold cavities, cores, and cooling channels, with FEA simulations to optimize plastic flow and cooling.
- Material Selection: Choose mold materials based on production volume—aluminum for low runs (10,000–100,000 bottles), pre-hardened steel for medium runs (100,000–1 million), and hardened steel for high runs (1 million+).
- Mold Base Fabrication: Machining the mold base (frame) to house cavities, cores, and guide pins, ensuring structural stability during high-pressure injection.
- Cavity & Core Machining: Using CNC milling and EDM to shape the mold’s cavity (bottle exterior) and core (bottle interior), including details like threads, logos, and texture.
- Cooling System Integration: Drilling or milling channels to circulate coolant (water or oil) around cavities, ensuring uniform cooling and reducing cycle times.
- Polishing & Assembly: Polishing cavity surfaces to desired finish, then assembling components (ejector pins, guide bushings) to ensure smooth operation.
- Testing & Validation: Trial runs with plastic resin (PET, HDPE) to check for defects (warping, thin walls), adjusting mold dimensions or cooling as needed. Final inspections verify dimensional accuracy and part quality.
4. Plastic Bottle Injection Mold Materials
- Aluminum Alloys (7075, 6061): Lightweight and cost-effective for low to medium production runs. Offers good thermal conductivity for faster cooling but wears faster than steel—ideal for prototypes or short-run specialty bottles.
- Pre-Hardened Steel (P20, 718): Balances durability and machinability for medium runs (100,000–1 million bottles). Hardness (30–40 HRC) resists wear while allowing precision machining of fine details.
- Hardened Steel (H13, S136): High hardness (50–55 HRC) and corrosion resistance make it suitable for high-volume production (1 million+ bottles) or harsh resins (acids, solvents). S136 offers superior polishability for clear bottles.
- Beryllium Copper: Excellent thermal conductivity (faster cooling than steel) and wear resistance, used for molds requiring rapid cycle times (e.g., water bottle production lines).
5. Plastic Bottle Injection Mold Applications
- Beverage Industry: Molds for water bottles, soda bottles, and juice containers (PET or HDPE), featuring precise neck threads for cap sealing and lightweight designs to reduce material use.
- Cosmetics & Personal Care: Molds for shampoo bottles, lotion containers, and perfume vials, with custom shapes (oval, triangular) and surface textures (matte, glossy) to enhance brand appeal.
- Food Packaging: Molds for sauce bottles, oil containers, and condiment jars, using food-grade materials (FDA-approved steel) and leak-proof neck designs.
- Household & Cleaning Products: Molds for detergent bottles, spray bottles, and disinfectant containers, engineered to withstand chemical exposure and heavy use.
- Pharmaceuticals: Molds for pill bottles and liquid medicine containers, with child-resistant cap threads and tamper-evident features, meeting strict regulatory standards.
6. Plastic Bottle Injection Mold Performance Additions
- Ventilation Systems: Microscopic vents in mold cavities to release trapped air, preventing burn marks or incomplete filling—critical for complex bottle shapes.
- Hot Runner Systems: Heated channels that keep plastic molten in the mold, reducing waste (no cold sprues) and enabling faster cycle times for high-volume production.
- Texturing: Laser etching or chemical etching to add surface patterns (branding, grip textures) directly into mold cavities, eliminating post-production labeling steps.
- Quick-Change Inserts: Modular cavity inserts that allow switching between bottle sizes or designs without retooling the entire mold, ideal for brands with multiple product lines.
- Corrosion Resistance: Chrome plating or nitriding for molds processing acidic or abrasive resins (e.g., citrus juice bottles), extending mold life by 50%+.
7. Plastic Bottle Injection Mold Common Questions
How long does a custom plastic bottle mold last?
Aluminum molds last 10,000–100,000 cycles; pre-hardened steel 100,000–1 million; hardened steel 1 million+ cycles. Lifespan depends on resin type (abrasive additives shorten life) and maintenance.
What’s the typical cycle time for bottle production?
Small bottles (50–200ml) take 5–10 seconds per cycle; large bottles (1–5L) take 15–30 seconds. Custom cooling systems can reduce cycle times by 20–30%.
Can molds produce clear bottles?
Yes—using polished hardened steel (S136) or beryllium copper molds ensures the high surface finish needed for clarity. Proper cooling prevents clouding in materials like PET.
How much does a custom mold cost?
Small single-cavity molds (cosmetic bottles) start at (5,000–)15,000; large multi-cavity molds (beverage bottles) range from (50,000–)200,000+. Costs depend on size, cavities, and material.
Can molds be modified for design changes?
Yes—modular molds with replaceable inserts allow updates to bottle details (logo, neck size) without full replacement. Major shape changes may require new cavity/core machining.