- Answer
Five common types of CNC machine tools include:
CNC milling machine: Milling planes, grooves, or complex curved surfaces through a rotating cutting tool.
CNC lathe: Clamping the workpiece for rotation and using a turning tool to cut cylindrical parts.
CNC machining center: Integrating multiple functions such as milling, drilling, and boring, with an automatic tool – changing device.
CNC grinding machine: Using a grinding wheel to grind the workpiece surface to achieve high – precision smoothness.
CNC laser cutting machine: Utilizing a laser beam to melt or vaporize materials, cutting thin plates or metal pipes. - Explanation
The CNC machine tool family is like a “combination of hardware stores in the industrial world”:
CNC milling machine: It’s like a “carving knife that can turn corners”, capable of “drawing” various planes or curved surfaces on materials (such as milling the tooth surface of a gear).
CNC lathe: Similar to a “rotating pencil sharpener”, it clamps a cylindrical material (such as an aluminum rod), rotates it while cutting, and produces pen – shaped parts.
Machining center: It’s like an “all – around Swiss Army knife”. It can both mill and drill, and can automatically change tools, completing complex parts in one go.
CNC grinding machine: Just like a “precision polisher”, it uses a grinding wheel to make the part surface as smooth as a mirror (such as parts of medical devices).
Laser cutting machine: It’s like a “lightsaber cutter”, quickly “cutting” out complex shapes of metal sheets with a laser beam (such as hollow decorative parts). - Problem Expansion
Core Functions and Application Scenarios of Various Machine Tools
CNC milling machine (3 – axis / 5 – axis)
Features: A 3 – axis milling machine can process planes and simple curved surfaces, while a 5 – axis milling machine can rotate the cutting tool at multiple angles to handle complex structures such as impellers and aero – engine blades.
Applications: Machining the cavity of automotive molds, milling the aluminum – alloy frame of unmanned aerial vehicles.
CNC lathe
Features: The main motion is the rotation of the workpiece. It is suitable for processing axis – symmetric parts (such as shafts and discs), with an accuracy up to IT6 level (±0.01mm).
Applications: Producing motor shafts, bicycle frame tubes, and the valve cores of bathroom faucets.
CNC machining center
Core advantages: Multiple processes (milling, drilling, tapping) can be completed in one clamping, reducing the error of manual tool – changing. For example, when machining a transmission housing, it can continuously complete milling the plane → drilling → boring → chamfering, with an efficiency 3 times higher than that of traditional machine tools.
Typical scenarios: Mass – producing mobile phone mid – frames (requiring integrated milling of curved surfaces + drilling + polishing).
CNC grinding machine (surface grinding / cylindrical grinding)
Accuracy level: The surface roughness can reach Ra 0.1μm (mirror level), used for the final processing of precision parts (such as gauge blocks and guide rails).
Medical applications: Grinding the surface of artificial joints to ensure fit and wear resistance (error < 0.005mm).
CNC laser cutting machine
Technological breakthroughs: Fiber – optic laser cutting machines can cut 20mm – thick steel plates, with a speed 5 times that of traditional tools and minimal thermal deformation.
Creative scenarios: Cutting hollow patterns in sheet metal processing (such as elevator panel decorations), and cutting lithium – battery electrode sheets in the new energy field.
Recommended Reading
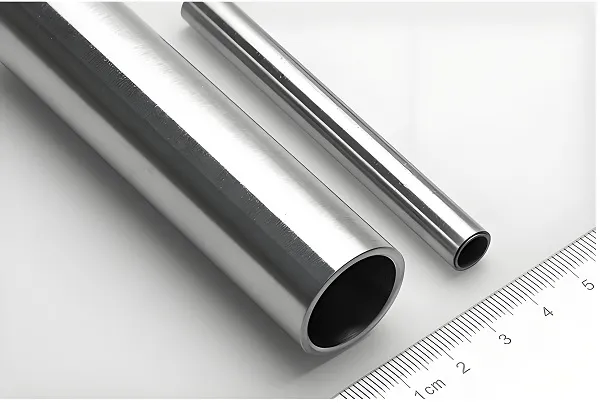
Stamped Tube CNC Processing Introduction
The purpose of this article is to provide a comprehensive introduction to the production process of stamped tubes, including types of equipment, corresponding production product types, application scope, product characteristics…
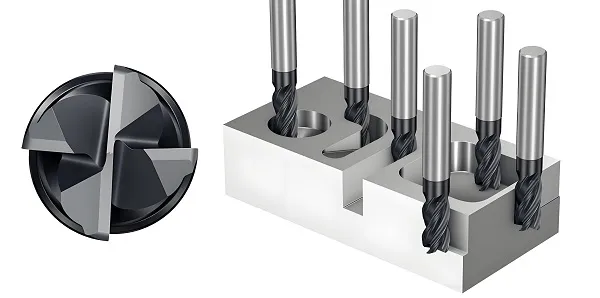
Customized End Milling Tools
End milling tooling is one of the indispensable tools in metal cutting processing, widely used in aerospace, mold making, automobile manufacturing and many other fields. It realizes multi-angle and high-precision…
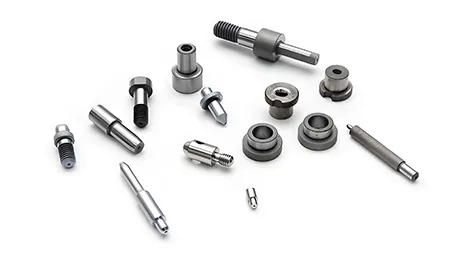
Customized Medical CNC Parts Service
Medical CNC parts are precision components that are machined by computer numerical control (CNC) technology and are used in medical equipment, instruments and implants. With the continuous progress of medical technology, CNC…
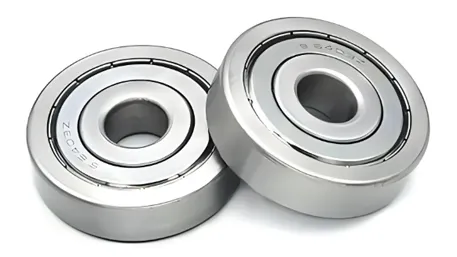
In-depth Research on the Essentials of CNC Bearing Machining
Abstract: This article deeply discusses the key essentials of bearing machining under Computer Numerical Control (CNC) technology. Through detailed analysis of process flow, tool selection, cutting parameter optimization, precision control,…

Beyond Precision: 7 Overlooked Dimensions of CNC Machining Parts
1. Material Anisotropy & Toolpath Psychology CNC machining navigates material “personality” through adaptive algorithms. For aluminum alloys (e.g., 6061-T6), grain directionality causes 12-18% variance in surface roughness when cutting parallel vs. perpendicular…
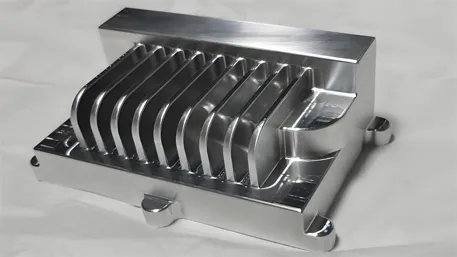
Custom CNC Stainless Steel Parts: Precision Paragon Shaped by Technology
In the high – end realm of modern manufacturing, custom CNC stainless – steel parts, with their outstanding performance and precise craftsmanship, have become the core support for numerous key…