Customized brass CNC turned parts serve as precision components in electronics, automotive, medical devices, and high-end manufacturing, leveraging the unique properties of brass alloys to deliver superior conductivity, corrosion resistance, and aesthetic appeal. Through precise material selection, advanced CNC turning technologies, and end-to-end customization processes, we provide tailored solutions for complex geometries and high-precision requirements, ensuring optimal performance across diverse industries.
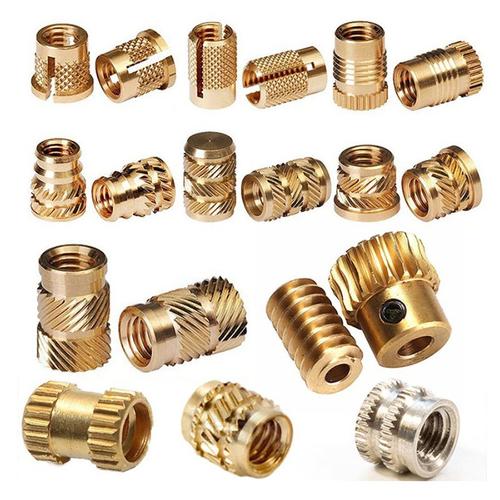
I. Core Material Properties and Application Advantages
(A) Performance Comparison of Mainstream Brass Alloys
Material Grade | Density (g/cm³) | Tensile Strength (MPa) | Hardness (HV) | Conductivity (IACS%) | Salt Spray Resistance (h) | Core Advantages | Typical Certifications |
---|---|---|---|---|---|---|---|
H65 Brass | 8.40 | 390 | 100 | 28 | ≥800 (Nickel Plated) | Easy to machine, good plasticity, cost-balanced | EN 12164 Copper Product Certification |
H70 Brass | 8.50 | 410 | 120 | 26 | ≥1000 (Gold Plated) | High gloss, stress corrosion resistance | ASTM B134 Standard Certification |
HPb59-1 Leaded Brass | 8.50 | 420 | 130 | 24 | ≥600 | Excellent machinability, self-lubricating | RoHS Environmental Certification |
HSn62-1 Tin Brass | 8.45 | 380 | 110 | 22 | ≥1200 | Seawater corrosion resistance, wear resistance | ISO 4274-1 Processing Standard |
(B) Driving Forces of Customization Requirements
- Precision Machining Needs
- Dimensional accuracy: Shaft diameter tolerance ±0.005mm (e.g., aerospace plug pins), thread accuracy up to ISO 4H/6g grade.
- Surface roughness: Ra≤0.8μm (medical catheter connectors), mirror polishing up to Ra≤0.2μm.
- Functional Performance Requirements
- Electrical conductivity: Contact resistance ≤5mΩ (electronic connectors) for high-frequency signal transmission.
- Pressure bearing capacity: Hydraulic components withstand ≥10MPa, leakage rate ≤1×10⁻⁹ mbar·L/s (helium mass spectrometer detection).
- Environmental Adaptability
- Corrosion resistance: Neutral salt spray test ≥720 hours without rust (outdoor hardware).
- Temperature range: Dimensional stability ≤±0.01% in -40℃~120℃ environment (automotive sensor components).
II. Analysis of Four Core Processing Technologies
(A) CNC Turning: High-Precision Rotational Part Machining
- Technical Advantages
- 5-axis 联动 CNC machining centers achieve complex surface one-step forming (e.g., spiral gears, eccentric shafts) with accuracy up to ±0.005mm.
- Supports micro-part machining (diameter ≥0.5mm), suitable for precision fields like watch movements and medical micro-catheters.
- Process Parameters
- Spindle speed: 2000-8000rpm (brass bar stock), feed rate 0.05-0.3mm/r.
- Tool selection: PCD diamond tools (surface roughness Ra≤0.4μm), carbide tools (wear-resistant machining).
- Cooling system: Water-soluble cutting fluid reduces temperature rise, ensuring thermal deformation ≤0.003mm.
(B) Surface Treatment Technologies
Process Type | Typical Application Scenarios | Technical Highlights |
---|---|---|
Gold/Silver Plating | Electronic connectors | Plating thickness 0.1-3μm, contact resistance reduced by 30%. |
Electroless Nickel Plating | Corrosion-resistant components | Phosphorus content 9-12%, salt spray test ≥1000 hours. |
Passivation Treatment | Medical device parts | Chromium-free passivation film thickness 2-5μm, compliant with ISO 13485 standard. |
Polishing Process | Decorative components | Vibration polishing roughness Ra≤0.2μm, glossiness ≥90GU. |
(C) Composite Machining Technologies
- Milling Integration
- Turn-mill composite machining centers achieve one-step forming of radial holes, keyways, etc., with positional accuracy ±0.01mm.
- Processing efficiency of polygonal shafts increased by 50%.
- Thread Machining
- Whirlwind milling for high-precision threads (pitch accuracy ±0.002mm), surface hardness increased by 20%.
- Supports customization of M1-M30 metric threads and UN/BSW imperial threads.
(D) Inspection and Quality Control
- Precision Measurement
- Coordinate Measuring Machine (CMM) detects geometric tolerances (roundness ≤0.002mm, perpendicularity ≤0.005mm).
- Laser diameter gauge monitors machining dimensions in real time with 100 times/second data acquisition.
- Nondestructive Testing
- Eddy current flaw detection for internal cracks (minimum detection size ≥0.1mm).
- Air tightness test (50kPa pressure maintained for 10 minutes, leakage ≤5ml/min).
