In the field of modern industrial manufacturing, plastics have become key materials in industries such as electronics, automotive, medical, and aerospace due to their characteristics of lightweight, corrosion resistance, good insulation, and low cost. With the development of industrial demands towards personalization and precision, CNC (Computer Numerical Control) technology, with its diverse processing techniques and high – precision control capabilities, has become the core technical support for customizing plastic parts. This article will systematically expound on the technical logic and engineering value of custom CNC plastic parts from dimensions such as processing technology analysis, materials engineering, quality control, and industry applications.
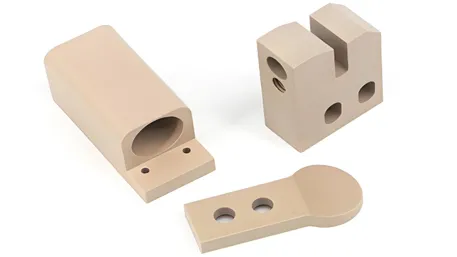
CNC technology achieves high – precision customization of plastic parts through diverse processing technologies. The following are the core technologies and data indicators:
- Process Characteristics: Suitable for processing complex curved surfaces, planes, and contours. Five – axis 联动 milling can complete spatial structures that are difficult to achieve with traditional processes.
- Data Indicators: Positioning accuracy is ±0.01mm, repeat positioning accuracy is ±0.02mm, and surface roughness Ra≤0.8μm. For example, when processing the three – dimensional curved surface of a plastic impeller, the profile error can be controlled within ±0.05mm to ensure hydrodynamic performance.
- Efficiency Optimization: High – speed milling (HSC) technology can increase the processing efficiency of materials such as ABS by 50%, with a rotational speed of 15000r/min and a feed rate of 3000mm/min.
- Process Characteristics: Used for precision processing of shaft – type and disk – type parts, such as the outer circle and thread forming of plastic screws.
- Data Indicators: The dimensional tolerance is controlled within ±0.01mm, and the surface roughness Ra≤0.4μm. Using diamond tools can further improve the surface quality, with the Ra value as low as 0.2μm.
- Process Characteristics: Achieves precision hole processing and thread forming, suitable for pin holes of electronic connectors, plastic fasteners, etc.
- Data Indicators: The drilling position accuracy is ±0.02mm, and the hole diameter tolerance is ±0.01mm (diameter ≥ 0.5mm); tapping can achieve a plastic thread accuracy of ISO 6H level, with a thread pitch diameter error ≤ ±0.03mm.
- Process Characteristics: Completes multi – surface processing in one clamping, solving the processing problems of complex spatial structures.
- Data Indicators: The position accuracy reaches ±0.02mm, and the processing efficiency is 60% higher than that of traditional processes. For example, the multi – directional flow channels and interfaces of a medical nebulizer valve body can be formed in one – step through five – axis milling, avoiding the accumulation of multi – process errors.
Material selection is a crucial step in customizing plastic parts, which needs to be comprehensively considered in combination with the functionality, environmental tolerance, and cost requirements of the application scenario:
- Insulation and Conductivity Requirements: ABS (insulation resistance ≥ 10^16Ω·cm) is used for the outer shells of electronic parts; conductive plastics (such as PA added with carbon fiber) are used for electrostatic dissipation components, and the volume resistivity can be reduced to 10^3 – 10^5Ω·cm.
- Chemical Resistance Optimization: PPS (Polyphenylene Sulfide) can withstand strong corrosive media such as concentrated sulfuric acid and sodium hydroxide, and remains stable at 175℃, which is suitable for plastic parts of chemical equipment.
- High – temperature Scenarios: PEEK (Polyetheretherketone) can be used for a long – term at 250℃ and withstand short – term high temperatures of 300℃, and is used for high – temperature – resistant parts in aerospace.
- Weather Resistance Requirements: ASA (Engineering Plastic Alloy) has excellent ultraviolet resistance. After 5000 hours of QUV accelerated aging test, the color difference ΔE≤2, which is suitable for the outer shells of outdoor equipment.
- Economical Solutions: PP (Polypropylene) has a low cost (about 12,000 yuan/ton) and good moldability, and is used for ordinary plastic container parts, with a tensile strength ≥ 20MPa.
- High – end Applications: Although PEEK has a relatively high cost (about 200,000 yuan/ton), it can replace metals in the medical field and is used to customize orthopedic implants, with both biocompatibility and mechanical strength (tensile strength ≥ 90MPa).
In view of the special properties of plastic materials, CNC processing technologies achieve a double breakthrough in efficiency and quality through the following technological innovations:
- When processing soft plastics (such as PE, PP), use sharp tools with a large rake angle (15° – 20°) to reduce material adhesion, and increase the feed rate to 3000mm/min.
