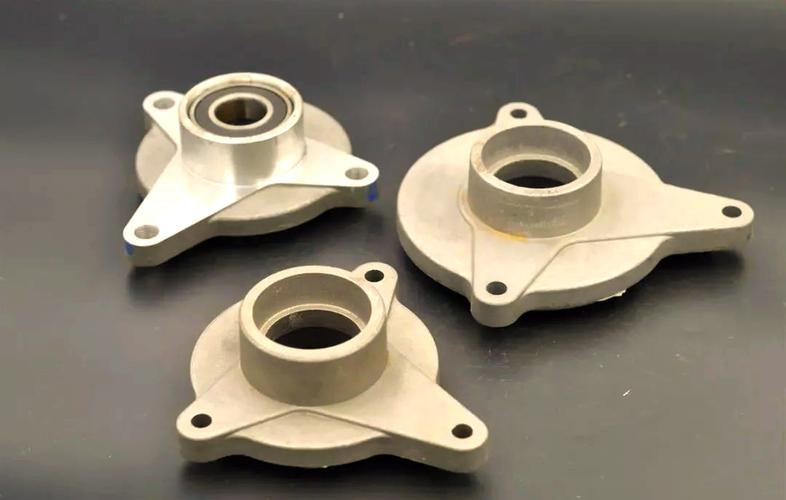
Table of Contents
- Aviation Aluminum Alloy Die Castings: The Core Lightweight Material for Aviation Industry
- Custom Material Selection: Decoding the Performance Code of Aviation-Grade Aluminum Alloys
- Precision Manufacturing Process: The Transformation from Liquid Metal to Aviation-Grade Parts
- Core Technological Breakthroughs: Overcoming Aviation-Grade Performance and Precision Challenges
- Aviation-Grade Quality Control: The Pursuit of Zero Defects under Stringent Standards
- Full-Cycle Custom Service: Matching the Extreme Needs of Aviation Industry
- Aviation Die Casting FAQs: Professional Answers to Key Customization Questions
1. Aviation Aluminum Alloy Die Castings: The Core Lightweight Material for Aviation Industry
- Core Lightweight Carrier: Achieve 40%-60% weight reduction compared to steel components. For example, 7075-T6 aluminum alloy die castings have a density of only 2.8g/cm³ and a tensile strength of up to 572MPa, reducing aircraft structural weight by 15%-20% and improving fuel efficiency by 8%-12%.
- Complex Structure Forming: Realize complex curved surface forming (curvature radius ≤5mm) for wing ribs, fuselage frames, etc., through integrated die casting, reducing part count by 30%-50% and assembly error (matching accuracy ±0.02mm).
- Harsh Environment Adaptation: Maintain stable performance in the temperature range of -55℃~150℃, with corrosion depth ≤5μm after 1,000 hours of salt spray testing, meeting extreme environment requirements such as high-altitude low temperature and humid marine conditions.
2. Custom Material Selection: Decoding the Performance Code of Aviation-Grade Aluminum Alloys
1. Main Alloy Grades and Performance Advantages
Alloy Type
|
Typical Grade
|
Core Performance Indicators
|
Typical Applications
|
2xxx Series
|
2024-T351
|
Tensile strength ≥470MPa, fatigue strength ≥140MPa, fracture toughness ≥24MPa·m¹/², suitable for high-stress structures
|
Wing ribs, fuselage frames
|
6xxx Series
|
6061-T6
|
Thermal conductivity ≥167W/(m·K), excellent stress corrosion resistance, good weldability, suitable for thermal management components
|
Engine heat dissipation housings, electronic equipment brackets
|
7xxx Series
|
7075-T651
|
Tensile strength ≥572MPa, hardness ≥150HB, outstanding fatigue resistance, meeting ultra-high load requirements for landing gear components
|
Landing gear brackets, engine mounting frames
|
2. Custom Material Design
- Composition Optimization: For high-temperature components of aero-engines, adding 0.15%-0.3% Zr refines the grain size to below 50μm, increasing high-temperature strength by 15% (tensile strength ≥300MPa at 300℃).
- Metallurgical Control: Using semi-continuous casting + homogenization annealing, the alloy composition segregation is <5%, ensuring batch fluctuation of mechanical properties ≤3%.
3. Precision Manufacturing Process: The Transformation from Liquid Metal to Aviation-Grade Parts
1. Mold Design: 0.005mm-Level Precision Attack
- Vacuum Mold Flow Analysis: Simulate molten metal flow under vacuum (≤30mbar) via Moldflow, optimizing gate position (≥10mm from stress-concentrated areas), reducing shrinkage porosity from 2% in conventional processes to below 0.3%.
- Mold Material and Machining:
-
- Cavity made of German imported 2344 tool steel, quenched at 1050℃ + three-time tempering at 560℃, hardness reaching 52HRC. Combined with laser texturing (surface roughness Ra≤0.2μm), achieving a mirror finish for aviation components.
-
- Precision inserts processed by slow wire EDM (accuracy ±0.003mm), ensuring forming accuracy (tolerance ±0.01mm) for 0.5mm thin-wall holes.
2. Die Casting: Aviation-Grade Process Control
- Vacuum Die Casting Technology:
-
- Injection speed increased to 80m/s, with three-stage pressure boosting (initial pressure 80MPa → intermediate pressure 120MPa → final pressure 180MPa), achieving casting density ≥99.5% and ultrasonic flaw detection defect rate <0.1%.
-
- Mold temperature control accuracy ±2℃ (realized via 3D printed conformal cooling channels), reducing deformation caused by uneven cooling (flatness error ≤0.05mm/100mm).
- Semi-Solid Die Casting: For difficult-to-form alloys like 7075, using thixotropic injection (solid phase rate 50%-60%), reducing filling pressure by 30% and crack occurrence rate from 15% to 2%.
