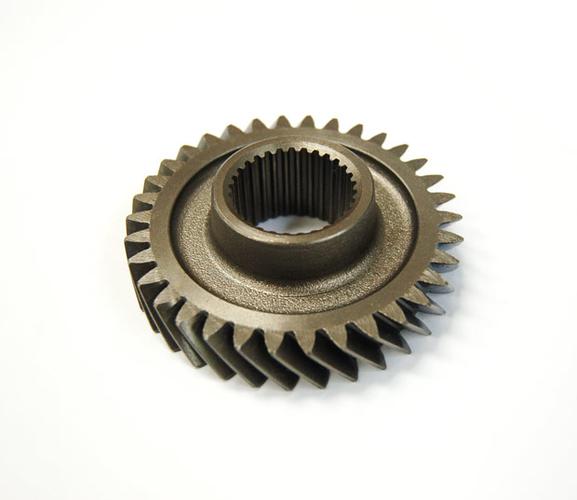
1. Why Custom Engine Gear Parts
2. Engine Gear Parts Processing Technologies
- Hobbing: Uses a rotating hob (cutting tool) to create gear teeth, ideal for high-volume production of spur and helical gears. Ensures precise tooth spacing and profile accuracy (±0.02mm) for smooth engagement.
- Shaping: Employs a reciprocating cutter to form gear teeth, suitable for internal gears, splines, or gears with complex profiles (bevel gears). Effective for low-to-medium volume production with tight tolerances.
- Grinding: Finishes gear teeth with abrasive wheels to achieve ultra-smooth surfaces and precise dimensions, critical for high-speed gears (turbochargers) where minimal friction is essential. Reduces noise and wear.
- Broaching: Uses a multi-tooth broach to cut internal gears or splines in a single pass, offering high productivity for simple tooth profiles. Ideal for Mass production of small to medium gears.
- Lapping: Polishes gear teeth with abrasive compounds, improving surface finish and reducing friction. Often used for high-precision gears in aerospace or racing engines to enhance durability.
- 3D Printing (Additive Manufacturing): Emerging for prototyping or low-volume production of complex gear geometries (e.g., lightweight, Hollow out designs), using metal powders (steel, titanium) to build gears with internal features.
3. Engine Gear Parts Processing Flow
- Design & Engineering: Collaborate with clients to gather engine specs (power, speed, torque) and gear requirements (ratio, dimensions). Use CAD and gear simulation software to optimize tooth profile, material stress distribution, and backlash (clearance between teeth).
- Material Selection: Choose metals based on engine demands—high-carbon steel for strength, alloy steel for durability, or case-hardened steel for a hard surface and tough core.
- Blank Preparation: Cut raw material (bars, sheets) into gear blanks using sawing or cutting machines, ensuring consistent dimensions for subsequent processing.
- Rough Machining: Shape blanks into gear forms (bore, hub, outer diameter) using turning or milling, creating a base for tooth cutting.
- Tooth Cutting: Use hobbing, shaping, or broaching to cut teeth, ensuring precise geometry and spacing. Helical gears require angle adjustment to match helix angle specifications.
- Heat Treatment: Apply processes like carburizing (hardens tooth surfaces), quenching, and tempering to enhance hardness (58–62 HRC for high-wear applications) and toughness, preventing tooth breakage.
- Finishing: Grind teeth to refine surface finish and dimensional accuracy, then lap if needed to reduce friction. Deburr edges to prevent stress concentration and improve safety.
- Inspection & Testing: Use gear measurement machines (GMM) to check tooth profile, pitch, and runout. Conduct hardness testing, fatigue testing, and noise/vibration analysis to ensure performance.
4. Engine Gear Parts Materials
- High-Carbon Steel (1045, 1060): Offers good strength and wear resistance, suitable for low-to-medium load gears in automotive engines. Cost-effective and easy to machine.
- Alloy Steel (4140, 4340): Contains chromium, molybdenum, or nickel to enhance strength, toughness, and hardenability. Ideal for high-torque gears in diesel engines and industrial machinery.
- Case-Hardened Steel (1018, 8620): Features a hard, wear-resistant surface (carburized layer) and a tough core, perfect for gears with high contact stress (transmission gears, camshaft gears).
- Stainless Steel (304, 440C): Resists corrosion and high temperatures, used in marine engines or engines exposed to moisture (e.g., generator sets). 440C offers high hardness for wear resistance.
- Powder Metallurgy Alloys: Sintered metal powders create gears with controlled porosity, allowing for lubricant retention. Suitable for small, low-load gears in auxiliary engine systems (oil pumps).
5. Engine Gear Parts Applications
- Automotive Engines: Spur gears in timing systems, helical gears in transmissions, and bevel gears in differential units, using alloy steel for balance of strength and machinability.
- Diesel Engines: Heavy-duty gears in fuel injection systems and crankshaft drives, made from case-hardened steel to withstand high torque and heat.
- Industrial Engines: Large helical gears in generator sets and pump drives, using forged alloy steel for durability under continuous operation.
- Marine Engines: Corrosion-resistant stainless steel gears in propulsion systems, ensuring reliable performance in saltwater environments.
- Racing & High-Performance Engines: Precision-ground, lightweight gears (titanium or alloy steel) in racing transmissions, optimized for high speed and minimal backlash to reduce power loss.
6. Engine Gear Parts Performance Additions
- Surface Coatings: Apply DLC (Diamond-Like Carbon) coatings to reduce friction and wear, extending gear life by 50–70% in high-speed applications.
- Precision Balancing: Dynamically balance gears to reduce vibration at high speeds, minimizing noise and stress on bearings (critical for racing engines).
- Tooth Profile Optimization: Use modified involute profiles (e.g., tip relief) to reduce stress concentration at tooth tips, preventing premature failure under heavy loads.
- Heat Resistance Enhancement: Alloying with molybdenum or tungsten improves resistance to high temperatures (up to 600°C), suitable for turbocharged engines.
- Lubrication Grooves: Add internal or surface grooves to retain lubricant, ensuring continuous oil film between teeth and reducing friction in low-lubrication environments.
7. Engine Gear Parts Common Questions
How long do custom engine gears last?
Lifespan depends on material, load, and maintenance: alloy steel gears in automotive engines last 150,000–200,000 km; case-hardened steel gears in industrial engines can exceed 10,000 operating hours. High-stress applications (racing) may reduce lifespan by 30–40%.
Can custom gears reduce engine noise?
Yes—by optimizing tooth profile (helical vs. spur) and backlash, custom gears can reduce noise by 20–40% compared to standard gears. Precision grinding and balancing further minimize vibration-related noise.
What materials work best for high-torque engines?
Alloy steel (4340) or case-hardened steel (8620) are ideal, as they combine high tensile strength (1,000+ MPa) and surface hardness (58+ HRC) to withstand heavy loads without tooth deformation.
How are gears tested for durability?
They undergo fatigue testing (repeated load cycles to simulate engine operation), torque testing (to verify strength), and wear testing (abrasion resistance under lubricated conditions). Gears for critical applications also undergo metallurgical analysis to check for internal defects.
Is customization cost-effective for small batches?
Yes—while tooling costs (hobs, cutters) exist, modern CNC machining and 3D prototyping reduce setup time for small batches. Custom gears prevent costly engine damage from ill-fitting standard gears, offsetting initial expenses.