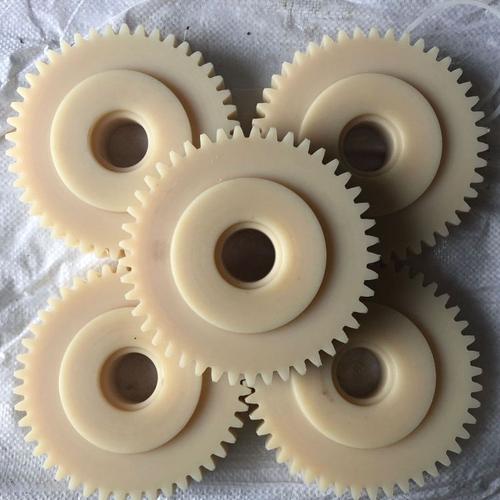
1. Why Custom Nylon Gear Parts
2. Nylon Gear Parts Processing Technologies
- Injection Molding: Melts nylon resin and injects it into precision molds under pressure, producing complex gears with tight tolerances (±0.05mm). Ideal for high-volume production, offering consistent tooth profiles and material properties.
- CNC Machining: Uses computer-controlled tools to cut gears from solid nylon blocks, suitable for low-volume or prototype production. Enables quick modifications and precise control over critical dimensions.
- 3D Printing: Builds gears layer-by-layer from nylon filaments or powders, perfect for rapid prototyping or complex geometries (internal lubrication channels, lightweight lattice structures) that are difficult to mold.
- Compression Molding: Places nylon preforms in heated molds and applies pressure to form gears, ideal for large or thick-walled parts requiring uniform density and strength.
- Laser Cutting: Uses high-powered lasers to cut gear teeth in thin nylon sheets, suitable for small, flat gears in lightweight applications like 3D printers or small appliances.
3. Nylon Gear Parts Processing Flow
- Design & Engineering: Collaborate to define specifications (tooth count, pitch, load requirements) and environmental factors (temperature range, chemical exposure). Use CAD and FEA software to simulate gear performance and optimize geometry.
- Material Selection: Choose nylon grades (PA6, PA66, PA12, or glass-filled variants) based on strength needs, temperature resistance, and friction properties. Glass-filled nylon (10–30% glass) enhances rigidity for high-load applications.
- Prototype Development: Create test samples using 3D printing or CNC machining to verify fit, function, and durability. Adjust designs based on prototype testing results.
- Mold Fabrication (for injection molding): Produce steel molds with precise cavity dimensions, incorporating cooling channels to ensure uniform part cooling and reduce warpage.
- Production: For high volumes, use injection molding; for small batches, employ CNC machining. Process parameters (temperature, pressure, cooling time) are optimized for the specific nylon grade.
- Post-Processing: Remove flash (excess material) and deburr gear teeth to prevent premature wear. Some gears undergo annealing to reduce internal stresses and improve dimensional stability.
- Quality Inspection: Measure dimensions using coordinate measuring machines (CMMs), test hardness and tensile strength, and verify tooth profile accuracy. Conduct functional testing under load to ensure performance.
4. Nylon Gear Parts Characteristics
- Self-Lubricating: Nylon’s low coefficient of friction (0.1–0.3) eliminates the need for constant lubrication, ideal for applications where oil contamination is a concern (food processing, medical equipment).
- Lightweight: Approximately 1/7 the weight of steel gears, reducing energy consumption in rotating machinery and easing equipment load.
- Quiet Operation: Nylon’s inherent damping properties absorb vibration and reduce noise by 10–30% compared to metal gears, beneficial for consumer appliances and office equipment.
- Corrosion Resistance: Resists degradation from water, oils, and many chemicals, suitable for wet environments (washdown equipment) or chemical processing plants.
- Impact Resistance: Flexibility allows nylon gears to absorb shocks and overloads without breaking, unlike brittle materials—valuable in machinery with occasional jamming.
- Temperature Tolerance: Standard nylon gears operate reliably between -40°C and 100°C; heat-stabilized grades extend this range to 150°C for industrial applications.
5. Nylon Gear Parts Applications
- Food & Beverage Industry: Corrosion-resistant, lubricant-free nylon gears in conveyors, mixers, and packaging machines, meeting FDA standards (using food-grade PA66).
- Medical Equipment: Quiet, non-magnetic nylon gears in MRI machines, surgical tools, and patient lifts, where metal contamination or noise must be avoided.
- Automotive Sector: Lightweight gears in window regulators, seat adjusters, and windshield wiper systems, reducing vehicle weight and improving fuel efficiency.
- Consumer Appliances: Low-noise gears in blenders, printers, and vacuum cleaners, enhancing user experience with quiet operation.
- Robotics & Automation: Lightweight, corrosion-resistant gears in robotic arms and conveyor systems, where precision and durability in varied environments are critical.
- Marine Applications: Saltwater-resistant nylon gears in small boat winches and fishing equipment, avoiding rust issues associated with metal alternatives.
6. Nylon Gear Parts Performance Additions
- Glass or Carbon Fiber Reinforcement: Adding 10–30% glass fibers increases tensile strength by 50–100% and reduces wear, suitable for high-load applications like industrial conveyors.
- Solid Lubricant Infusion: Incorporating PTFE, molybdenum disulfide, or graphite into nylon reduces friction by 30–40%, extending gear life in high-speed applications.
- UV Stabilization: Adding additives protects gears from sunlight degradation, making them suitable for outdoor equipment like lawnmowers or irrigation systems.
- Chemical Resistance Enhancement: Using specialty nylons (PA12, PPA) improves resistance to oils, fuels, and cleaning agents, ideal for automotive or food processing environments.
- Dimensional Stability Treatments: Annealing processes reduce post-production shrinkage, ensuring gears maintain precise dimensions in temperature-fluctuating environments.
7. Nylon Gear Parts Common Questions
What is the maximum load nylon gears can handle?
Unreinforced nylon gears handle up to 500 N; glass-filled variants (30% glass) manage 1,500–2,000 N. Load capacity decreases at high temperatures (over 80°C) by approximately 20–30%.
How do nylon gears compare to metal gears in service life?
In low-load, clean environments, nylon gears often match or exceed metal gear life (5,000–10,000 operating hours). They wear faster under heavy loads but resist corrosion, making them longer-lasting in wet or chemical environments.
Can nylon gears operate in high-temperature environments?
Standard nylon (PA66) performs reliably up to 100°C; heat-stabilized grades (PA46) work at 150°C. Above 150°C, consider specialty polymers, as nylon may soften and lose strength.
Are custom nylon gears cost-effective?
Yes—molding tooling costs are offset by low material and production costs for high volumes. For small batches, CNC machining avoids tooling expenses. Their long service life and low maintenance needs further enhance cost-effectiveness.
Do nylon gears require lubrication?
Most applications don’t need external lubrication due to nylon’s self-lubricating properties. In high-speed or heavy-load scenarios, occasional light oiling can extend life, but avoid incompatible chemicals (strong solvents).