In a wide array of industries, from high – tech manufacturing to medical device production, stainless – steel sleeves play a crucial role in protecting components, facilitating smooth operation, and enhancing overall product durability. As the demand for top – tier, customized sleeves continues to soar, CNC (Computer Numerical Control) machining emerges as the go – to solution. With its unrivaled precision and flexibility, CNC machining ensures that every stainless – steel sleeve meets the most exacting standards. This article delves deep into the technical prowess, customization journey, material selection, quality control, and industry applications of custom CNC stainless – steel sleeves.
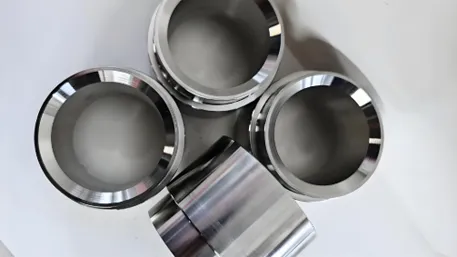
I. Technological Mastery: Revolutionizing Sleeve Manufacturing
(A) Unparalleled Precision
CNC machining systems are engineered to deliver pinpoint accuracy. With positioning accuracy reaching ±0.005mm and repeat positioning accuracy of ±0.01mm, we can fabricate sleeves with incredibly tight tolerances. For instance, when manufacturing sleeves for high – precision medical instruments, the inner diameter can be maintained within ±0.005mm, ensuring a perfect fit for the components they house. This level of precision not only optimizes performance but also minimizes the risk of mechanical failures due to misalignment.
(B) Complex Design Execution
Five – axis CNC machining technology unlocks the potential to create sleeves with complex geometries. Whether it’s sleeves with intricate grooves, tapered profiles, or multi – chamber designs, the five – axis system can execute these designs in a single setup. Compared to traditional machining methods, which often require multiple setups and are prone to errors, five – axis CNC machining reduces setup – related errors from ±0.03mm to within ±0.01mm. Moreover, it boosts production efficiency by over 60%, significantly shortening lead times.
(C) Advanced Process Optimization
To overcome challenges such as material deformation and surface roughness during sleeve machining, we deploy a suite of advanced techniques. By carefully selecting cutting parameters, optimizing toolpaths, and implementing real – time cooling systems, we can keep material deformation to a minimum. Additionally, the use of high – speed machining and advanced finishing processes results in sleeves with a superior surface finish, reducing friction and wear during operation.
II. End – to – End Customization: Tailoring to Your Needs
(A) In – Depth Requirement Gathering and Design Ideation
When you approach us with your sleeve requirements, our experienced engineering team engages in comprehensive discussions to understand your application, performance expectations, and design preferences. Leveraging state – of – the – art CAD/CAM software, we generate multiple design concepts. We then collaborate closely with you, refining the designs until they perfectly align with your vision.
(B) Strategic Material Selection and Cost Analysis
Based on the finalized design, we recommend the most suitable stainless – steel grade. We consider factors such as corrosion resistance, mechanical strength, and cost – effectiveness. Simultaneously, we conduct a detailed cost analysis, factoring in material costs, machining complexity, and production volume, to provide you with a transparent and competitive quote.
(C) Precision Manufacturing and Order Tracking
Once you approve the design and quote, production commences. You can monitor the progress of your order in real – time through our dedicated online tracking platform. Our skilled technicians adhere to strict manufacturing standards, using advanced CNC machines to produce sleeves that meet the highest quality benchmarks.
(D) Rigorous Quality Assurance and Timely Delivery
After production, each sleeve undergoes a rigorous quality inspection. Only sleeves that meet our exacting standards are shipped to you. We also offer comprehensive after – sales support, addressing any concerns you may have during the product’s lifecycle.
III. Smart Material Selection: Matching the Right Material to the Right Application
(A) 304 Stainless Steel: The Versatile Workhorse
304 stainless steel, with a density of 7.93g/cm³, offers an excellent balance of cost, corrosion resistance, and machinability. It has a tensile strength of ≥515MPa, a yield strength of ≥205MPa, and an elongation of ≥40%. This makes it an ideal choice for applications in general manufacturing, where cost – effectiveness and basic corrosion protection are key.
(B) 316L Stainless Steel: The Corrosion – Resistant Champion
316L stainless steel, with a density of 7.98g/cm³, contains 2 – 3% molybdenum, which significantly enhances its resistance to chloride – induced corrosion. It has a tensile strength of ≥485MPa, a yield strength of ≥170MPa, and an elongation of ≥40%. This grade is particularly suitable for applications in the medical, marine, and food processing industries, where high – level corrosion resistance is non – negotiable.
