This article takes the technical exploration in the field of auto parts manufacturing as the main line, analyzing how CNC processing technology breaks through industry bottlenecks through interdisciplinary integration and iterative innovation. By disassembling core scenarios such as power system optimization, lightweight material application, and digital twin verification, it reveals the key role of the technical exploration methodology in practice and demonstrates three paradigm shift paths for future technical exploration.
Recommended Reading
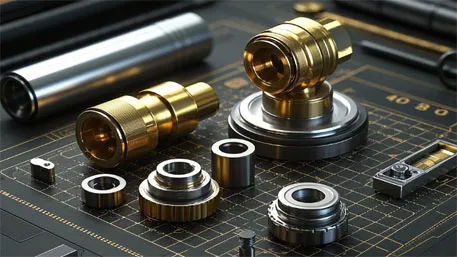
CNC Prototype Manufacturing: Xiamen Goldcattle’s Full-link Empowerment
— Centered on Precision Machining Technology, Creating an “Acceleration Engine” for Product Innovation I. Technical Advantages: Why Do Global TOP 500 Enterprises Choose CNC Prototypes? ±0.005mm Precision Standard, Breaking Through…
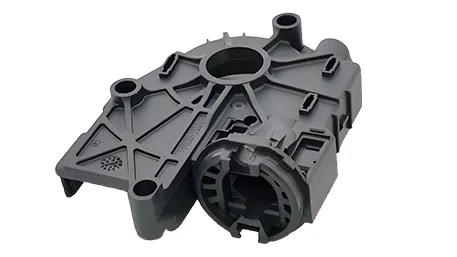
Xiamen Goldcattle Precision Plastic Injection Molding Parts Customer Case
1.Background Xiamen Goldcattle Industrial & Trade Co., Limited, founded in 2011, is a company with rich experience and professional technology in the field of precision plastic injection molded parts. With its…
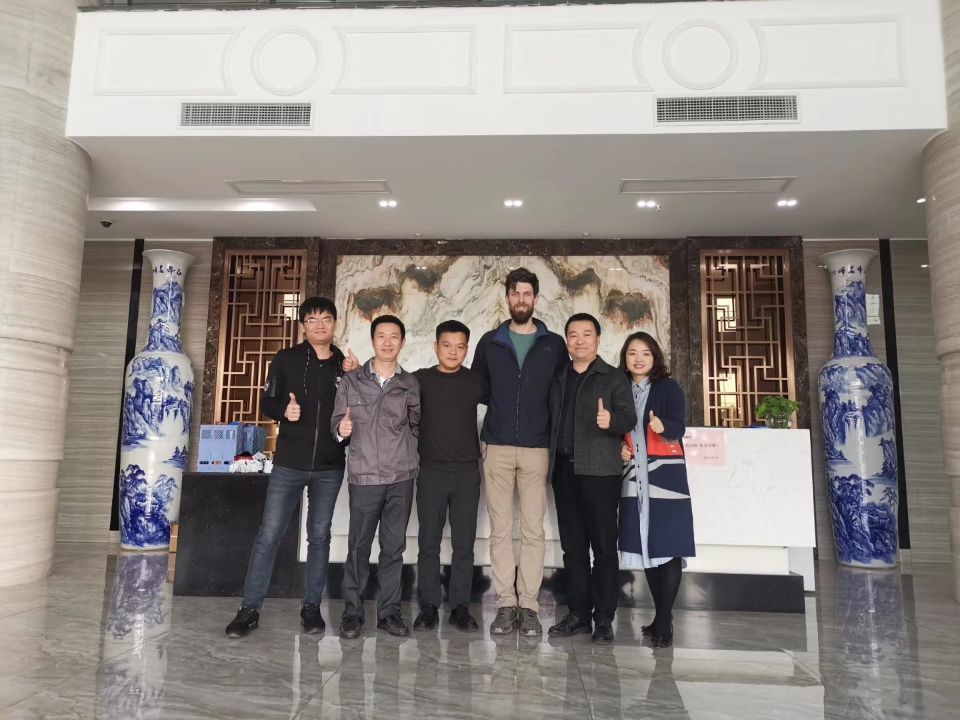
Group photo of American customers visiting our factory
On August 27, the customer came to the company for a site visit. The high quality products and services, strong company qualification and reputation, and good industry development prospect are…
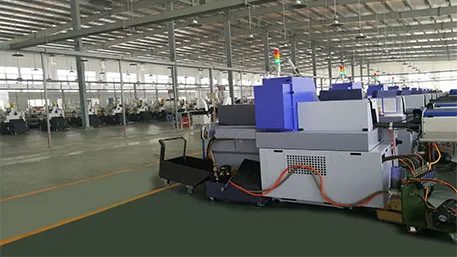
Xiamen Goldcattle: A Premier CNC Machining Parts Manufacturer in China
In the vast landscape of China’s manufacturing industry, Xiamen Goldcattle shines as a leading CNC machining parts manufacturer. With a proven track record of excellence and a commitment to quality, Xiamen…
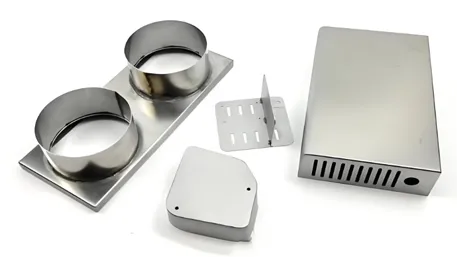
Technological Innovation Empowers Sheet Metal Customization: Xiamen Goldcattle Sets a New Benchmark for Intelligent Manu
In the wave of the upgrade of China’s sheet metal industry, Xiamen Goldcattle, with its innovative service model of the “Technical Expert Assistance Program for Enterprises”, has set a new…
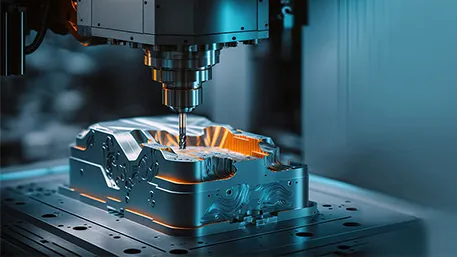
Industrial CNC Parts Service
Welcome to the world of CNC parts for industry. With the rapid development of manufacturing industry, CNC parts play an increasingly important role in the industrial field. As a professional CNC parts…