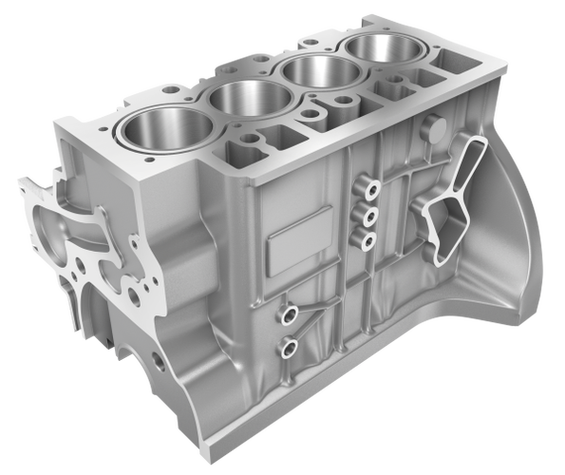
Table of Contents
- Automotive Engine Die Castings: The Core Carrier of Power Systems
- Custom Material Selection: Decoding the Material Code for Harsh Engine Conditions
- Precision Manufacturing Processes: The Transformation from Liquid Metal to Engine Core Components
- Core Technological Breakthroughs: Conquering High-Temperature, High-Pressure, and High-Reliability Challenges
- Full-Process Quality Control: The Pursuit of Zero Defects Under Automotive-Grade Standards
- Agile Service System: Matching the High-Efficiency Development Needs of the Automotive Industry
- Engine Die Casting FAQs: Professional Answers to Key Customization Questions
1. Automotive Engine Die Castings: The Core Carrier of Power Systems
- High-Temperature & High-Pressure Adaptation: Operating continuously at 200℃~300℃ and withstanding 10-20MPa explosion pressure, aluminum alloy die castings require a tensile strength ≥300MPa to ensure stable operation of combustion chamber components (cylinder blocks, cylinder heads).
- Complex Structure Integration: Integrated die casting forms multi-cavity channels (e.g., cooling water channels, oil paths) with hole diameter tolerances of ±0.03mm, reducing welding processes by 40% and improving sealing (leakage rate ≤5cc/min).
- Lightweight Imperative: Achieving 30%-50% weight reduction compared to cast iron components; for example, aluminum alloy cylinder blocks are 40% lighter than cast iron, reducing engine weight and improving fuel efficiency by 5%-8%.
2. Custom Material Selection: Decoding the Material Code for Harsh Engine Conditions
1. Main Alloy Properties and Typical Applications
Alloy Type
|
Typical Grade
|
Core Performance Indicators
|
Engine Component Applications
|
Aluminum Alloy
|
A380
|
Tensile strength ≥320MPa, high-temperature resistance (strength retention ≥70% at 300℃)
|
Cylinder blocks, cylinder heads, intake manifolds
|
Aluminum Alloy
|
ADC12
|
Thermal conductivity ≥180W/(m·K), excellent airtightness (porosity ≤1%)
|
Oil pans, water pump housings
|
Magnesium Alloy
|
AZ91D
|
Density 1.8g/cm³, damping coefficient 0.05 (vibration attenuation ≥35%)
|
Engine mounts, timing chain cases
|
2. Custom Material Design
- Combustion Chamber Components: Adding 0.5% Mg + 0.3% Ni to A380 alloy increases tensile strength by 15% at 300℃ and enhances thermal fatigue resistance by 20%, suitable for high-temperature environments in turbocharged engines.
- Lubrication System: Controlling Fe≤0.9% in ADC12 alloy and using refining degassing to reduce hydrogen content to ≤0.15ml/100g minimizes the risk of lubrication failure due to internal oil path gas holes.
3. Precision Manufacturing Processes: The Transformation from Liquid Metal to Engine Core Components
1. Mold Design: 0.01mm-Level Precision Mastery
- Thermal Balance Optimization:
-
- Conformal cooling channels (spacing 3-5 times pipe diameter) limit mold temperature fluctuation to ±5℃, avoiding solidification shrinkage caused by uneven cylinder block wall thickness (shrinkage rate controlled at 0.8%-1.0%).
-
- Tungsten steel inserts (hardness HRC65) for deep cavities ensure coaxiality ≤0.02mm for 10mm deep holes (e.g., cylinder head bolt holes).
- Mold Flow Analysis Enhancement: Simulating high-pressure filling (injection speed 60m/s) via Moldflow to optimize gate position (≥8mm from hot spots), reducing shrinkage porosity from 5% to 0.8%.
2. Die Casting: Engine-Exclusive Processes
- Vacuum Die Casting Technology:
-
- Vacuum degree ≤50mbar with three-stage pressure boosting (initial 80MPa → intermediate 120MPa → final 180MPa), achieving cylinder block internal density ≥99.5% and X-ray flaw detection defect rate <0.1%.
-
- Intelligent mold temperature control (aluminum alloy molds 180±3℃) ensures cylinder head valve seat hole dimensional fluctuation ≤±0.03mm for high-precision assembly.
- Semi-Solid Die Casting: Controlling solid phase rate at 50%-60% for magnesium alloy components, reducing filling pressure by 25% and crack occurrence rate from 12% to 2.5%.
