Friends who drive cars are well aware that factory – original parts sometimes are just “adequate but not perfect” – either they can’t meet the performance requirements of modification, or they lack something in terms of details. At this point, CNC – customized parts have become the favorite choice of many car enthusiasts. However, car parts are much more complex than motorcycle parts. Since they are related to driving safety, more attention needs to be paid when customizing them. Today, let’s talk about the key aspects of customizing automotive CNC parts in detail.
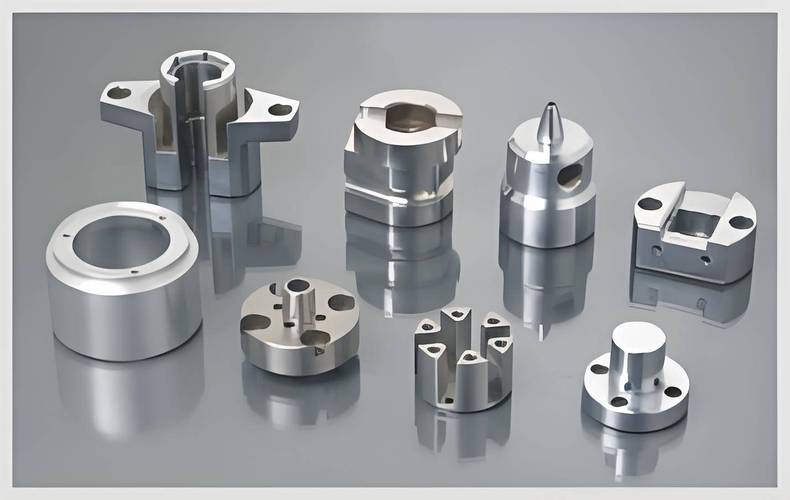
I. Three Advantages of Automotive CNC Customization That Even Seasoned Drivers Can’t Resist
Compared with mass – produced universal parts, CNC – customized parts are like “tailor – made” for cars, especially suitable for car owners who pursue driving experience and personalization:
- High Precision to the Point of “Perfect Fit”: For mating parts in cars, such as transmission gears and bushings, a clearance difference of 0.02 mm can cause gear – shifting jolts. CNC machining can control the tolerance within ±0.003 mm, which is 5 – 8 times more accurate than factory – original parts. After installation, the smoothness of operation is immediately different.
- Strength to Withstand “Aggressive Driving”: Factory – original parts often use stamping or welding processes to control costs. In contrast, CNC customization processes with a whole piece of material. For example, for an aluminum alloy suspension arm, after one – piece forming, the impact – resistance strength is increased by 50%. When taking sharp turns on mountain roads, the roll is significantly reduced.
- Both Personalization and Functionality: If you want to replace your car with a unique steering wheel hub or modify a lightweight intake manifold for a racing car, CNC machining can achieve it. For example, making the brackets in the engine compartment into a hollow shape not only reduces weight but also improves heat dissipation and shows off the mechanical beauty.
II. Choosing the Wrong Material is a Waste of Effort! The “Best Matches” for Different Parts
Automotive parts have clear – cut functions. Some bear weight, some resist high temperatures, and some need to be lightweight. Only by choosing the right material can they play their maximum role. Remember the application scenarios of these commonly used materials:
- Aluminum Alloy (6061/7075): The First Choice for Balancing Performance and Cost
- Suitable Parts: Wheels, suspension control arms, engine mounts, intake manifolds (parts that require lightweight and medium – strength).
- Why Choose It: With a density of only 2.7g/cm³, it is 60% lighter than steel, which can reduce the vehicle’s own weight and improve acceleration and fuel economy. After surface anodizing, its corrosion resistance is sufficient to cope with rain, snow, and road salt.
- Advantages: The yield strength of 7075 aluminum alloy reaches 500MPa, 40% higher than 6061. It is also reliable for load – bearing parts like suspensions, and its price is only 1/3 that of titanium alloy.