(C) 17 – 4 PH Stainless Steel: The High – Strength Option
17 – 4 PH stainless steel combines high strength with good corrosion resistance. After heat treatment, it can achieve a hardness of up to HRC 40 – 45. It is often used in aerospace and high – performance machinery applications, where components need to withstand extreme mechanical stresses.
IV. Stringent Quality Control: Ensuring Excellence at Every Step
(A) Raw Material Screening
All incoming stainless – steel materials are subjected to strict quality checks. We use spectroscopic analysis to verify the chemical composition, ensuring that it meets the required standards. Additionally, hardness testing and metallographic analysis are performed to confirm the material’s integrity.
(B) In – Process Monitoring
Throughout the manufacturing process, we employ statistical process control (SPC) techniques to monitor key manufacturing parameters. Regular sampling and data collection help us identify and correct any potential issues promptly, ensuring consistent product quality.
(C) Final Product Validation
Before shipping, each sleeve undergoes a comprehensive inspection. We use coordinate measuring machines (CMMs) to verify dimensional accuracy, ensuring that all critical dimensions are within ±0.005mm. Surface roughness is also measured to ensure it meets the specified requirements. In addition, we perform mechanical and corrosion resistance tests to validate the sleeve’s performance.
V. Diverse Industry Applications: Empowering Multiple Sectors
(A) Medical Devices
In the medical field, custom CNC stainless – steel sleeves are used in a variety of devices, from surgical instruments to diagnostic equipment. Their high precision and biocompatibility (especially when made from 316L stainless steel) ensure safe and reliable operation.
(B) Aerospace
Aerospace applications demand components that can withstand extreme conditions. Custom CNC stainless – steel sleeves, particularly those made from 17 – 4 PH stainless steel, are used in aircraft engines, landing gear systems, and avionics equipment, providing the necessary strength and corrosion resistance.
(C) Industrial Machinery
In industrial settings, stainless – steel sleeves protect shafts, bearings, and other components from wear and corrosion. Custom CNC – machined sleeves can be designed to fit specific machinery, improving operational efficiency and extending equipment lifespan.
VI. Frequently Asked Questions (FAQ)
(A) What is the typical precision of custom CNC stainless – steel sleeves?
Our CNC machining can achieve a dimensional tolerance of ±0.005mm, ensuring a precise fit for your applications.
(B) How do I choose the right stainless – steel material for my sleeves?
The choice depends on your application’s requirements. If cost – effectiveness and general corrosion resistance are sufficient, 304 stainless steel is a good option. For highly corrosive environments, 316L stainless steel is recommended. In high – stress applications, 17 – 4 PH stainless steel is the way to go.
(C) What is the lead time for custom sleeves?
Lead times vary depending on the complexity of the design and order quantity. Simple designs can be completed in 3 – 5 days, while more complex ones may take 7 – 10 days. Rush orders are available upon request.
(D) Can CNC machining handle complex sleeve designs?
Absolutely. Our five – axis CNC machines can fabricate sleeves with intricate geometries, meeting even the most demanding design requirements.
(E) How much does it cost to customize stainless – steel sleeves?
Costs are determined by factors such as material, design complexity, precision requirements, and order quantity. While small – batch customization may be relatively costly, economies of scale can significantly reduce per – unit costs for larger orders.
VII. Customer Testimonials
A leading medical device manufacturer approached us to develop custom 316L stainless – steel sleeves for a new surgical instrument. Our team used five – axis CNC machining to achieve the required precision of ±0.005mm. The sleeves not only met the strict quality standards of the medical industry but also helped the manufacturer streamline their production process. As a result, they were able to launch their new product ahead of schedule.
An aerospace company needed high – strength 17 – 4 PH stainless – steel sleeves for their aircraft engine components. We implemented advanced machining techniques and rigorous quality control measures to ensure that the sleeves could withstand the extreme conditions of flight. The customer reported a significant reduction in component failures, leading to improved aircraft reliability and reduced maintenance costs.
Reach Out Now for Your Custom CNC Stainless – Steel Sleeves!
Regardless of your industry or application, our team of experts is ready to collaborate with you. We offer a seamless end – to – end service, from design to delivery. Contact us today to discuss your project requirements and take the first step towards getting top – quality custom CNC stainless – steel sleeves.