In the era of consumption upgrading and refined product packaging, custom transparent plastic boxes have become a core packaging solution for industries such as food, electronics, and cosmetics, thanks to their high light transmittance, moisture resistance, and design flexibility. This article systematically analyzes the technical logic and industrial value of transparent plastic boxes, covering material selection, processing technology, customization processes, and application scenarios, providing professional guidance for brands seeking tailored packaging solutions.
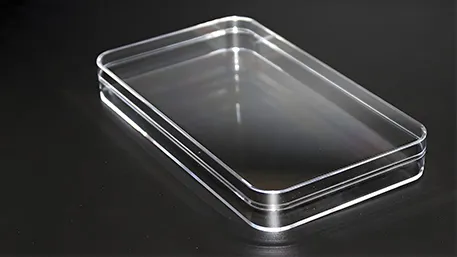
Materials for custom transparent plastic boxes must balance light transmittance, mechanical properties, temperature resistance, and safety certifications. Key parameters for common materials are as follows:
Material |
Transmittance (%) |
Tensile Strength (MPa) |
Temperature Resistance (℃) |
Safety Certifications |
Typical Applications |
Polyethylene Terephthalate (PET) |
≥90 |
40-60 |
-20~60 |
FDA/GB 4806 |
Food packaging, gift boxes |
Polypropylene (PP) |
85-90 |
30-40 |
-10~120 |
Food-contact grade |
Microwave meal boxes, fresh produce trays |
Polycarbonate (PC) |
≥92 |
60-70 |
-40~130 |
Lead-free certification |
Electronic component packaging, optical device cases |
Polystyrene (PS) |
≥88 |
35-45 |
-10~70 |
General packaging grade |
Disposable transparent boxes, toy packaging |
Polyvinyl Chloride (PVC) |
85-90 |
45-55 |
-15~50 |
RoHS compliant |
Cosmetic storage boxes, jewelry cases |
Through light transmittance testing (haze ≤5%) and yellowing resistance testing (ΔE ≤3 after 1,000 hours of UV aging), we ensure that transparent boxes remain clear and deformation-free during long-term use.
Process |
Characteristics |
Precision (mm) |
Daily Capacity (pcs) |
Suitable Scenarios |
Injection Molding |
Complex structures in one step |
±0.05 |
5,000-20,000 |
High-end boxes with snaps/hinges |
Blister Molding |
Low-cost rapid production |
±0.1 |
10,000-50,000 |
Shallow trays (e.g., fruit boxes) |
Blow Molding |
Hollow transparent boxes |
±0.2 |
8,000-30,000 |
Curved/irregular packaging |
Compression Molding |
High-transparency sheet processing |
±0.03 |
3,000-10,000 |
Precision electronic component trays |
- Printing Processes:
- Silk Screen Printing: Precision ±0.1 mm, supports CMYK full-color system, adhesion passes 3M tape test (peeling ≤5%).
- Hot Stamping (Gold/Silver): Temperature controlled at 120±5℃, pressure 8-10 kg/cm², metal foil adhesion ≥95%.
- Functional Coatings:
- Anti-Static Coating: Surface resistance ≤10⁹ Ω, effectively preventing dust adsorption on electronic components (suitable for PC/PS materials).
- Anti-Fog Treatment: Hydrophilic coating technology ensures fog resistance ≥30 minutes under 20℃ temperature difference (ideal for fresh produce packaging).
- Scenario Definition: Clarify usage (e.g., food packaging/electronic storage/gift display), content characteristics (weight/size/ storage conditions), and appearance requirements (transparency/color/opening method).
- Technical Parameters: Discuss dimensional tolerances (e.g., ±0.03 mm for precision electronic boxes, ±0.1 mm for general packaging) and sealing grades (e.g., IP54 dust/water resistance for food boxes).
- Cost Evaluation: Provide material proposals (e.g., PET boxes ¥0.5-2/piece, PC boxes ¥2-5/piece) and mold quotes (simple mold ¥10,000-30,000, precision mold ¥50,000-150,000) within 3 days.
- 3D Modeling: Use SolidWorks to design box structures, optimizing snap-fit pull force (≥5 N) and hinge lifespan (≥10,000 openings/closing), with wall thickness simulation (recommended 0.8-1.5 mm for food boxes).
- Sample Production:
- 3D Printing (SLA Technology): Precision ±0.05 mm, first sample delivered in 3 days, ideal for complex structure verification.
- Silicone Mold Small Batch: Minimum order 50 pieces, cost 40% lower than steel molds, for physical sample approval.
- Mold Materials:
- Food-Grade Molds: Made of S136 stainless steel (HRC52 hardness), compliant with FDA 21 CFR 177.1640 to prevent material migration risks.
- Precision Molds: CNC machining precision ±0.01 mm, runner design ensures balanced melt filling, reducing sink marks (depth ≤0.1 mm).
