Powder coating for CNC parts is a dry finishing process where electrostatically charged powder (a mixture of resins, pigments, and additives) is sprayed onto the part surface, then cured under heat to form a durable, protective layer. It offers superior adhesion, corrosion resistance, and color retention compared to liquid paints, making it ideal for functional and decorative CNC-machined components.
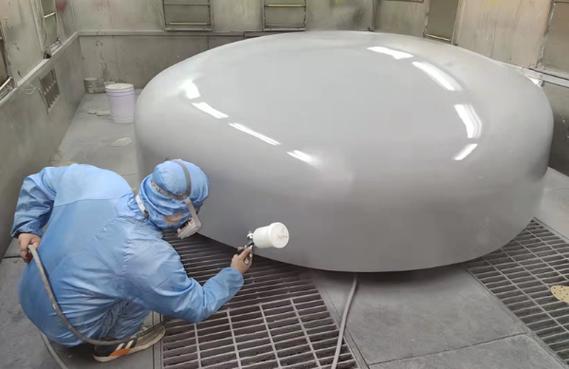
Detailed Analysis of Powder Coating for CNC Parts
1. Core Technologies
Powder coating relies on electrostatic principles and thermal curing to bond the coating to CNC parts:
- Electrostatic Application: The powder is charged (typically negatively) using a spray gun, while the CNC part is grounded (positively). This electrostatic attraction ensures uniform powder adhesion, even on complex geometries like deep grooves or sharp edges. Manual guns are used for small batches, while automated systems with robotic arms handle mass production, achieving ±5μm thickness consistency.
- Curing Mechanisms: Thermosetting powders (the most common type) melt and cross-link at 160–200°C, forming a hard, infusible film. Thermoplastic powders (used for flexible coatings) melt at lower temperatures (120–150°C) without cross-linking, allowing for re-melting if needed. Infrared or convection ovens are used for curing, with cycle times ranging from 10–30 minutes depending on part thickness.
- Thickness Control: Coating thickness (typically 50–150μm) is regulated by powder feed rate, gun voltage (60–100kV), and spray distance (15–30cm). Thicker coatings (200–300μm) provide enhanced impact resistance for heavy-duty parts, while thinner layers (30–50μm) are used for precision components like electronic enclosures.
2. Manufacturing Process
The powder coating workflow for CNC parts involves several critical steps:
-
Surface Preparation:
- Cleaning: Remove oils, cutting fluids, and contaminants using alkaline cleaners or solvent degreasing. For metal parts, acid etching or sandblasting creates a rough surface (Ra1.6–3.2μm) to improve powder adhesion—critical for corrosion resistance.
- Pre-Treatment: Metal CNC parts often undergo phosphate conversion coating or chromate treatment to further enhance corrosion resistance, especially in automotive or marine applications. Plastic CNC parts may require flame treatment to increase surface energy for better powder adhesion.
-
Powder Application:
- Electrostatic Spraying: The charged powder is sprayed onto the grounded CNC part, adhering to all surfaces via electrostatic attraction. For large parts (e.g., machine frames), multiple guns are positioned to ensure coverage. For intricate parts (e.g., gear teeth), a “fluidized bed” method (dunking the part in aerated powder) may be used for uniform coating.
- Recovering Overspray: Unused powder is collected via cyclones or filters and reused (up to 95% efficiency), reducing waste compared to liquid paints (which have 30–40% waste).
-
Curing:
- The part is baked in an oven at 160–200°C, causing the powder to melt, flow, and cross-link. For thick-walled CNC parts (e.g., steel brackets), pre-heating the part to 80–100°C accelerates curing and prevents pinholes.
- Cooling occurs naturally or via forced air, with the coating reaching full hardness within 24 hours.
3. Powder Materials and Formulations
Powder coatings are tailored to CNC part materials and performance needs:
-
Resin Types:
- Epoxy: Offers excellent corrosion resistance and adhesion, ideal for indoor CNC parts like electrical enclosures. Limited UV resistance makes it unsuitable for outdoor use.
- Polyester: Balances UV resistance, flexibility, and durability, used for outdoor parts (e.g., automotive trim, patio furniture).
- Hybrid (Epoxy-Polyester): Combines epoxy’s corrosion resistance with polyester’s weatherability, suitable for marine or industrial CNC parts.
- Fluoropolymer: Provides extreme chemical and heat resistance (up to 260°C), used in aerospace CNC components or chemical processing equipment.
-
Additives:
- Pigments for color (e.g., titanium dioxide for white, carbon black for black) and special effects (metallic, textured).
- Flow agents to ensure smooth finishes, anti-crater additives to prevent surface defects, and UV stabilizers for outdoor parts.
4. Suitable CNC Parts and Applications
Powder coating enhances performance across diverse CNC components:
- Automotive: Chassis parts (steel brackets), wheel rims, and interior trim (aluminum) benefit from corrosion resistance and scratch protection.
- Aerospace: Lightweight aluminum CNC parts (e.g., aircraft seat frames, control panels) use high-temperature powders to withstand cabin conditions.
- Industrial Machinery: Gearboxes, hydraulic manifolds, and tooling fixtures (steel) gain abrasion resistance and chemical protection.
- Consumer Goods: Exercise equipment (steel), outdoor furniture (aluminum), and electronic device casings (magnesium alloys) use powder coating for durability and aesthetics.
- Medical Devices: Stainless steel CNC parts (e.g., surgical instrument trays) use antimicrobial powders to meet hygiene standards.
5. Key Advantages and Industry Benefits
Powder coating offers unique advantages for CNC parts compared to liquid paints:
- Durability: The cured coating resists chipping, peeling, and impact—ideal for high-wear CNC parts like automotive pedals or industrial handles.
- Eco-Friendliness: No volatile organic compounds (VOCs) are released, reducing environmental impact and meeting strict regulations (e.g., EU REACH, US EPA standards).
- Cost Efficiency: High powder reuse rates (85–95%) lower material costs, while faster curing reduces production time compared to liquid paint drying.
- Versatility: Supports a wide range of colors, textures (matte, glossy, textured), and thicknesses, enabling custom finishes for branding or functional needs (e.g., anti-slip coatings for tool grips).
6. Challenges and Quality Control
- Complex Geometries: Deep recesses or blind holes in CNC parts may trap air, causing thin or uneven coatings. Solutions include adjusting gun angle, using lower powder velocity, or pre-heating the part to improve flow.
- Contamination Risks: Oil residues or surface oxides on CNC parts cause coating defects (craters, adhesion failure). Rigorous pre-cleaning (ultrasonic washing for precision parts) and quality checks (adhesion testing via cross-hatch tape tests) mitigate this.
- Temperature Sensitivity: Plastic or heat-sensitive CNC parts (e.g., composite brackets) require low-temperature curing powders (120–140°C) to avoid deformation.
- Thickness Uniformity: Automated systems with laser thickness sensors ensure consistency, critical for CNC parts with tight tolerances (e.g., 0.1mm clearance fits).
In summary, powder coating is a versatile, durable finishing process for CNC parts, combining electrostatic precision with thermal curing to deliver protective, high-performance coatings across industries—from automotive to aerospace.