Scratches on CNC parts stem from residual chips, tool wear, contaminated coolants, or improper handling. Solutions include optimizing chip evacuation (high-pressure coolant, filtered systems), using sharp/coated tools, refining handling (lint-free gloves, soft fixtures), and post-processing (polishing, abrasive cleaning). These steps eliminate surface damage, ensuring functional and aesthetic quality across materials.
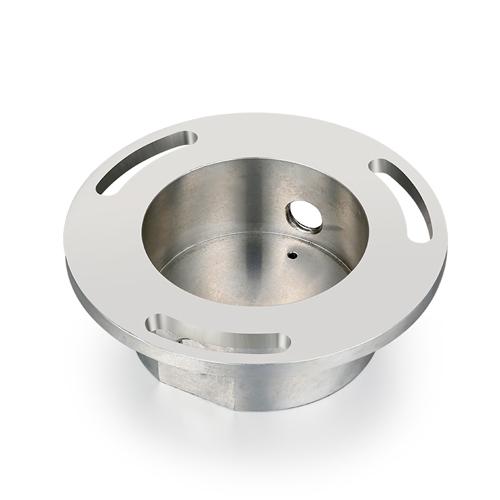
Detailed Analysis of Resolving CNC Machined Surface Scratches
1. Technical Causes & Tooling Solutions
Scratches often originate from tool-chip interactions or equipment issues, requiring targeted technical fixes:
-
Tool Condition & Geometry:
- Sharpness Maintenance: Dull tools drag rather than cut, pushing chips across surfaces and creating scratches. Use carbide tools with edge radii <0.01mm for finishing; replace tools when edge wear exceeds 0.02mm (detected via in-process microscopy). For aluminum, PCD (polycrystalline diamond) tools stay sharp longer, reducing scratch risks by 60% vs. HSS tools.
- Coatings & Surface Treatments: TiAlN or diamond-like carbon (DLC) coatings reduce friction between tool and workpiece. For example, DLC-coated end mills on brass parts lower scratch rates by 40% by minimizing material adhesion to the tool.
- Tool Path Optimization: Avoid abrupt tool retractions that drag chips across surfaces. Use “lift-off” moves (tool raises 0.5mm before traversing) in CAM programs to prevent contact with machined areas—critical for high-gloss parts like automotive trim.
-
Chip Evacuation Technologies:
- High-Pressure Coolant Systems: 70–100 bar coolant flushes chips away from the surface, preventing them from being recut. For deep slots (e.g., 20mm-deep in steel), directional nozzles target the cutting zone, reducing scratch rates by 70% vs. flood cooling alone.
- Chip Breakers & Flute Design: Tools with spiral flutes (30–45° helix) and chip breakers fragment chips into small pieces (5–10mm), avoiding long strings that scratch surfaces. This is vital for ductile materials like copper, where unbroken chips can drag across 10+mm of surface.
2. Process & Coolant System Optimization
Contaminated workflows or inadequate cooling amplify scratch risks, requiring process refinements:
-
Coolant Filtration & Management:
- Fine Filtration: Particulates (e.g., 5–10μm metal fragments) in unfiltered coolant act as abrasives. Use 5μm filters in coolant tanks to remove debris; change filters daily for high-volume production (e.g., automotive brackets). This reduces scratch occurrences by 50% in aluminum machining.
- Coolant Type Matching: Water-soluble coolants (5–10% concentration) for aluminum prevent mineral deposits that scratch surfaces; oil-based coolants for steel reduce chip adhesion. For composites (e.g., CFRP), use low-foam coolants to avoid trapped air bubbles that carry abrasive fibers.
-
Machining Sequence & Feeds/Speeds:
- Finish Last: Schedule finishing passes after all roughing/secondary operations to avoid re-contaminating surfaces with chips from subsequent cuts. For example, machine a mold cavity’s final surface last, then immediately cover it with a protective film.
- Controlled Feeds/Speeds: High feed rates (exceeding 0.3 mm/rev) can eject chips with enough force to scratch nearby surfaces. For thin-walled parts (e.g., 0.8mm stainless steel), use low feeds (0.05–0.1 mm/rev) and high speeds (15,000 RPM) to minimize chip velocity.
3. Material-Specific Scratch Risks & Fixes
Different materials react uniquely to machining forces, requiring tailored approaches:
-
Metals:
- Aluminum/Brass (Soft Metals): Prone to “drag scratches” from chips sticking to tools. Use air blowers to clear chips between passes; after machining, immerse parts in ultrasonic baths (40kHz) with mild detergent to dislodge embedded particles. For mirror-finish aluminum (e.g., smartphone frames), follow with vibratory polishing (ceramic media, 2-hour cycle) to erase micro-scratches.
