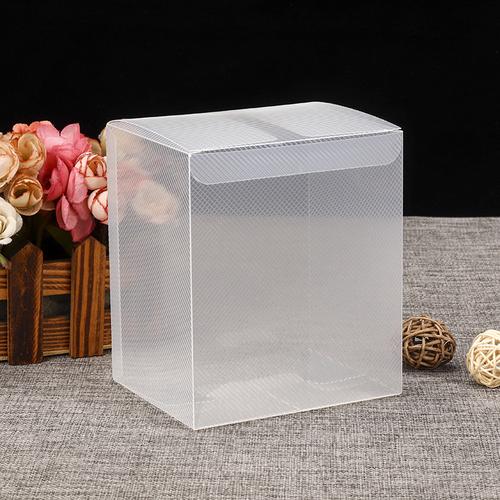
Core Technologies: Engineering for Clarity & Function
1. High-Clarity Plastic Molding
- Injection molding for rigid boxes: Uses precision molds (Ra ≤0.02μm) to produce PET/PVC boxes with 92-95% light transmittance. A 150×100×50mm cosmetic box achieved ±0.05mm tolerance, ensuring tight lid closure and stackability.
- Thermoforming for flexible shapes: Creates curved or irregular transparent boxes (e.g., blister packs for electronics) with 0.2-1.0mm uniform thickness, reducing material waste by 30% vs. injection molding.
- Ultrasonic welding: Bonds multi-piece transparent boxes (e.g., 2-piece gift boxes) with 0.1mm seam accuracy, maintaining clarity without visible adhesives.
2. Precision Printing & Branding
- UV digital printing: Delivers 1200dpi full-color graphics on transparent surfaces, with scratch-resistant (3H pencil test) and fade-resistant (ΔE ≤1 after 1000h UV) properties. A skincare box with gradient logo retained vibrancy through 500+ handling cycles.
- Silk screening: Applies opaque/metallic inks (gold, silver) to PET boxes, creating premium contrasts for luxury brands. A chocolate box with silk-screened gold foil accents achieved 98% color consistency across 10,000 units.
- Hot stamping: Adds metallic finishes (aluminum, copper) to PVC boxes, ideal for cosmetic and confectionery packaging—adhesion tested to withstand 100+ rubs without peeling.
3. Surface Treatment & Functional Enhancement
- Anti-scratch coating: Applied to PET/PP boxes, increasing surface hardness to 4H (from 2H) and reducing visible scratches by 60% during shipping.
- Anti-fog treatment: For food packaging (e.g., bakery boxes), prevents condensation (≤5g/m²/24h water vapor transmission), maintaining clarity for 30+ days.
- Matte finish Partial matte finish: Creates tactile contrast on transparent boxes (e.g., matte logo on glossy base), enhancing brand recognition without compromising clarity.
4. Quality Testing for Transparency & Durability
- Light transmittance testing: Ensures ≥90% light transmittance for clear boxes, with haze ≤2% (measured via spectrophotometer) to showcase products clearly.
- Dimensional inspection: CMM verifies critical dimensions—box width/height (±0.1mm), lid fit (gap ≤0.2mm)—preventing product jamming or looseness.
- Impact resistance: Drop tests (1.2m onto concrete) confirm no cracking for rigid boxes; flex tests (180° bending) validate durability of thin-walled blister packs.
Material Expertise: Matching Transparent Plastics to Packaging Needs
Material
|
Key Properties
|
Application
|
Advantages
|
PET (Polyethylene Terephthalate)
|
High clarity (92% transmittance), recyclable, 120℃ heat resistance
|
Food trays, cosmetic boxes, electronic packaging
|
Shatter-resistant; FDA-compliant for direct food contact.
|
PVC (Polyvinyl Chloride)
|
Excellent printability, rigid, low cost
|
Gift boxes, toy packaging, stationery cases
|
Vibrant color retention; ideal for complex shapes.
|
PP (Polypropylene)
|
Impact-resistant, microwave-safe, 130℃ heat resistance
|
Snack boxes, bakery containers, reusable packaging
|
BPA-free; withstands hot filling (≤100℃).
|
PS (Polystyrene)
|
Ultra-clear (95% transmittance), low density
|
Candy boxes, jewelry packaging, small-item blisters
|
Glossy finish; cost-effective for high-volume orders.
|
Transparent Packaging Box Machining Technologies
- Precision injection molds: CNC-machined aluminum/steel molds with mirror polishing (Ra ≤0.01μm) ensure box surfaces are free of defects (e.g., flow lines, bubbles) that reduce clarity.
- UV digital printing systems: 6-color printers with 1200dpi resolution achieve photo-quality graphics on transparent PET/PVC, with in-line UV curing for instant adhesion.
- Automated thermoforming lines: Vacuum-forming machines produce 500+ thin-walled blister packs/min with consistent thickness (±0.05mm), critical for product visibility.
Custom Transparent Packaging Box Manufacturing Process
- Design & DFM: Engineers optimize client 3D models (STEP/IGS) for moldability—e.g., adding 0.5° draft angles to box walls for easy demolding without surface scratches.
- Material selection: Recommend PET for food, PVC for print-heavy designs, or PP for reusable packaging based on product type and shelf life.
- Mold fabrication: CNC machining creates precision molds with cooling channels optimized to prevent clouding (e.g., in PET boxes).
- Injection/thermoforming: Molding processes produce box bases/lids with 90%+ transmittance; automated trimming removes excess material.
- Printing & coating: UV digital printing or silk screening applies branding; anti-scratch/anti-fog coatings added per application.
- Quality validation: Light transmittance testing, dimensional inspection, and impact trials ensure compliance with client specs.
Custom Transparent Packaging Box Application Fields
- Food industry: PET trays for fruits/vegetables (breathable), PP boxes for baked goods (microwave-safe), PS candy containers (ultra-clear).
- Cosmetics & personal care: PVC/PET boxes for skincare sets (with UV printing), transparent acrylic-like cases for perfume bottles.
- Electronics & gadgets: Anti-static PET blisters for headphones, clear boxes for charging cables (with window patching for barcodes).
- Gifts & crafts: Custom-shaped PVC boxes for jewelry (with velvet inserts), transparent magnetic closure boxes for luxury gifts.
Customization Capabilities: From Concept to Shelf
- Shape & size: From 5×5×5mm (mini jewelry boxes) to 500×300×200mm (electronics packaging), with custom contours (e.g., rounded corners, die-cut windows).
- Printing & finishes: Full-color UV printing, metallic hot stamping, embossed logos, or partial matte for brand texture.
- Functional features: Magnetic closures, snap-fit lids, hang holes, or anti-fog treatment for refrigerated products.
- Eco-friendly options: Recyclable PET (rPET) with 30% recycled content, biodegradable additives, or compostable PLA blends.
Common Processing Questions
- Q: How to prevent print bleeding on transparent boxes?
- Q: What’s the minimum order quantity for a custom-shaped PET box?
- Q: Can transparent boxes withstand refrigeration (-5℃) or heat (60℃)?
- Q: How to ensure the box lid fits tightly without gaps?
Why Choose Goldcattle?
- Expertise: 26 years in transparent packaging, with 500+ custom designs for global brands (L’Oréal, Nestlé, Samsung).
- Quality: 100% inspection for clarity (haze ≤2%), print accuracy (ΔE ≤1), and dimensional fit; FDA/ISO 22000 certified for food contact.
- Efficiency: Automated lines produce 1M+ boxes/month; digital printing reduces setup time by 50% for small batches.
- Sustainability: Offer recyclable (PET/PP) and biodegradable options; carbon-neutral production lines reduce environmental impact.