3. Post-Processing: Function Enhancement and Precision Correction
- Precision Machining:
-
- Five-axis grinding for cylinder block planes (flatness ≤0.02mm/100mm) to ensure cylinder sealing.
-
- Honing for oil path holes (roughness Ra≤0.4μm), reducing oil flow resistance by 10% and improving lubrication efficiency.
- Surface Treatment:
-
- Cylinder head anodizing (film thickness 20μm), hardness ≥200HV, resistant to coolant corrosion (no peeling after 500 hours).
-
- Oil pan electrophoretic coating (film thickness 30μm), passing 1000-hour salt spray test without rust, suitable for wet 底盘 environments.
4. Core Technological Breakthroughs: Conquering High-Temperature, High-Pressure, High-Reliability Challenges
1. High-Temperature Strength Retention Technology
- Grain Refinement Treatment: Adding 0.2% Ti + 0.15% B refines aluminum alloy grains to below 50μm, increasing high-temperature (300℃) fatigue strength by 25% to meet 100,000 thermal cycle requirements for turbocharged engines without cracks.
- Structural Reinforcement Design: Variable wall thickness design (1.5mm minimum → 3mm maximum) in cylinder block stress-concentrated areas, combined with arc-shaped reinforcing ribs (2mm height), increases knock resistance by 30%.
2. Precision Cooling and Lubrication System Forming
- Micro-Channel Forming: Successfully casting 0.8mm-wide cooling water channels (depth-width ratio 3:1), increasing filling success rate to 92% via spiral mold runner design and improving heat dissipation efficiency by 15%.
- Oil Path Sealing Technology: Using vacuum leak testing (pressure 10kPa) with post-machining hole plugging to ensure oil path leakage rate ≤1cc/min, 30% better than industry standards.
3. Defect Detection Technology Upgrade
- CT Tomography: 0.2mm resolution detects internal shrinkage holes (volume ≤1mm³) in cylinder blocks, achieving 100% full-size 3D reconstruction and reducing miss rate from 5% (traditional X-ray) to 0.1%.
- Automatic Airtightness Detection: Helium mass spectrometer leak detection (accuracy 1×10⁻⁹mbar·L/s) for 100% cylinder head combustion chamber inspection, ensuring no leakage under high pressure.
5. Full-Process Quality Control: The Pursuit of Zero Defects Under Automotive-Grade Standards
1. Raw Material Control
- Spectral Analysis: Batch alloy composition testing (accuracy 0.01%), controlling Si content in A380 alloy at 11.5%-13.5% and Fe≤0.9% to eliminate material deviations at the source.
- In-Furnace Treatment: Adding C2Cl6 refining agent (0.5kg/ton) during aluminum alloy melting to reduce hydrogen content to ≤0.1ml/100g, minimizing gas hole defects.
2. Process Monitoring
- IoT Data Collection: Real-time monitoring of injection pressure (fluctuation ≤1%), mold temperature (deviation ±2℃), and cycle time (error ≤2 seconds), with automatic shutdown for anomalies (response time ≤15 seconds).
- First Article Full Inspection: CMM measurement of 50+ critical dimensions (Cpk≥1.67), including cylinder hole diameter (tolerance ±0.015mm) and flatness (≤0.03mm), ensuring 100% qualification before mass production.
3. Finished Product Inspection
Inspection Item
|
Inspection Method
|
Automotive-Grade Standard
|
Compliance Rate
|
Dimensional Accuracy
|
Coordinate Measuring Machine
|
Cylinder hole roundness ≤0.01mm, positional accuracy ±0.02mm
|
99.8%
|
Internal Defects
|
CT Scan + Ultrasonic Testing
|
0 tolerance for defects ≥0.5mm
|
100%
|
Airtightness Testing
|
Helium Mass Spectrometer
|
Leakage rate ≤5cc/min
|
99.5%
|
High-Temperature Strength
|
Electronic Universal Tester
|
Tensile strength ≥250MPa at 300℃
|
99.2%
|
6. Agile Service System: Matching the High-Efficiency Development Needs of the Automotive Industry
1. Collaborative R&D
- Early Design Involvement: Participating in customer engine development, providing wall thickness optimization (recommended 2-4mm) and demolding draft suggestions (1.5°-3°), reducing post-mold modification costs by 40%.
- Joint Material Development: Developing high thermal conductivity aluminum alloy (≥200W/(m·K)) for new energy engines, reducing motor controller housing temperature by 20℃, applied in a popular production model.
2. Rapid Delivery
- Rapid Prototyping: Aluminum simple molds deliver first samples in 10 days, supporting 3D printed prototype verification and shortening prototyping cycle by 50% compared to traditional methods.
- Mass Production: Equipped with 600-1600T large-scale die casting machines, monthly capacity 200,000 pieces, reducing delivery cycle for complex cylinder blocks by 35% compared to industry average.
3. After-Sales Assurance
- PPAP Document Support: Providing full-dimension inspection reports, material traceability records, and process FMEA to meet IATF 16949 certification requirements.
- On-Site Technical Service: Offering on-site process debugging for OEMs, resolving machining deformation and sealing issues, increasing yield from 85% to 97%.