- Steel/Titanium (Hard Metals): Scratches often come from hard, sharp chips (e.g., broken tool fragments). Use magnetic chip conveyors to remove ferrous debris; for titanium, post-machine with abrasive flow machining (AFM) to smooth scratches in tight areas (e.g., bolt holes) to Ra <0.1μm.
-
Plastics & Composites:
- ABS/PC (Thermoplastics): Softens at high temperatures, making surfaces prone to scratches from tool drag. Use low spindle speeds (3,000–5,000 RPM) and uncoated carbide tools; cool with chilled air (15°C) to prevent material softening.
- Carbon Fiber Reinforced Polymers (CFRP): Frayed fibers act as abrasives. Cut with PCD tools (negative rake angle 5°) to shear fibers cleanly; vacuum chips continuously to avoid fiber accumulation on surfaces. Post-process with 600-grit sandpaper (wet) to remove loose fibers.
4. Handling & Fixturing Improvements
Scratches often occur after machining due to poor handling, requiring workflow adjustments:
-
Fixturing & Storage:
- Soft Contact Surfaces: Line fixtures with rubber or felt pads to prevent metal-to-metal contact. For large parts (e.g., 1m steel plates), use foam supports with cutouts matching the part’s geometry to avoid surface pressure points.
- Controlled Handling: Mandate lint-free gloves (nitrile, not latex) for operators—latex particles can scratch polished surfaces (e.g., brass musical instrument parts). Use vacuum lifters instead of manual lifting for heavy parts to prevent accidental dragging.
-
Post-Machining Transport:
- Segregated Storage: Store finished parts in individual compartments (e.g., foam inserts for electronic connectors) to prevent rubbing. For batch production (e.g., automotive bolts), use coated metal trays with dividers to separate parts.
5. Post-Processing to Remove Existing Scratches
For parts with minor scratches, targeted post-treatments restore surfaces:
-
Mechanical Polishing:
- Use progressively finer abrasives: start with 400-grit sandpaper (wet) for deep scratches, then 800–1200-grit for smoothing, followed by buffing with aluminum oxide compound. This works for stainless steel (e.g., medical instrument trays) to achieve Ra <0.05μm.
- Abrasive Flow Machining (AFM): Forces abrasive-laden polymer through internal/external surfaces (e.g., hydraulic valve bores), erasing scratches in hard-to-reach areas. Effective for parts with complex geometries (e.g., turbine blade cooling channels).
-
Chemical & Electrochemical Treatments:
- Electropolishing: For stainless steel, this process dissolves surface layers (5–10μm) to remove scratches, leaving a passive film that resists future damage. Used in food-grade parts (e.g., dairy processing equipment) to meet hygiene standards.
- Chemical Stripping: For anodized aluminum with surface scratches, strip the anodized layer (using 10% NaOH solution), polish, and re-anodize to restore a uniform finish.
6. Industry-Specific Scratch Prevention
Different sectors have unique scratch risks, demanding tailored protocols:
- Aerospace & Defense: Critical parts (e.g., aircraft wing spars) require scratch-free surfaces to avoid stress concentration. Use 100% in-process inspection with optical scanners (resolution 0.001mm) and cleanrooms for final handling. Coolant systems include UV filters to detect contaminants.
- Medical Devices: Scratches on surgical tools (titanium) trap bacteria. Post-machining, parts undergo ultrasonic cleaning (60°C, 30 minutes) followed by electropolishing. Surfaces are inspected under 50x magnification to ensure Ra <0.02μm.
- Consumer Electronics: Smartphone frames (aluminum) need cosmetic perfection. Finish with diamond turning (20,000 RPM) and automated optical inspection (AOI) to detect 0.01mm scratches, with rejected parts reworked via robotic polishing.
- Automotive Interiors: Plastic trim (ABS) must be scratch-resistant. Molded parts are post-machined with soft abrasive pads (800-grit) and coated with UV-cured clear resin to seal surfaces against future damage.
7. Preventive Measures for Batch Production
To avoid scratches in high-volume manufacturing:
- In-Line Inspection: Integrate vision systems (e.g., Cognex cameras) after machining stations to detect scratches in real time (≥0.05mm depth). Trigger automatic alerts to stop production and adjust processes (e.g., change coolant filter, replace worn tools).
- Standardized Work Instructions: Define tool change intervals (e.g., every 500 parts for brass), coolant replacement schedules (weekly for aluminum), and handling protocols (e.g., “no sliding parts on workbenches”). Train operators to identify early scratch patterns (e.g., linear scratches from chip drag vs. random scratches from contaminants).
- Root Cause Analysis: For recurring scratches, use fishbone diagrams to link causes (e.g., “scratches in slot bottoms” traced to poor chip evacuation) and implement fixes (e.g., add directional nozzles to slot machining stations).
By addressing tooling, processes, material properties, and handling, manufacturers can eliminate surface scratches in CNC machining, ensuring parts meet functional, aesthetic, and industry-specific requirements.