Sandblasting CNC parts is a process that propels abrasive materials at high speed onto the part surface using compressed air. It removes oxide layers, oil, burrs, or creates a uniform roughness via abrasive impact. This technique cleans surfaces, enhances coating adhesion, or achieves decorative effects like matte finishes. Suitable for CNC parts made of metals, plastics, etc., it requires selecting abrasives and parameters based on material and application needs.
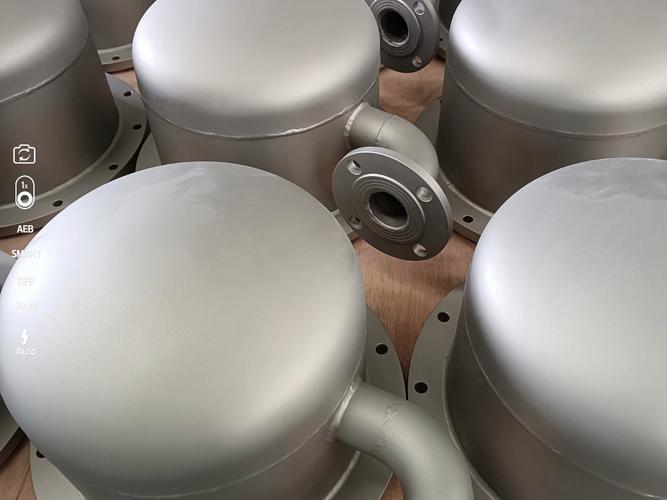
Detailed Analysis of Sandblasting CNC Parts
1. Core Technologies and Equipment
Sandblasting relies on abrasive acceleration and surface interaction, with key equipment and parameters as follows:
-
Types of Sandblasting Equipment:
- Suction Sandblasters: Use compressed air negative pressure to draw abrasives, ideal for small-batch, precision work (e.g., removing oxide from fine parts) with low pressure (0.2–0.5MPa) for easy flow control.
- Pressure Sandblasters: Mix abrasives with compressed air in a pressure tank before spraying, operating at higher pressures (0.4–0.8MPa) for high-efficiency, mass processing (e.g., cleaning automotive parts).
- Wet Sandblasters: Spray abrasives mixed with water, reducing dust and ensuring smoother surfaces. Suitable for heat-sensitive materials (e.g., aluminum alloys) or dust-free environments (e.g., medical parts).
-
Abrasive Selection:
- Metal Parts: Aluminum oxide (brown/white corundum, 80–120 mesh) removes oxides and strengthens surfaces; glass beads (100–200 mesh) polish or deburr without damaging substrates; steel grit/shot (high hardness) strengthens high-strength steel parts (e.g., gears) to boost surface hardness.
- Plastics/Composites: Nylon grit (elastic) avoids scratching, suitable for ABS/PC parts; walnut shell/corn cob abrasives (biodegradable) clean precision plastic components (e.g., electronic enclosures).
-
Key Parameters:
- Pressure: 0.3–0.6MPa for metals; 0.1–0.3MPa for plastics/soft metals (e.g., aluminum) to prevent over-erosion.
- Distance/Angle: Nozzle-to-part distance of 10–20cm; 90° vertical spraying for maximum efficiency, 45° tilt to reduce blind spots.
- Time: 30–60 seconds for oxide removal, 10–20 seconds for matte finishing.
2. Sandblasting Process
A standardized process ensures uniform results without damaging parts:
-
Pre-Treatment:
- Cleaning: Remove oil/cutting fluid with alcohol or alkaline cleaners (oil causes uneven abrasive adhesion).
- Masking: Cover non-blast areas (e.g., threads, sealing surfaces) with silicone plugs, tape, or dedicated films to avoid accidental treatment.
- Inspection: Check for cracks or thin walls (<1mm); reduce pressure to <0.2MPa for thin parts to prevent deformation.
-
Sandblasting Operation:
- Equipment Setup: Adjust pressure based on abrasives (e.g., 0.5MPa for aluminum oxide, 0.3MPa for glass beads); test on scrap material first.