- Production Parameters:
- PET Injection Molding: Temperature 260±5℃, cooling time 10-15 seconds, daily capacity 10,000 pieces (4-cavity mold).
- Blister Molding: Heating temperature 180-220℃, vacuum degree ≥90 kPa, sheet material utilization ≥85%.
- Quality Standards:
- Transmittance Test: Measured by haze meter, transmittance deviation ≤2%.
- Sealing Test: Vacuumed to -90 kPa, pressure retention 30 seconds, leakage ≤5 kPa (for food packaging).
- Packaging Solution: Pearl cotton separation + carton packaging (500 pieces/carton), passing ISTA 3A drop test (1.2m height, no damage).
- After-Sales Support: 48-hour quality issue response, free replacement for orders with defect rate >0.5%, 1-year mold warranty (excluding normal wear).
- Fruit/Bakery Packaging: PET blister boxes with easy-peel film, transmittance ≥90%, oxygen permeability ≤50 cm³/(m²·24h·atm), extending shelf life by 3-5 days.
- Frozen Food Containers: PP material resistant to -20℃, passing microwave heating test (120℃, 30 minutes, no deformation), suitable for ready-to-eat meals.
- Chip Trays: PC injection-molded boxes with surface resistance ≤10⁸ Ω, ESD certification, dimensional tolerance ±0.03 mm, ensuring safe transportation of precision components.
- Lens Packaging: Inner wall flocking (friction coefficient ≤0.3), with buffer slots, lens displacement ≤0.5 mm after 1m drop test.
- Skincare Sample Boxes: PVC transparent boxes with hot-stamped LOGO, snap-fit pull force ≥8 N, IP54 sealing to prevent lotion leakage.
- Jewelry Storage Boxes: PS material with electroplated surface, glossiness ≥85GU, inner flannel fitting error ≤0.2 mm, enhancing gift aesthetics.
Sustainable Material Upgrades
- Bio-Based PET (Corn Starch Derived): Degradation rate ≥90%, carbon emissions reduced by 40%, suitable for disposable food packaging.
- Recycled Transparent Plastic (rPET): Recycling content ≥50%, compliant with GRS (Global Recycle Standard), meeting EU Packaging Law (PPW) requirements.
Intelligent Function Integration
- Temperature/Humidity Monitoring Boxes: Built-in RFID sensors, real-time environment recording (accuracy ±2℃/±5%RH), data traceable for 180 days.
- Anti-Counterfeit Packaging: UV fluorescent ink for hidden patterns, only visible under specific wavelength light, increasing forgery difficulty by 60%.
Structural Design Innovations
- Foldable Transparent Boxes: Unfolding size error ≤1%, folding lifespan ≥500 times, saving 30% transportation volume.
- Magnetic Closure Boxes: Magnetic force ≥15 N, smooth opening/closing, enhancing user experience.
Q1: What is the minimum order quantity for custom transparent plastic boxes?
A: The minimum order for steel molds is 5,000 pieces. Small batches (500 pieces 起订) can use silicone molds, with unit costs 30% higher than steel molds—ideal for samples or limited editions.
Q2: How to ensure long-term transparency of the boxes?
A: We use yellowing-resistant materials (e.g., PET with UV stabilizers) and pass 1,000-hour QUV aging tests, with transmittance loss ≤5% and haze increase ≤3%.
Q3: What certifications are required for food-grade transparent boxes?
A: Certifications include China GB 4806, US FDA 21 CFR 177.1630, and EU EU 10/2011, ensuring heavy metal migration ≤0.1 ppm and potassium permanganate consumption ≤10 mg/L.
Q4: What is the lead time for complex irregular boxes?
A: The full cycle including mold development is 45-60 days: 10 days for design confirmation, 25 days for mold processing, and 10 days for production. Rush orders can be delivered in as little as 30 days.
“For a 50,000-unit order of high-end cosmetic transparent gift boxes, the team completed the process from design to delivery in just 40 days. The boxes achieved 92% transmittance, with an average snap-fit pull force of 12 N and passed 48-hour submersion testing without leakage. Proactive mold runner optimization increased production yield from 92% to 97%, with a transportation damage rate controlled at 0.03%. Their professionalism and attention to detail were impressive—we’ll continue collaborating on transparent packaging projects!” ——Packaging Procurement Lead in the Beauty Industry
Whether you need safe food packaging, premium gift boxes, or precision electronic cases, we offer:
- Free Material Selection Consultation: Tailored material recommendations (PET/PC/PP, etc.) with detailed performance comparison charts, based on your content requirements.
- End-to-End Visibility: Real-time project updates from 3D design to quality control, ensuring every detail meets your expectations.
- One-Stop Solutions: Full-chain services covering mold development, mass production, and logistics—making customization effortless.
Click below to share your transparent box requirements and let every product shine in packaging that showcases its value!