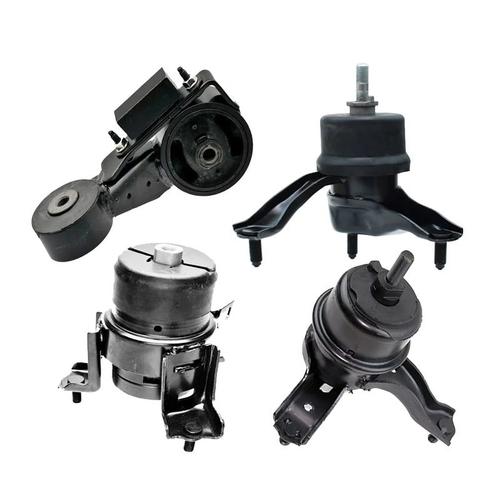
1. Why Custom Engine Mount Parts
2. Engine Mount Parts Processing Technologies
- CNC Machining: Uses computer-controlled tools to precision-cut metal mounts (steel, aluminum) from solid blocks, ensuring tight tolerances (±0.05mm) for critical attachment points. Ideal for high-strength, load-bearing components.
- Injection Molding: Shapes rubber or polymer composites into flexible mount elements (vibration dampers) by injecting molten material into molds. Allows for complex geometries and consistent material properties.
- Casting (Sand or Die): Sand casting produces large, thick metal mounts (industrial engines) cost-effectively, while die casting creates intricate aluminum mounts with fine details (automotive applications).
- Forging: Compresses heated metal to enhance strength and durability, suitable for mounts in high-stress applications (racing engines, heavy machinery). Reduces internal defects, improving resistance to fatigue.
- Bonding Processes: Adhesively bonds metal plates to rubber/polymer layers, creating hybrid mounts that combine rigidity (metal) and vibration absorption (rubber). Ensures strong, durable bonds even under thermal stress.
3. Engine Mount Parts Processing Flow
- Design & Engineering: Collaborate with clients to gather engine specs (weight, dimensions, vibration data) and application requirements. Use CAD and FEA (Finite Element Analysis) to model stress points, vibration absorption, and load distribution, optimizing mount geometry.
- Material Selection: Choose materials (metal, rubber, composite) based on engine type and conditions. For example, high-temperature engines may use heat-resistant silicone rubber and stainless steel.
- Prototyping: Create a physical prototype using 3D printing (polymers) or CNC machining (metals) to test fit, vibration absorption, and structural integrity. Adjust design based on prototype feedback.
- Production: For metal components, use CNC machining, casting, or forging to shape parts. For rubber elements, use injection molding. Hybrid mounts undergo bonding processes to join metal and rubber layers.
- Surface Treatment: Metal parts receive anti-corrosion coatings (e.g., powder coating, zinc plating) to resist rust, especially in moist environments (marine engines).
- Assembly & Testing: Assemble mount components (if multi-part) and conduct tests: load testing (to verify weight capacity), vibration testing (to measure damping effectiveness), and thermal testing (to ensure performance under high temperatures).
- Quality Inspection: Check dimensional accuracy with CMM (Coordinate Measuring Machines), verify bond strength in hybrid mounts, and inspect for defects (cracks, uneven coating) to meet safety standards.
4. Engine Mount Parts Materials
- Metals: Steel (high strength for heavy engines), aluminum (lightweight for automotive use, corrosion-resistant), and stainless steel (heat and corrosion resistance for marine or industrial engines).
- Rubbers & Polymers: Natural rubber (good vibration absorption, cost-effective), neoprene (oil and chemical resistance, ideal for automotive), silicone rubber (high-temperature resistance, up to 200°C), and polyurethane (durability and load-bearing for industrial machinery).
- Composites: Fiber-reinforced polymers (glass or carbon fiber) combine lightweight properties with rigidity, suitable for high-performance applications (racing vehicles, aerospace auxiliary engines).
- Hybrid Materials: Metal-rubber combinations (steel plates bonded to rubber) balance structural support and vibration damping, common in passenger vehicles and generators.
5. Engine Mount Parts Applications
- Automotive Industry: Mounts for gasoline/diesel engines in cars, trucks, and SUVs, using hybrid metal-rubber designs to reduce cabin noise and vibration.
- Industrial Machinery: Heavy-duty steel or forged mounts for diesel engines in generators, pumps, and construction equipment, enduring constant high loads and harsh environments.
- Aerospace & Aviation: Lightweight aluminum or composite mounts for auxiliary engines (APUs), with strict vibration control to protect sensitive avionics.
- Marine Vessels: Stainless steel and corrosion-resistant rubber mounts for boat engines, resisting saltwater exposure and dampening vibration in hulls.
- Racing & Performance Vehicles: High-strength, low-deflection mounts (aluminum, reinforced composites) that secure engines during high-speed acceleration, reducing power loss from movement.
6. Engine Mount Parts Performance Additions
- Vibration Damping Optimization: Tuning rubber/polymer hardness (Shore A scale) to match engine vibration frequency, reducing noise and wear by 30–50% compared to standard mounts.
- Heat Resistance: Adding heat shields (metal) or using high-temperature polymers (silicone) to protect mounts from engine exhaust heat, extending service life in hot environments.
- Load-Bearing Reinforcement: Integrating ribbing or gussets in metal mounts to enhance strength without increasing weight, supporting heavier engines or sudden load spikes.
- Corrosion Protection: Applying epoxy coatings, galvanizing, or using stainless steel to resist rust in humid, salty, or chemical-exposed environments (marine, industrial settings).
- Adjustable Designs: Incorporating slotted holes or adjustable bushings to allow fine-tuning of engine alignment during installation, simplifying assembly and reducing fitment issues.
7. Engine Mount Parts Common Questions
How long do custom engine mounts last?
Lifespan depends on material and use: rubber-based mounts in passenger cars last 5–8 years; metal-forged mounts in industrial machinery can last 10–15 years. High-temperature or heavy-load applications may reduce lifespan by 20–30%.
Can custom mounts reduce engine noise effectively?
Yes—by matching rubber hardness to vibration frequency, custom mounts can reduce noise transmission by 40–60% compared to standard mounts, improving passenger comfort or workplace safety.
What materials work best for high-heat engines?
Silicone rubber (resists up to 200°C) paired with stainless steel or aluminum (heat-resistant metals) is ideal. For extreme heat (e.g., racing engines), ceramic-reinforced composites may be used.
How are mounts tested for safety?
They undergo load testing (to 150% of rated capacity), vibration testing (simulating 10,000+ hours of operation), and thermal cycling (exposing to -40°C to 120°C) to ensure durability and performance under stress.
Is customization more expensive than standard mounts?
Initial design and tooling costs are higher, but for specialized applications, custom mounts reduce long-term costs by minimizing wear on engines and surrounding components, offsetting the upfront investment.