- High – strength Steel (4140/4340): The “Guardian” of Hard – core Chassis Parts
- Suitable Parts: Drive shafts, chassis cross – members, brake caliper brackets (parts that bear high torque and impact).
- Why Choose It: Its tensile strength can reach over 1000MPa, twice that of ordinary steel. For example, the drive shaft can withstand a torque of 3000N·m without deformation when rotating at high speed.
- Advantages: After heat treatment, its hardness can reach HRC35 – 45, with strong wear resistance. Moreover, its price is lower than that of titanium alloy, making it suitable for car owners who have high – strength requirements but limited budgets.
- Titanium Alloy (TC4/GR5): The “Ultimate Configuration” for High – end Performance Cars
- Suitable Parts: Exhaust pipes, racing car suspension springs, high – strength bolts (parts that pursue extreme performance and corrosion resistance).
- Why Choose It: Its strength is equivalent to that of steel, but it is 40% lighter. For example, a titanium alloy exhaust pipe is 3kg lighter than a stainless – steel one, which can lower the vehicle’s center of gravity. And it can withstand high temperatures of 800℃ and will not oxidize when in long – term contact with engine exhaust gas.
- Note: Its price is 5 – 8 times that of aluminum alloy. Generally, it is only used for high – end modifications or racing cars. There is no need for ordinary family cars to follow suit.
- Stainless Steel (304/316): The “Practical Choice” for Durability and Corrosion Resistance
- Suitable Parts: Exhaust pipe tail sections, brake lines, chassis guards (parts in contact with water, oil, or high temperatures).
- Why Choose It: 304 stainless steel can resist the corrosion of rainwater and oil. 316 stainless steel is more resistant to acids and alkalis and will not rust when used in coastal areas. Its service life is 3 – 5 times longer than that of ordinary steel.
- Advantages: It has good toughness and is not easy to break after a slight collision. For example, when the chassis guard is hit by a stone, it will at most deform but not crack, providing more reliable protection for the engine.
III. How to Choose Processing Technologies? Match Them According to Part Complexity
Automotive parts come in various shapes, some simple and some complex. Choosing the wrong processing technology not only affects accuracy but also wastes money. Distinguish the application scenarios of these technologies:
- Three – axis Machining: The “Economical Choice” for Simple Parts
- Suitable Parts: Planar brackets, cylindrical shafts, simple covers (parts with regular shapes that do not require multi – angle processing).
- Characteristics: The tool can only move in three directions, with high processing efficiency. For example, for an engine compartment cover, 10 – 15 pieces can be processed in one hour, and the cost is 60% lower than that of five – axis machining.
- Five – axis Machining: The “Exclusive Tool” for Complex and Irregular Parts
- Suitable Parts: Turbocharger impellers, irregular suspension arms, steering wheel skeletons (parts with curved surfaces, inclined holes, or polyhedrons).
- Characteristics: The spindle can rotate at multiple angles. When processing a turbo impeller, the curved surface of the blades and the fillets at the roots can be processed in one clamping without repeatedly adjusting the direction. The accuracy can be controlled within 0.005 mm.
- Disadvantages: The equipment cost is high, and the processing cost is 3 times that of three – axis machining. It is suitable for small – batch and high – precision parts.
- Laser Cutting + CNC Composite Processing: The “Efficient Solution” for Thin – sheet Parts
- Suitable Parts: Body kits, radiator grilles, chassis guards (thin – sheet parts with a thickness of 3 – 10 mm).
- Characteristics: First, use laser to quickly cut out the approximate shape, and then use CNC to refine the edges and holes. For example, when processing a carbon – fiber body kit, the efficiency is 2 times higher than that of pure CNC processing, and material waste can also be reduced.
