Injection molding and plastic casting are both methods to shape plastic, but they differ fundamentally in how material is introduced into the mold and the types of plastics they use.
- Injection molding forces molten thermoplastic resin into a closed mold under high pressure, then cools and solidifies the plastic.
- Plastic casting pours liquid resin (often thermosetting plastics) into an open or closed mold, where it cures (hardens) through chemical reaction or heat—no high pressure is involved.
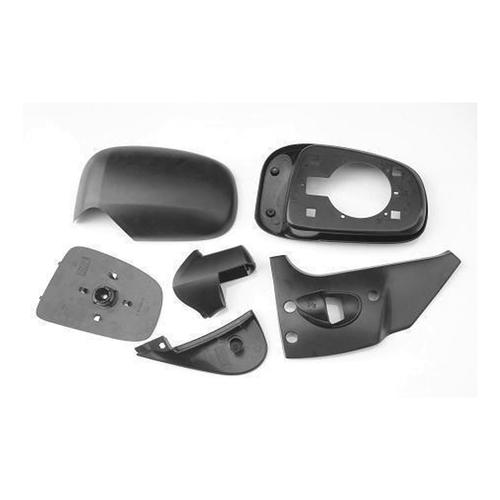
How do their processes differ step-by-step?
Injection molding process:
- Melting: Thermoplastic pellets (e.g., PP, ABS) are heated to a molten state (150–300°C) in a barrel.
- Injection: The molten plastic is injected into a closed, precision-machined steel or aluminum mold under high pressure (100–2000 bar).
- Cooling: The mold is cooled (via water channels) to solidify the plastic quickly (seconds to minutes).
- Ejection: The mold opens, and the solid part is ejected.
Plastic casting process:
- Mixing: Liquid resin (e.g., epoxy, polyurethane) is mixed with a hardener (for thermosets) to start a chemical reaction.
- Pouring: The liquid mixture is poured or injected (at low pressure) into an open or closed mold (often made of silicone, aluminum, or even wood for simple parts).
- Curing: The resin hardens over time (minutes to hours) through chemical cross-linking, sometimes accelerated by heat.
- Demolding: The cured part is removed from the mold—no cooling is needed, as curing generates its own heat.
What materials do they use?
- Injection molding: Exclusively uses thermoplastics (plastics that melt when heated and solidify when cooled), such as ABS, polypropylene (PP), polyethylene (PE), or nylon. These can be melted and reshaped repeatedly.
- Plastic casting: Primarily uses thermosetting plastics (resins that cure into a permanent solid), like epoxy, polyurethane, or polyester. Once cured, they cannot be remelted—applying heat would burn them. Some casting processes use thermoplastics (e.g., acrylic casting), but this is less common.
How do they compare in cost?
- Injection molding: Higher upfront costs ((1,000–)100,000+ for molds) due to precision steel/aluminum tooling, but low per-part costs at scale (cents to dollars per part) because of fast cycle times (seconds per part).
- Plastic casting: Lower upfront costs ((100–)5,000 for molds, often made of silicone or low-cost metals) but higher per-part costs (dollars to tens of dollars per part) due to slower curing times and manual labor (e.g., mixing resin, pouring).
Which is better for part complexity and precision?
- Injection molding: Excels at complex, high-precision parts with tight tolerances (±0.001 inches). It can produce intricate details (e.g., thin walls, threads, undercuts) thanks to high-pressure filling, which ensures the plastic flows into every mold cavity detail.
- Plastic casting: Works for moderately complex shapes but struggles with very thin walls or tight tolerances (typically ±0.01 inches). Low pressure means liquid resin may not fill tiny details, and curing shrinkage can cause dimensional variations.
What about production volume?
- Injection molding: Ideal for high-volume production (10,000+ parts). Fast cycle times and automated equipment make it efficient for mass manufacturing (e.g., plastic bottles, automotive parts).
- Plastic casting: Better for low-volume production (1–1,000 parts) or prototypes. Slow curing and manual steps make it impractical for large batches, but its low mold cost suits small runs (e.g., custom figurines, artisanal parts).
Which is more versatile?
- Injection molding: Limited to thermoplastics but handles a wide range (rigid, flexible, heat-resistant). It’s used across industries from consumer goods to aerospace.
- Plastic casting: Specializes in thermosets, which offer unique properties like high heat resistance, chemical resistance, or flexibility (e.g., soft polyurethane for gaskets). It’s common in crafts, prototyping, and specialty parts (e.g., epoxy tooling).
Conclusion
Choose injection molding for high-volume, precise, complex thermoplastic parts. Choose plastic casting for low-volume, custom, or thermoset parts where upfront cost and simplicity matter more than speed. The core difference lies in pressure, materials, and scalability—each method solves distinct manufacturing needs.