Inspecting CNC part precision involves 5 key steps:
1) Prepare the part (clean and secure it to avoid movement);
2) Select tools (e.g., CMM for dimensional checks, profilometers for surface finish);
3) Measure critical features (dimensions, geometric tolerances like flatness/roundness);
4) Assess surface quality (roughness, defects);
5) Compare data to design specs to verify compliance.
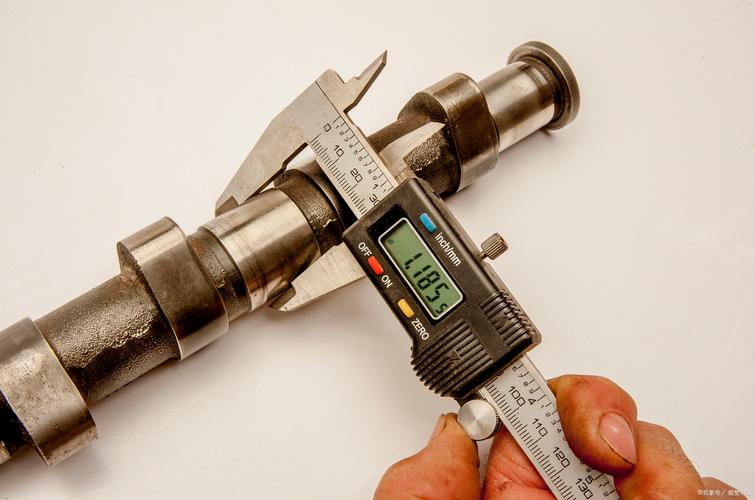
Detailed Analysis of CNC Part Precision Inspection
1. Core Inspection Technologies & Tools
Precision inspection relies on advanced tools tailored to CNC part complexity and tolerance requirements:
-
Coordinate Measuring Machines (CMMs):
These are gold standards for dimensional accuracy, using touch probes or laser scanners to measure 3D coordinates. Bridge-type CMMs (accuracy ±0.0005mm) handle small to medium parts (up to 2m), while gantry CMMs suit large components (e.g., aerospace frames). They verify GD&T (Geometric Dimensioning and Tolerancing) features: flatness (±0.001mm), perpendicularity (±0.002mm/m), and positional tolerances (±0.003mm), critical for mating parts like engine brackets. -
Optical & Laser Systems:
- Optical Comparators: Project 2D part profiles onto a screen, ideal for inspecting small features (e.g., hole diameters <5mm) with ±0.001mm accuracy. Useful for shafts, gears, and threaded components.
- Laser Scanners: Capture millions of data points/second to create 3D models, perfect for complex free-form surfaces (e.g., turbine blades, mold cavities). Scanners with 0.001mm resolution detect deviations in curved profiles, ensuring aerodynamic or aesthetic compliance.
-
Surface Metrology Tools:
- Profilometers: Measure surface roughness (Ra, Rz) via stylus or optical sensors. For example, Ra <0.05μm is required for hydraulic valve spools to prevent leakage, while Ra 1.6μm suffices for non-sealing structural parts.
- Interferometers: Check high-precision surfaces (e.g., optical lenses, mirror finishes) with nanoscale accuracy (±0.0001μm), detecting microscopic waviness.
-
Specialized Gauges:
- Pin Gauges/Ring Gauges: Verify hole diameters or shaft sizes quickly in mass production (e.g., automotive bolt holes, ±0.002mm tolerance).
- Dial Indicators: Measure runout (e.g., shaft concentricity, ±0.001mm) and flatness of large surfaces (e.g., machine beds).
2. Step-by-Step Inspection Process
A structured workflow ensures consistent and accurate results:
-
Part Preparation:
- Cleaning: Remove coolant, oil, or debris with ultrasonic cleaning (for small parts) or lint-free cloths (for large ones). Contaminants can skew measurements (e.g., a 0.005mm dust particle mimics a dimension error).
- Secure Fixturing: Clamp parts gently to avoid deformation—use vacuum chucks for thin-walled aluminum parts (≤1mm thick) or custom jigs for irregular shapes (e.g., turbine blades). Fixtures must repeatably position parts within ±0.002mm.
- Temperature Stabilization: Let parts acclimate to 20±2°C (standard lab temperature) for 2–24 hours (depending on material). Metals like steel expand ~0.012mm/m per °C; a 5°C shift can cause 0.06mm errors in a 1m part.
-
Define Inspection Criteria:
- Extract critical features from CAD models: linear dimensions (length, diameter), geometric tolerances (parallelism, concentricity), and surface finish specs (Ra, Rz). For example, a CNC-machined gear requires checking tooth pitch (±0.003mm), profile (±0.002mm), and face runout (±0.001mm).
-
Select & Calibrate Tools:
- Choose tools based on tolerance: CMMs for ±0.001mm, optical scanners for complex 3D shapes, and gauges for ±0.01mm.