- When processing hard plastics (such as POM, PC), apply coated tools (such as TiAlN coating), with a cutting speed of 500m/min, and the tool life is extended by 2 times.
- Adopt air cooling or minimum quantity lubrication (MQL) technology to reduce the impact of cutting heat on plastics and avoid the softening and deformation of materials such as PEEK.
- When processing thin – wall parts, through layer – by – layer cutting and adaptive feed strategies, reduce internal stress to ensure the dimensional stability of parts with a wall thickness of 0.3mm, and the deformation is ≤ 0.05mm.
To ensure that products meet industry standards and customer requirements, custom CNC plastic parts need to go through a strict quality control process:
- Use a coordinate measuring machine (CMM) for full – size scanning, and control the tolerance of key dimensions (such as the module of plastic gears) within ±0.02mm.
- Geometric tolerance detection: flatness ≤ 0.05mm/m, perpendicularity ≤ 0.03mm, to ensure the assembly accuracy of parts.
- Use infrared spectroscopy to confirm the plastic composition, such as the detection of characteristic absorption peaks of PEEK.
- Mechanical property tests: tensile tests (such as POM tensile strength ≥ 60MPa), impact tests (such as ABS notched impact strength ≥ 20kJ/m²), to ensure compliance with standards such as GB/T 1040.
- Use a roughness tester to detect the surface Ra value, and precision parts need to reach Ra≤0.4μm.
- Functional tests: such as the airtightness test of plastic seals, with a leakage rate ≤ 1×10^-7 Pa·m³/s.
- Custom – made ABS plastic connector outer shells are precisely milled by CNC. The interface size tolerance is ±0.01mm, ensuring signal transmission stability, and the insertion and extraction life reaches more than 1000 times.
- Conductive plastic (PA + carbon fiber) heat sinks are formed by CNC, with a 40% increase in thermal conductivity, meeting the high – efficiency heat – dissipation requirements of 5G base – station equipment.
- PEEK plastic intervertebral fusion cages are carved and formed by CNC, with a controllable porosity (30% – 50%) to promote bone tissue growth, and the mechanical strength is ≥ 150MPa.
- The PPS plastic valve body of the medical nebulizer has a surface roughness Ra≤0.8μm, reducing the residual liquid medicine by 50% and improving the treatment effect.
- Custom – made nylon (PA66) automotive engine hoods are injection – molded and precisely processed by CNC, reducing the weight by 30% and withstanding high temperatures of 150℃, meeting the harsh environment of the engine compartment.
- PEEK plastic brackets for aerospace are milled by five – axis CNC. While reducing the weight by 40%, they maintain a tensile strength of ≥ 90MPa, improving the energy efficiency of aircraft.
- What level of precision can custom plastic parts achieve?
CNC processing can achieve a dimensional tolerance of ±0.01mm, a repeat positioning accuracy of ±0.02mm, and a surface roughness Ra≤0.8μm, meeting the needs of most precision industries.
- How to choose the appropriate plastic material?
It needs to be comprehensively considered according to the functionality (such as insulation, chemical resistance), environmental tolerance (such as temperature, ultraviolet resistance), and cost of the application scenario. For example, choose PEEK for high – temperature environments, ASA for outdoor applications, and PP for economical scenarios.
- How long is the production cycle for custom plastic parts?
The production cycle depends on the complexity of the parts, the type of material, and the order quantity. Simple parts usually take 3 – 7 days, and complex parts may take 10 – 15 days. Urgent customization is supported.
- What are the options for the surface treatment of plastic parts?
Common treatments include polishing (Ra≤0.4μm), sandblasting, painting, electroplating, etc., which can be customized according to appearance or functional requirements. For example, medical parts require a high – cleanliness surface, and outdoor parts require an ultraviolet – resistant coating.
- What is the cost of CNC – processed plastics?
The cost is affected by materials, processing complexity, accuracy requirements, and batch size. Generally, the cost of small – batch customization is relatively high, but CNC technology can reduce the unit cost by optimizing the process. In the long run, it is more cost – effective than traditional processes.
Inquire now and get a customized solution!
Whether it is the precision connectors of electronic devices, the highly biocompatible implants in the medical field, or the lightweight components in the automotive industry, our professional team will rely on the high – precision processing technology and materials engineering advantages of CNC technology to provide you with a full – process customization service from design, processing to inspection. Click to leave a message, and let us, with a rigorous technical system and reliable quality assurance, customize high – performance and low – cost plastic part solutions for your project, helping you achieve technological breakthroughs and industrial upgrades in the field of modern industry!