In the competitive toy market, custom plastic shells for toy cars have become a core factor in enhancing product competitiveness through material innovation, process optimization, and precise customization. This article analyzes material selection, processing technology, customization processes, and quality control, combining real data and industry standards to provide actionable solutions for toy manufacturers.
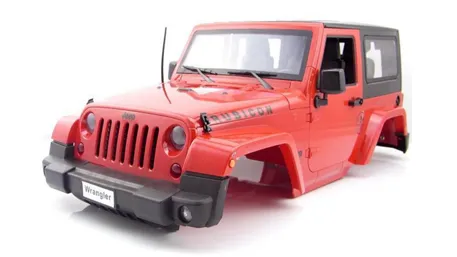
Materials for custom toy car plastic shells must balance safety certification, mechanical properties, and cost. Key data for common materials are as follows:
Material |
Tensile Strength (MPa) |
Temperature Resistance (℃) |
Safety Certifications |
Typical Applications |
ABS |
45-55 |
-20~80 |
EN71/GB 6675 |
Remote-control car shells, high-end models |
PP |
30-40 |
-10~120 |
FDA food-contact grade |
Soft plastic toys for toddlers |
PC |
60-70 |
-40~130 |
Lead-free certification |
Transparent concept car shells |
TPE |
5-15 (break) |
-50~90 |
Phthalates ≤0.1% |
Tires, bumpers |
Through mechanical property testing and environmental safety certification, shells are ensured to be drop-resistant (impact strength ≥20 kJ/m²), weather-resistant (color change ≤Grade 1 after 500 hours of UV aging), and compliant with global toy safety standards.
- Mold Flow Analysis: Using Moldflow to simulate material filling, shrinkage marks are controlled below 0.5%, and warpage deformation ≤0.08 mm/m.
- Mold Precision: Mold cavities are machined via slow wire electrical discharge machining, with dimensional tolerance ±0.01 mm and surface roughness Ra≤0.2 μm, ensuring 1:1 design replication.
- Molding Efficiency: High-speed injection machines with 8-cavity molds achieve a daily output of 2,000 pieces, increasing efficiency by 40% compared to traditional molds.
- Painting: Automatic reciprocating sprayers control paint thickness at 50±5 μm, with adhesion passing the cross-cut test (ISO 2409) and peeling rate ≤3%.
- Electroplating: Chrome plating thickness of 10-15 μm passes 48-hour salt spray testing without corrosion, with glossiness ≥90GU (60° measurement).
- IMD (In-Mold Decoration): Pattern positioning accuracy ±0.1 mm, with no surface wear after 500 friction tests.
- Product Definition: Clarify toy type (e.g., electric/remote-control/static model), target age group (0-3/3-6/6+ years), and expected annual sales (e.g., 50,000 units).
- Technical Collaboration: Provide CAD drawings or sketches, and confirm key parameters (e.g., shell wall thickness 1.5-3 mm, assembly tolerance ±0.05 mm).
- Cost Evaluation: Deliver material proposals (e.g., ABS ¥8/piece, PP ¥5/piece) and mold quotes (simple mold ¥20,000, precision mold ¥150,000) within 3 days.
- 3D Modeling: Use UG/NX to create 3D models, optimizing snap fits and reinforcing ribs to reduce cracking risks.
- Sample Production: Produce first samples via 3D printing (accuracy ±0.1 mm) or silicone molds (minimum order 50 pieces) for trial assembly.
- Design Iteration: Adjust details based on feedback (e.g., headlight light transmittance improved from 85% to 92%) until final approval.
- Mold Material: High-hardness mold steel (HRC52-54) with a service life of ≥500,000 cycles; key cores use insert designs for easy maintenance.
- Smart Machining: Manufactured via 5-axis CNC machining centers with precision ±0.005 mm; cooling channel design reduces molding cycle by 25%.
- Process Parameters: ABS injection temperature 230±5℃, holding pressure 60 MPa, cooling time 15 seconds, single-mold cycle 45 seconds.
- Capacity Configuration: 100,000-unit orders use 2 injection machines for 24/7 production, with delivery in 45 days.
Inspection Item |
Standard Requirements |
Testing Equipment |
Pass Criteria |
Dimensional Accuracy |
Critical dimensions ±0.05 mm |
Coordinate Measuring Machine (CMM) |
CPK≥1.67 |
Surface Defects |
Bubbles >0.2 mm ≤1 piece |
Visual inspection line |
Defect rate <0.1% |
Drop Test |
No cracking after 3 drops from 1.5m |
Drop tester |
Fracture rate = 0 |
Heavy Metal Migration |
Lead ≤90 ppm, Cadmium ≤75 ppm |
ICP-MS spectrometer |
Below detection limit |
- Packaging: Pearl cotton lining + corrugated carton (50 pieces/carton), compressive strength ≥5,000 N, ensuring transportation damage rate <0.05%.
- After-Sales: 7×24-hour feedback channel, solutions provided within 48 hours, and free replacement of defective products within 3 months.
- Lightweight Design: Thin-wall injection molding (wall thickness reduced to 1.2 mm) cuts material consumption by 15% while maintaining drop resistance.
- Digital Twin Technology: Simulating molding processes during mold design reduces trial runs from 5 to 1, shortening development cycles by 30%.
- Sustainability Upgrades: Recycled ABS (≥30% recycled content) reduces carbon emissions by 20%, complying with the EU EPR directive.
Q1: How to control costs for small-batch customization?
A: For orders under 1,000 pieces, 3D-printed molds reduce costs by 60%, with unit costs 35% lower than traditional molds, supporting rapid prototyping (first sample delivered in 3 days).
Q2: How to ensure precision for complex curved shells?
A: Reverse engineering scans real car models (accuracy ±0.02 mm) and multi-slider mold structures achieve curve radius errors <0.5° and edge sharpness ≥95%.
Q3: What is the shortest delivery time for urgent orders?
A: Existing mold orders deliver within 72 hours; new mold orders for 100,000 pieces can be rushed in 45 days (20% faster than standard cycles).
“For a 100,000-unit order of children’s remote-control car shells, the team completed the process from design to delivery in just 42 days, 30% faster than expected. The shells met ±0.03 mm dimensional accuracy, with a 99.8% no-crack rate in 1.5m drop tests, and electroplated surfaces passing 72-hour salt spray testing without corrosion. Proactive optimization of mold cooling systems reduced unit costs by 12%, with a defect rate controlled at 0.08%. Their professionalism and execution inspire confidence for long-term collaboration!” ——Senior Procurement Specialist in the Toy Industry
Whether you’re creating adorable toddler toys or high-end collectible models, we offer:
- One-on-One Professional Consultation: Senior engineers tailor material and process solutions to your needs.
- End-to-End Quality Assurance: Rigorous testing at every stage ensures precision, safety, and durability.
- Flexible Services: Support small-batch trials and urgent orders, with the fastest 3-day prototyping and 45-day mass production.
A child’s laughter begins with a well-crafted toy car; your success starts with a professional customization partnership. Click below to share your requirements and turn every toy car shell into a market highlight!