- Calibrate tools daily using certified standards (e.g., a 100mm master block with ±0.0001mm accuracy) to ensure measurements are traceable to international standards (ISO 10360).
-
Execute Measurements:
- Dimensional Checks: For linear dimensions (e.g., hole depth), use CMM touch probes (accuracy ±0.0005mm). For geometric tolerances (e.g., flatness of a mold plate), scan the surface with a laser to collect 10,000+ data points, then analyze deviations from the ideal plane.
- Surface Inspection: Run a profilometer stylus across critical areas (e.g., a bearing seat) to record Ra—reject parts with Ra >0.8μm if specs require <0.4μm.
- Complex Features: For 3D contours (e.g., aerospace engine impellers), use 5-axis laser scanners to capture every curve, comparing to CAD with software like Geomagic Control X to highlight ±0.002mm deviations.
-
Data Analysis & Reporting:
- Compare measurements to drawing tolerances. Flag out-of-spec features (e.g., a hole diameter 0.003mm over limit).
- Generate reports with pass/fail status, trend charts (e.g., tool wear causing increasing diameter errors), and 3D visualizations of deviations for process improvement.
3. Impact of Material Properties
Material characteristics influence inspection methods and accuracy:
-
Metals (Steel, Aluminum, Titanium):
- High thermal conductivity requires strict temperature control (±1°C) to avoid expansion/contraction errors.
- Hardness (e.g., 50HRC steel) allows precise stylus probing without surface damage, unlike soft metals (e.g., annealed aluminum, 20HRC) which need lighter probe forces (≤0.1N) to prevent indentation.
-
Plastics (ABS, PC, PEEK):
- Low rigidity means fixturing must minimize clamping force—over-tightening can distort dimensions by 0.01–0.05mm.
- Hygroscopic plastics (e.g., PA6) absorb moisture, swelling 0.1–0.3%—inspect after 24-hour drying to ensure accuracy.
-
Composites (Carbon Fiber, Glass Fiber):
- Anisotropic properties (different expansion in fiber vs. resin directions) require multi-directional measurements.
- Rough cut edges may scatter laser light, so use touch probes for critical dimensions instead of optical scanners.
4. Part-Specific Inspection Focus
CNC part designs dictate unique inspection priorities:
-
Precision Gears & Sprockets:
- Key checks: tooth pitch (±0.002mm), cumulative pitch error (≤0.005mm/10 teeth), and backlash (±0.001mm). Use gear testers with rotary encoders for high accuracy.
-
Mold Cavities & Cores:
- Inspect surface finish (Ra <0.1μm for glossy 塑件) and profile accuracy (±0.003mm) to ensure molded parts match CAD. 3D scanners compare cavity geometry to the original part design.
-
Aerospace Structural Parts:
- Large components (e.g., wing ribs) require portable CMMs or laser trackers (accuracy ±0.005mm at 10m) to check hole positions (±0.01mm) and flange flatness (≤0.005mm/m).
-
Electronic Connectors:
- Tiny features (pin diameter 0.3mm, pitch 0.5mm) need optical comparators or micro-CMMs (accuracy ±0.0005mm) to verify pin straightness and spacing.
5. Industry-Specific Standards & Scenarios
Different sectors demand tailored precision inspection:
-
Aerospace & Defense:
- Tolerances as tight as ±0.001mm for engine components (e.g., fuel injectors). Use CMMs with environmental controls (temperature, humidity) and traceable to NIST standards. Critical features undergo 100% inspection.
-
Automotive:
- Mass-produced parts (e.g., brake calipers) use automated gauging stations (cycle time <10 seconds) to check key dimensions (bore diameter ±0.01mm). Sampling (1 in 50 parts) with CMMs validates process stability.
-
Medical Devices:
- Surgical instruments (e.g., scalpel handles) require Ra <0.02μm to prevent bacterial adhesion. Inspect surface finish with white light interferometers, and verify hole concentricity (±0.002mm) for fluid flow.
-
Electronics:
- PCB housings need tight dimensional control (±0.05mm) for component fit. Use vision systems with 0.001mm/pixel resolution to inspect hundreds of features in seconds.
6. Common Challenges & Solutions
- Thermal Variability: Mitigate with climate-controlled labs (20±1°C, 50±5% humidity) and thermal compensation software in CMMs.
- Complex Geometries: Use 5-axis scanners for undercuts or deep cavities; for internal features (e.g., threaded holes), deploy articulating probes.
- Surface Reflectivity: Shiny metals (e.g., polished stainless steel) can scatter laser light—use matte sprays (temporary, 0.001mm thick) to improve scan accuracy.
- High-Volume Inspection: Automate with robotic loaders for CMMs or inline vision systems to balance speed and precision.
In summary, inspecting CNC part precision combines advanced tools, rigorous processes, and material/industry-specific strategies. By aligning measurement methods with part requirements, manufacturers ensure compliance with design specs and performance reliability.