III. Full-Process Customization Solutions
(A) Design and Material Engineering
- Multi-Dimensional Design Support
- Structural Optimization
- Stress distribution analyzed via ANSYS simulation, optimized fillet radius R≥0.5mm for stepped shafts, fatigue life increased by 40%.
- Progressive turning for thin-walled parts (wall thickness ≥0.8mm), deformation ≤0.008mm.
- Functional Customization
- Elastic contact structure for conductive components, insertion life ≥10,000 cycles (contact force decay ≤15%).
- Passivation treatment for medical components, heavy metal leaching ≤0.1ppm (compliant with USP Class VI standard).
- Precise Material Selection
- Electronics: H70 brass + gold plating (conductivity ≥26%IACS, contact resistance ≤3mΩ).
- Marine Engineering: HSn62-1 tin brass (seawater corrosion resistance, salt spray test ≥1200 hours).
- High-End Decoration: HPb59-1 leaded brass + mirror polishing (surface hardness ≥130HV, glossiness ≥85GU).
- Pre-Processing Technology
- Material annealing: Stress relief at 520℃ for 1 hour, machining deformation rate ≤0.02%.
- Tool coating: TiAlN coating reduces friction coefficient to 0.05, tool life extended by 3 times.
(B) Production and Quality Control
- Flexible Manufacturing Capability
- Rapid Prototyping
- 3D printed brass samples delivered in 24 hours, CNC first article processing cycle 3 days.
- Supports single-piece customization (e.g., aerospace prototypes), minimum order quantity 1 piece.
- Mass Production
- Automated production lines with gantry robots, single machine daily capacity 5000 pieces (standard shaft parts).
- Intelligent scheduling system optimizes delivery time, batch order cycle reduced by 20%.
- Comprehensive Inspection System
- Mechanical Properties
- Tensile test: Yield strength ≥200MPa (ISO 6892 standard), elongation ≥30%.
- Torque test: Connecting components bear ≥50N·m (GB/T 3098.1 standard).
- Environmental Performance
- Thermal cycling: -40℃~80℃ for 50 cycles, dimensional change rate ≤0.03%.
- Wear test: Friction wear ≤0.005mm (100,000 cycles, ASTM G99 standard).
- Certification Support: Provides ISO 9001, RoHS, REACH and other certification reports, compliant with EU/North American market access requirements.
IV. Multi-Scenario Application Solutions
(A) Electronics and Communications
- High-Frequency Connectors
- H65 brass turned pins with 3μm gold plating, insertion loss ≤0.1dB (10GHz band).
- Tolerance control ±0.003mm, adapted to high-density PCB spacing requirements.
- Relay Components
- Tin-phosphor bronze spring sheets (conductivity ≥15%IACS), service life ≥100,000 cycles, contact reliability ≥99.9%.
(B) Medical Devices
- Surgical Instrument Shafts
- HPb59-1 leaded brass + passivation treatment, surface roughness Ra≤0.4μm, compliant with ISO 13485 sterilization requirements.
- Stepped shaft fit accuracy H7/g6 ensures smooth opening/closing without jamming.
- Medical Catheter Connectors
- Thin-walled tube (wall thickness 1.2mm) machining accuracy ±0.005mm, airtightness test leakage rate ≤1×10⁻¹⁰ mbar·L/s.
(C) Automotive and Aviation
- Fuel System Components
- HSn62-1 tin brass oil pipe connectors, fuel corrosion resistance (volume change rate ≤2%), pressure resistance ≥15MPa.
- Thread accuracy 6H/6g, adapted to ISO 8434-1 standard interfaces.
- Aviation Instrument Gears
- Brass worm and worm gear, tooth surface roughness Ra≤0.8μm, transmission efficiency ≥90%, vibration resistance (10-2000Hz, 5g acceleration).
(D) High-End Decoration and Luxury Goods
- Watch Components
- H70 brass crown with mirror polishing Ra≤0.2μm, 2μm rose gold plating, salt spray test ≥800 hours.
- Engraving process achieves 0.05mm depth LOGO with accuracy ±0.01mm.
- Furniture Hardware
- Brass hinge cores with aged treatment simulation ≥95%, opening/closing life ≥50,000 cycles, noise ≤30dB.
V. Technology Selection Guide
Requirement Type | Preferred Technology Combination | Material Selection | Core Indicators | Delivery Cycle |
---|---|---|---|---|
Ultra-High-Precision Electronics | 5-axis CNC + Gold Plating | H70 Brass | Accuracy ±0.005mm, contact resistance ≤3mΩ | Prototype in 5 days, mass production in 25 days |
Corrosion-Resistant Marine Components | Turn-Mill Composite + Passivation | HSn62-1 Brass | Salt spray ≥1200h, pressure resistance 15MPa | Prototype in 7 days, mass production in 30 days |
Large-Scale Standard Parts | Automatic Lathe + Electroplating | HPb59-1 Brass | Cost ≤$0.7/unit, service life 100,000 cycles | Prototype in 3 days, mass production in 20 days |
High-End Decorative Parts | Precision Turning + Polishing | H65 Brass | Glossiness ≥90GU, wear resistance 500 cycles | Prototype in 6 days, mass production in 28 days |
Xiamen Goldcattle, a national high-tech enterprise with 26 years of manufacturing experience, specializes in customized brass CNC turned parts. Equipped with 5-axis CNC machines (tolerance ±0.005mm) and full-range surface treatment capabilities, we provide end-to-end solutions from design to mass production. Our certifications include ISO 9001, RoHS, and CE, ensuring compliance with global standards. Whether for prototyping or large-scale production, we support customization based on drawings/samples and guarantee on-time delivery.
For more information, visit our official website: https://www.xmgoldcattle.com/ to explore our precision machining capabilities and request a tailored quote.