3. Post-Processing: Micron-Level Precision Correction
- Precision Machining:
-
- Five-axis CNC machining center (positioning accuracy ±0.002mm) processes assembly datum surfaces with flatness ≤0.01mm, meeting the “zero-clearance” assembly requirement for aviation components.
-
- Electrochemical deburring (accuracy ±0.005mm) ensures no residue in 0.3mm deep narrow grooves, avoiding fatigue failure due to stress concentration.
- Surface Strengthening Treatment:
-
- Hard anodizing (film thickness 50-100μm), surface hardness ≥300HV, wear resistance increased by 5 times, suitable for landing gear connection parts.
-
- Electroless nickel-phosphorus alloy plating (coating thickness 15-25μm), passing 1,000 hours of salt spray testing without corrosion, meeting marine climate requirements.
4. Core Technological Breakthroughs: Overcoming Aviation-Grade Performance and Precision Challenges
1. Structural Lightweight Design Technology
- Topology Optimization Combined with Additive Manufacturing: Lightweight design via Altair Inspire removes 40% redundant material, while adding bionic reinforcing ribs (thickness 0.8-1.2mm) in stress-concentrated areas, reducing part weight by 25% and increasing stiffness by 20%.
- Thin-Wall Forming Technology: Breaking through the 1mm wall thickness limit, achieving 0.8mm thin-wall forming yield ≥95% (industry average 75%) through mold runner optimization (cross-sectional area error ±2%) and high-speed filling (speed ≥60m/s).
2. Simulation and Reliability Prediction
- Multi-Physical Field Coupling Analysis: Simulate part deformation under high-altitude low pressure (20kPa) and low temperature (-55℃) via ANSYS Workbench, prediction error ≤1.5%, ensuring dimensional stability during flight attitude changes.
- Fatigue Life Prediction: Based on Miner’s linear cumulative damage theory and flight load spectrum (100,000 cycles), fatigue life prediction error ≤8%, with 实测 life of key components ≥120% of design value.
3. Defect Detection Technology Upgrade
- CT Tomography: 0.1mm resolution detects internal defects, achieving 100% full-size 3D reconstruction, ensuring 100% identification of 气孔 ≥0.2mm (traditional X-ray detection miss rate 5%).
- Fluorescent Penetrant Inspection: Using aviation-specific penetrant (sensitivity level L1), detects 0.05mm micro-cracks with penetration time controlled at 15±2 minutes, ensuring zero miss of surface-breaking defects.
5. Aviation-Grade Quality Control: The Pursuit of Zero Defects under Stringent Standards
1. Material Traceability and Certification
- Blockchain Traceability System: Full-process data on-chain from aluminum ingot melting (furnace number traceability) to finished product delivery, material composition deviation ≤0.05%, ensuring compliance with AMS 4130 and QQ-A-2118 standards.
- Aviation Certification Support: Providing AS9100D certification, PPAP documents, and material traceability reports (storage period 15 years), meeting airworthiness certification requirements such as FAA and EASA.
2. Process Control: Second-Level Data Collection
- IoT Smart Production Line: Collect 50+ parameters (injection pressure, mold temperature, vacuum degree) per cycle, data uploaded to MES system, automatic shutdown for calibration when parameter fluctuation exceeds ±1%.
- First Article Three-Inspection System: First article must pass CMM measurement (200+ test points, Cpk≥1.67), metallographic analysis (grain size ≥Grade 7), and mechanical testing (tensile strength fluctuation ≤2%), with mold traceability activated for any non-compliance.
3. Finished Product Inspection: Aviation-Grade Standard Coverage
Inspection Item
|
Inspection Method
|
Aviation-Grade Standard
|
Compliance Rate
|
Dimensional Accuracy
|
Coordinate Measuring Machine
|
Key dimensions ±0.015mm, geometric tolerance ±0.02mm
|
100%
|
Internal Defects
|
CT Scan + Ultrasonic Testing
|
0 tolerance for defects ≥0.2mm
|
100%
|
Mechanical Properties
|
Electronic Universal Testing Machine
|
Tensile strength ≥98% of standard value, elongation ≥8%
|
99.8%
|
Fatigue Life
|
Vibration Fatigue Test Bench
|
Simulated flight load cycles ≥100,000 without cracks
|
100%
|
6. Full-Cycle Custom Service: Matching the Extreme Needs of Aviation Industry
1. Collaborative R&D: In-Depth Integration from Design to Forming
- Early Design Involvement: Participate in preliminary aviation component design, providing DFM suggestions (e.g., demolding draft ≥1.5°, wall thickness difference ≤2:1), reducing post-mold modification risk by 90% and R&D cycle by 20%.
- Custom Material Development: Jointly develop high-temperature resistant aluminum alloy (added 1.2%Cu+0.5%Mg) for new aero-engines, increasing tensile strength by 25% at 350℃, applied to a certain turbofan engine bracket.
2. Agile Delivery: Aviation-Grade Project Management
- Rapid Prototyping: Using aluminum simple molds (life 500 shots), deliver first samples in 7 days, supporting rapid aviation component verification (traditional cycle 15 days).
- Mass Production: Intelligent scheduling system prioritizes aviation orders, with a dedicated mold library (20 sets of universal mold bases in stock), emergency orders initiated within 48 hours, delivery cycle 30% shorter than industry average.
3. After-Sales Guarantee: Full Life Cycle Service
- On-Site Technical Support: Provide on-site process debugging for aviation customers (e.g., heat treatment deformation correction for landing gear brackets), increasing yield from 85% to 98%.
- Long-Term Quality Tracking: Establish exclusive files for aviation components, regular 回访 (quarterly), assisting customers with 37 design optimizations, reducing maintenance costs by 18%.