IV. Want to Ensure Reliable Parts? These 4 Links in the Processing Must Be “Closely Monitored”
Automotive parts are related to safety, and even a small defect can lead to big problems. Regular manufacturers will strictly follow these processes:
- Pre – review of Drawings: Avoid “Inherent Design Flaws”
After receiving the drawings, professional manufacturers will conduct a DFM analysis. For example, if they find a deep hole with a diameter of 8 mm and a depth of 100 mm on the part, they will suggest changing it to a 10 – mm diameter because a depth – to – diameter ratio exceeding 12:1 is likely to break the tool and affect accuracy. If it is a bearing – mating part, they will check whether the tolerance zone matches to prevent it from being too loose or too tight. - Full Inspection during Processing: Prevent Defective Products from Leaving the Production Line
- First – piece Inspection: First, make 2 – 3 parts from the first batch. Use a coordinate measuring machine to detect key dimensions. For example, the roundness of the wheel holes must be controlled within 0.01 mm. Only after passing the inspection will mass production start.
- Sampling Inspection for Each Process: For example, when processing a suspension arm, measure the parallelism after milling the plane and the position accuracy after drilling. If the deviation exceeds 0.015 mm, stop the machine for adjustment to avoid batch waste.
- Final Inspection of Finished Products: After all parts are completed, use a blue – light scanner to generate a 3D model and compare it with the drawing. Parts with excessive errors are directly scrapped and will not be “made do with”.
- Heat Treatment: “Buff” the Parts
- High – strength steel parts need to be quenched and tempered (quenching + high – temperature tempering). For example, after treatment, the hardness of a 4140 steel drive shaft reaches HRC28 – 32, which not only ensures strength but also has toughness and is not too brittle and easy to break.
- Aluminum alloy parts are heat – treated with T6. After solution treatment and artificial aging of 6061 aluminum alloy, the hardness is increased from HB60 to HB95, and the anti – deformation ability is significantly enhanced.
- Surface Treatment: A “Double Insurance” for Appearance and Durability
- For aluminum alloy parts, perform hard anodizing with a film thickness of 15 – 25 microns and a hardness of over HV300. It can resist gravel impacts and can be dyed in personalized colors.
- For steel parts, perform electrophoretic coating. The coating is uniform and has strong adhesion. It can pass a 500 – hour salt – spray test, which is 3 times more corrosion – resistant than ordinary painting. It is not afraid of rusting even when de – icing salt is spread in winter.
- Note: All parts must have burrs removed, especially parts in the engine compartment. Even a 0.5 – mm burr can wear the pipelines and cause malfunctions.
V. Newcomer’s Guide to Avoiding Pitfalls: Don’t Neglect These 3 Points
- Don’t Be Superstitious about “Low Prices”: For aluminum alloy wheels, small factories may process with recycled materials, resulting in poor strength and possible internal pores. Big factories use national standard 6061 – T6 materials and conduct flaw – detection tests for each batch. Although they are 30% more expensive, they are safer.
- Ask for “Material Reports”: Regular manufacturers will provide the mechanical property reports of the materials. For example, the tensile strength of 7075 aluminum alloy must be ≥540MPa to avoid being replaced with 6061. For steel parts, they should provide heat – treatment reports to ensure that the hardness meets the standard.
- “Test – fitting” is Essential: Even if only making 1 part, test – fit it first. For example, for a newly made suspension arm, measure the four – wheel alignment parameters after installation to ensure that the front – wheel toe – in and camber are within the standard range. Only if there are no problems, proceed with mass production.
The core of customizing automotive CNC parts is “safety first, performance second, and personalization third”. By choosing the right materials, technologies, and manufacturers, your car can be both easy to drive and safe. If you cut corners to save money, you may pay a heavy price.
If you have any questions when customizing automotive CNC parts, such as not knowing which material is suitable for your car model or wanting to know the processing cycle, you can leave an online message for consultation. We will help you develop the most suitable plan. Good parts can stand the test, and spending more effort is definitely worth it!