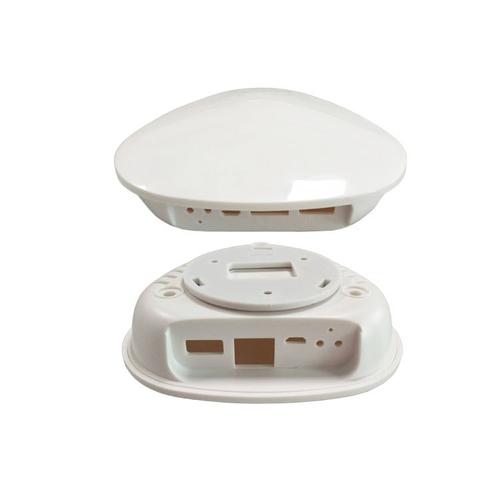
1. Why Custom Communication Equipment Plastic Enclosures
2. Communication Equipment Plastic Enclosure Processing Technologies
- Injection Molding: Melts plastic resin and injects it into precision molds under high pressure, producing enclosures with consistent wall thickness, intricate details (port cutouts, ribbing), and tight tolerances (±0.05mm). Ideal for high-volume production and complex geometries.
- CNC Machining: Uses computer-controlled routers to shape enclosures from solid plastic blocks, suitable for low-volume production or prototyping. Enables quick modifications to dimensions or feature designs.
- Thermoforming: Heats plastic sheets and forms them over molds, cost-effective for large, shallow enclosures (outdoor antenna housings). Offers faster turnaround for medium-volume runs.
- 3D Printing: Builds enclosures layer-by-layer from plastic filaments (ABS, PC) or resins, perfect for rapid prototyping or custom enclosures with unique internal structures (cable management channels).
- Ultrasonic Welding: Joins multi-part enclosures by vibrating components at high frequency, creating strong, hermetic seals without adhesives—critical for waterproof or dustproof designs.
3. Communication Equipment Plastic Enclosure Processing Flow
- Design & Engineering: Collaborate with clients to gather device specs (dimensions, heat output, port locations) and environmental requirements (IP rating, temperature range). Use CAD and FEA software to optimize structural integrity and cooling efficiency.
- Material Selection: Choose plastics based on performance needs—ABS for balance of strength and cost, PC for impact resistance, PBT for heat tolerance, or specialty blends with EMI shielding additives.
- Mold Fabrication: Create steel molds for injection molding, incorporating features like ejector pins, cooling channels, and inserts for metal threads (for ports). Molds are precision-machined to ensure accurate replication of enclosure details.
- Production: For high volumes, use injection molding; for prototypes or small batches, employ 3D printing or CNC machining. Process parameters (temperature, pressure) are tuned to the selected material to prevent warping or porosity.
- Finishing: Trim excess material, drill or tap holes for ports, and apply surface treatments (texturing for grip, painting for UV resistance). Add hardware like metal inserts for screws or gaskets for waterproofing.
- Assembly & Integration: Install components like EMI gaskets, ventilation grilles, or cable management clips. Test fits with the target communication device to ensure proper alignment.
- Quality Testing: Conduct environmental tests (IP rating verification, temperature cycling), impact resistance checks, and EMI/RFI shielding effectiveness measurements to ensure compliance with specifications.
4. Communication Equipment Plastic Enclosure Materials
- ABS (Acrylonitrile Butadiene Styrene): Offers a balance of strength, impact resistance, and cost-effectiveness. Suitable for indoor enclosures (routers, modems) requiring good dimensional stability and ease of machining.
- PC (Polycarbonate): Provides exceptional impact resistance (20x stronger than glass) and transparency, ideal for enclosures needing visibility (status indicators) or outdoor use (antennas, outdoor transceivers).
- PBT (Polybutylene Terephthalate): Boasts high heat resistance (up to 150°C) and chemical resistance, making it suitable for enclosures housing high-power devices (transmitters, amplifiers) that generate significant heat.
- PVC (Polyvinyl Chloride): Offers good weatherability and flame resistance, used for outdoor enclosures (cable junction boxes) requiring UV resistance and low cost.
- Specialty Blends: Combinations like PC/ABS (enhanced impact + heat resistance) or plastics with conductive additives (carbon fiber, metal particles) for EMI/RFI shielding in sensitive equipment.
5. Communication Equipment Plastic Enclosure Applications
- Networking Devices: Enclosures for routers, switches, and modems, featuring precise port cutouts and ventilation to prevent overheating. Often designed for wall or rack mounting.
- Telecom Infrastructure: Housings for fiber optic transceivers, DSL modems, and base station components, engineered for durability in telecom towers or underground vaults.
- Wireless Equipment: Outdoor enclosures for antennas, access points, and cellular repeaters, with IP65/IP66 ratings to resist rain, snow, and dust.
- Industrial Communication: Rugged enclosures for factory floor devices (Ethernet switches, IoT gateways), featuring impact resistance (IK08+) and chemical resistance to oils and solvents.
- Aerospace & Defense: Lightweight, EMI-shielded enclosures for avionics communication systems and military radios, meeting strict standards for vibration resistance and temperature extremes.
- Consumer Electronics: Compact enclosures for portable hotspots, Bluetooth adapters, and home Wi-Fi extenders, balancing aesthetics with functional port access.
6. Communication Equipment Plastic Enclosure Performance Additions
- EMI/RFI Shielding: Integrate conductive coatings (nickel, copper) or metal meshes to block electromagnetic interference, critical for sensitive devices like radio transceivers or radar equipment.
- Environmental Sealing: Add gaskets (silicone, EPDM) to achieve IP65/IP68 ratings, protecting internal components from water, dust, and humidity—essential for outdoor or industrial use.
- Thermal Management: Design heat sinks, vent channels, or fan mounts to dissipate heat from high-power devices (5G transceivers), preventing overheating and ensuring reliable operation.
- Mounting Systems: Incorporate flanges, brackets, or rail attachments (DIN rails) for easy installation in racks, walls, or poles, adapting to diverse deployment scenarios.
- Security Features: Add tamper-evident screws, lockable latches, or RFID tags to prevent unauthorized access, protecting sensitive equipment in public or remote locations.
- UV Resistance: Apply UV-stabilized pigments or coatings to prevent degradation from sunlight, extending enclosure life in outdoor applications by 3–5 years.
7. Communication Equipment Plastic Enclosure Common Questions
Which material is best for outdoor enclosures?
PC (polycarbonate) or UV-stabilized ABS are ideal—PC offers superior impact resistance and weatherability, while UV-stabilized ABS provides a cost-effective balance of durability and performance. Both can be sealed to achieve IP65/IP66 ratings.
Can enclosures provide EMI shielding?
Yes—by incorporating conductive additives (carbon black, metal fibers) into the plastic or applying conductive coatings (copper, nickel). Shielding effectiveness ranges from 40–80 dB, sufficient for most communication devices.
How are enclosures tested for environmental resistance?
They undergo IP rating testing (water spray, dust chambers), temperature cycling (-40°C to 85°C), and vibration testing to simulate transportation or outdoor conditions. Results are documented to verify compliance with specifications.
What’s the typical lead time for custom enclosures?
Prototyping (3D printing/CNC) takes 1–2 weeks. Production tooling for injection molding takes 4–6 weeks, with mass production following in 2–3 weeks. Rush options are available for urgent projects.
Can enclosures accommodate custom port configurations?
Absolutely—custom designs can integrate any combination of ports (Ethernet, USB, coaxial), with precise hole sizing and spacing to match device connectors. 3D modeling ensures perfect alignment during production.