- Uniform Spraying: Move the nozzle at 10–15cm/s; extend time for complex structures (e.g., deep grooves) to eliminate blind spots.
- Mass Processing: Automated sandblasters (e.g., rotary table systems) use programmed paths for standardized parts (e.g., phone mid-frames), achieving 500–1000 units/hour.
-
Post-Treatment:
- Cleaning: Blow off residual abrasives with compressed air or rinse (for wet blasting); use ultrasonic cleaning for deep holes if needed.
- Drying: Air-dry or bake at 50–80°C to prevent rust on metal parts.
- Inspection: Check surface roughness (Ra value) with a profilometer (e.g., Ra1.6–3.2μm for pre-coating); verify no residual impurities or over-erosion.
3. Material Compatibility
Different materials require specific abrasives and parameters to avoid damage:
-
Metals:
- Steel/stainless steel: Aluminum oxide (80 mesh) at 0.4–0.6MPa removes oxides and prepares for coating.
- Aluminum alloys: Glass beads (120 mesh) at 0.2–0.4MPa to avoid darkening from over-erosion.
- Copper/brass: Nylon grit or fine glass beads (200 mesh) at <0.2MPa to prevent oxidation discoloration.
-
Non-Metals:
- Plastics (ABS, PC): Nylon grit (100 mesh) at 0.1–0.2MPa for matte finishes without scratches.
- Composites (carbon/glass fiber): Corn cob abrasives at <0.15MPa to avoid fiber exposure or matrix damage.
4. Suitable CNC Parts and Effects
Sandblasting achieves diverse surface functions for various parts:
-
Pre-Treatment:
- Coating/plating substrates (e.g., automotive bracket, machine housings): Remove oxides/oil to improve adhesion (90% reduction in coating peeling).
- Pre-welding parts (e.g., pipe flanges): Eliminate rust/impurities to ensure weld quality.
-
Surface Strengthening:
- Moving components (e.g., gears, bearing seats): Steel shot blasting induces compressive stress, extending fatigue life by 30–50%.
- Mold cavities: Fine aluminum oxide blasting creates uniform roughness for easier demolding and texture.
-
Decoration:
- Consumer electronics (e.g., laptop casings, watch cases): Glass bead blasting for fine matte finishes (Ra0.8–1.6μm) to enhance 质感.
- Signs/decorative parts (e.g., metal nameplates): Sandblast then etch for contrasting patterns.
5. Industry Applications
Sandblasting serves sector-specific needs for CNC parts:
- Automotive: Engine blocks (aluminum) blasted to remove casting oxides before painting; chassis parts (steel) strengthened with steel grit to resist gravel impacts.
- Aerospace: Landing gear (high-strength steel) blasted to remove machining marks and induce stress; cabin trim (aluminum) glass bead-blasted for aesthetics and lightness.
- Mold Making: Injection mold cavities blasted (Ra1.6μm) to texture (e.g., phone case); stamping die edges blasted to reduce material sticking.
- Electronics: 5G radiator (aluminum) blasted to enhance heat sink adhesion; semiconductor equipment parts (stainless steel) wet-blasted to avoid dust contamination.
- Medical Devices: Surgical tools (stainless steel) blasted to remove fingerprints for sterilization; prosthetic joints (titanium) blasted for bone-integration-friendly roughness.
6. Challenges and Solutions
Address these issues to ensure quality:
- Uneven Surfaces: Caused by inconsistent nozzle movement or abrasive clumping. Use automated path control and sieve abrasives regularly.
- Over-Erosion/Deformation: Thin aluminum parts (e.g., phone frames) may dent at high pressure. Reduce pressure to 0.15MPa and shorten blasting time.
- Residual Abrasives: Trapped in holes/threads, affecting assembly. Reverse-blow with compressed air and use ultrasonic cleaning.
- Rusting: Steel parts rust if post-treated late. Apply anti-rust oil/primer within 2 hours; use wet blasting with rust inhibitors in humid environments.
In summary, sandblasting CNC parts requires matching abrasives and parameters to materials/needs. A standardized process ensures clean, strengthened, or decorative surfaces, critical for precision manufacturing performance and aesthetics.