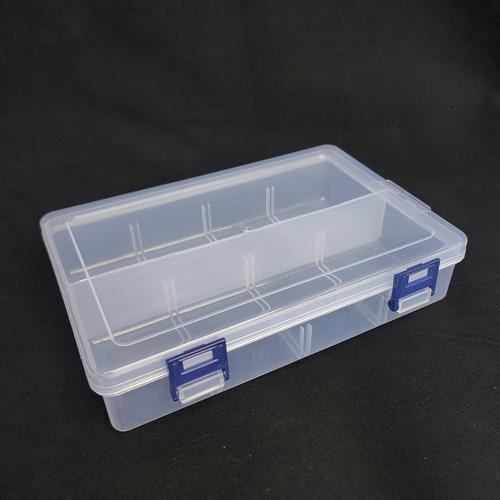
1. Why Custom Transparent Plastic Boxes
2. Transparent Plastic Box Processing Technologies
- Injection Molding: Melts plastic resin and injects it into precision molds under high pressure, producing boxes with consistent thickness, sharp edges, and complex features (hinges, snap closures). Ideal for high-volume production with tight tolerances (±0.1mm).
- Thermoforming: Heats plastic sheets until pliable, then stretches them over molds and cools to shape. Suitable for shallow boxes or trays, offering cost-effective production for medium volumes and large sizes.
- CNC Cutting: Uses computer-controlled routers to cut and shape pre-formed plastic sheets into boxes, ideal for low-volume or prototype production. Enables quick modifications to dimensions or design details.
- Extrusion Blow Molding: Forms hollow boxes by extruding molten plastic into a mold, then inflating it with air. Suitable for cylindrical or irregularly shaped boxes requiring seamless construction.
- 3D Printing: Builds boxes layer-by-layer from transparent filaments (PLA, PETG), perfect for rapid prototyping or complex geometries with internal compartments that are difficult to mold.
3. Transparent Plastic Box Processing Flow
- Design & Specification: Collaborate with clients to define dimensions, capacity, closure type (snap, hinge, lid), and features (compartments, windows). Use CAD software to create 3D models and simulate functionality.
- Material Selection: Choose transparent plastics based on requirements—PET for clarity and strength, PVC for flexibility, acrylic for impact resistance, or PP for chemical resistance.
- Mold Fabrication (for injection molding): Create steel or aluminum molds based on CAD designs, incorporating cooling channels to ensure uniform cooling and prevent warping. Mold complexity depends on box features (e.g., multi-cavity molds for small boxes).
- Production: For high volumes, use injection molding or thermoforming; for prototypes or small batches, employ 3D printing or CNC cutting. Process parameters (temperature, pressure, cooling time) are optimized for the selected material.
- Finishing: Trim excess material, polish edges to remove burrs, and add features like hinges or latches through secondary operations. Apply surface treatments (anti-scratch coating, UV protection) as needed.
- Assembly: For multi-part boxes, assemble components using adhesives, ultrasonic welding, or mechanical fasteners. Ensure closures function smoothly and securely.
- Quality Inspection: Check dimensions with calipers or 3D scanners, verify clarity using light transmission tests, and test functionality (closure strength, impact resistance) to meet specifications.
4. Transparent Plastic Box Materials
- PET (Polyethylene Terephthalate): Offers excellent clarity, high tensile strength, and good chemical resistance. Ideal for food packaging, cosmetic containers, and retail boxes due to its FDA approval and recyclability.
- PVC (Polyvinyl Chloride): Provides flexibility, durability, and low cost. Suitable for boxes requiring slight flexibility (toy packaging, stationery organizers) but with limited recyclability in some regions.
- Acrylic (Polymethyl Methacrylate, PMMA): Boasts superior clarity (92% light transmission) and impact resistance, often called “plexiglass.” Used for high-end display boxes, museum cases, or protective enclosures.
- PP (Polypropylene): Features chemical resistance, heat tolerance (up to 100°C), and good impact strength. Suitable for industrial storage boxes, medical instrument containers, and microwave-safe food packaging.
- PC (Polycarbonate): Offers exceptional impact resistance and heat tolerance, making it ideal for heavy-duty applications (tool storage, protective cases for electronics) despite being less clear than acrylic.
5. Transparent Plastic Box Applications
- Retail & E-Commerce: Display boxes for jewelry, cosmetics, or electronics, showcasing products while protecting them from dust and damage. Custom sizes enhance shelf appeal and brand recognition.
- Food & Beverage: Packaging for confectionery, baked goods, or meal prep, using FDA-approved PET or PP to maintain freshness and visibility. Tamper-evident features ensure food safety.
- Healthcare & Pharmaceuticals: Containers for medical devices, pills, or lab samples, using sterile, chemical-resistant plastics (PP, PC) that meet USP Class VI standards. Transparency allows easy inventory checks.
- Electronics & Industrial: Protective cases for small components, cables, or tools, using impact-resistant PC or acrylic to shield against moisture and physical damage. Custom compartments organize contents efficiently.
- Cosmetics & Personal Care: Boxes for skincare products, perfumes, or makeup kits, combining clarity with branding elements (embossed logos, colored accents) to attract consumers.
- Household & Organization: Storage boxes for craft supplies, office stationery, or small household items, using transparent plastics to easily identify contents without opening.
6. Transparent Plastic Box Performance Additions
- Anti-Scratch Coatings: Apply hard coatings (silicone-based) to reduce surface damage, maintaining clarity even with frequent handling—critical for retail display boxes.
- UV Protection: Add UV inhibitors to prevent yellowing and protect light-sensitive contents (cosmetics, medications) from sunlight degradation, extending product shelf life.
- Tamper-Evident Features: Integrate seals, breakable tabs, or shrink bands to indicate if the box has been opened, ensuring product integrity in food, pharmaceutical, or electronics packaging.
- Custom Closures: Design snap-fit lids, magnetic closures, or sliding mechanisms for easy access while ensuring a secure seal. Hinged designs eliminate separate lids, improving usability.
- Printing & Branding: Use techniques like screen printing, hot stamping, or digital printing to add logos, instructions, or decorative elements without compromising transparency.
- Recyclability Enhancements: Use mono-material construction (avoiding mixed plastics) or add recycling symbols to support sustainability goals and meet consumer environmental expectations.
7. Transparent Plastic Box Common Questions
Which material offers the best clarity?
Acrylic (PMMA) provides the highest clarity (92% light transmission), closely followed by PET (90%). Both offer excellent transparency, but acrylic is more impact-resistant, while PET is more flexible and cost-effective for packaging.
Are custom transparent boxes food-safe?
Yes—when made from FDA-approved materials like PET, PP, or food-grade PVC. These materials resist chemical leaching, making them safe for direct contact with food items. We provide certification documentation for food-contact applications.
How durable are transparent plastic boxes?
Durability depends on material: PC and acrylic boxes withstand heavy impacts, making them suitable for industrial use; PET and PP boxes offer good resistance to everyday handling but may crack under extreme force. All materials resist moisture and most chemicals.
Can custom boxes be recycled?
Many can—PET and PP boxes are widely recyclable in most waste management systems. Acrylic and PC are recyclable but require specialized facilities. We can recommend materials based on your recycling goals and regional capabilities.
What is the minimum order quantity for custom boxes?
Injection molding requires higher minimums (typically 1,000+ units) to offset mold costs, while thermoforming or CNC cutting accommodates smaller batches (100+ units). 3D printing is ideal for prototypes or very small runs (1–50 units).