In the era of automotive transformation towards efficiency, lightweighting, and Intelligentization,the engine block stands as the core of powertrain performance. Custom CNC engine block services leverage material innovation, process breakthroughs, and digital technologies to deliver end-to-end solutions, reshaping the boundaries of engine performance for racing, new energy vehicles, and special equipment.
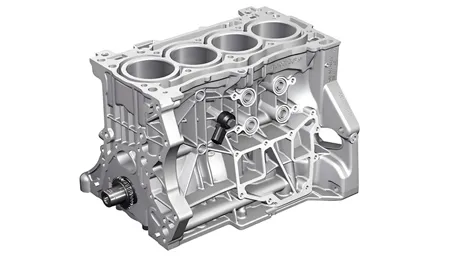
Grade |
Density (g/cm³) |
Compressive Strength (MPa) |
Thermal Expansion (×10⁻⁶/℃) |
Applications |
Machining Parameters |
HT250 |
7.2 |
250 |
11 |
Conventional Engines |
Rough milling Vc=120m/min, CBN finishing |
GGG50 |
7.1 |
500 |
10 |
Heavy-Duty Vehicles |
Deep hole drilling f=0.15mm/r, Ra≤1.6μm |
Technical Breakthroughs:
- Laser surface quenching on GGG50 increases hardness to HV550, extending fatigue life by 30%
- MQL application on HT250 improves tool life by 40%, achieving 2,000 holes per insert
Grade |
Density (g/cm³) |
Thermal Conductivity (W/(m·K)) |
Hardness (HB) |
Weight Reduction |
Machining Strategies |
A356 |
2.7 |
150 |
90 |
40% vs cast iron |
High-speed milling Vc=250m/min |
A380 |
2.7 |
100 |
100 |
Thin-wall |
Vacuum clamping deformation ≤0.02mm |
Process Innovations:
- Aluminum bore rolling reduces Ra from 0.8μm to 0.4μm, cutting friction by 20%
- Five-axis water jacket machining achieves ±0.05mm precision at 2mm wall thickness
Type |
Density (g/cm³) |
Tensile Strength (MPa) |
Machining Technology |
Applications |
CFRP-Al |
2.4 |
2,000 |
Ultrasonic-assisted milling |
Lightweight racing |
Titanium Alloy |
4.5 |
900 |
High-pressure coolant (10MPa) |
Extreme environments |
Cutting-Edge Applications:
- CFRP-Al blocks reduce weight by 60% while increasing modal frequency by 25%
- Laser peening on titanium extends fatigue life from 500,000 to 800,000 cycles
Technology:
Simultaneous X/Y/Z linear and A/C rotational axes enable complex surface machining with Heidenhain iTNC 640 control, achieving ±0.002mm surface accuracy.
Key Parameters:
- DMG MORI CTX gamma 2000 TC Machine
- Spindle Power: 42kW (continuous)
- Torque: 300N·m (40%ED)
- Rapid Traverse: 60m/min
Process Advantages:
- Bore Precision:
- CoroBore 860 tools achieve:
- Cast iron: Vc=250m/min, f=0.08mm/r, cylindricity ≤0.005mm
- Aluminum: Vc=300m/min, f=0.1mm/r, cylindricity ≤0.01mm
- Crankshaft Bore Alignment:
- Centering boring with in-spindle probing ensures ≤0.015mm coaxiality
- 8-station boring reduces cycle time by 40%
Case Data:
Aluminum block machining reduced setup times by 3x, cutting cycle time from 12 to 7 hours with 99.7% dimensional accuracy.
Architecture:
- Kistler 9257B force sensors + Siemens Sinumerik ONE AI algorithms dynamically adjust feed (±15%) and speed (±10%).
Core Functions:
- Tool Wear Compensation:
- CNN-based prediction achieves 92% accuracy, extending tool life by 35%
- Thermal Deformation Compensation:
- Infrared monitoring compensates 0.01mm per 10℃ temperature rise
Performance:
Titanium alloy machining reduced force fluctuations to ±8%, lowering scrap rate from 1.2% to 0.3% and costs by 22%.
Technology:
20-40kHz vibration (5-15μm amplitude) reduces cutting forces and temperatures.
Key Parameters:
- Mitsubishi U600-L ultrasonic spindle
- CFRP machining: Vc=80m/min, f=0.05mm/z
- Titanium deep hole: 1:50 depth-to-diameter ratio
Advantages:
- Composite Machining:
- Delamination factor reduced to 0.8 (vs 1.2 conventionally)
- Surface finish improved to Ra 0.8μm
- Titanium Tool Life:
- Increased from 30 to 80 parts per tool
Test Data:
CFRP-Al hybrid block machining reduced temperatures from 800℃ to 500℃, improving efficiency by 60%.
Process |
Principle |
Applications |
Parameters |
Laser Cladding |
0.1-2mm ceramic coating |
Bore wear resistance |
2.5kW power, 10mm/s scan |
Laser Quenching |
0.3-1.5mm hardened layer |
Cast iron surface hardening |
3mm spot, 20Hz frequency |
Laser Peening |
-1000MPa compressive stress |
Fatigue life enhancement |
5J/cm² energy, 10ns pulse |
Performance Comparison:
Treatment |
Friction Coefficient |
Wear Rate (mg/km) |
Life (Hours) |
Conventional |
0.12 |
2.5 |
2,000 |
Laser Cladding |
0.08 |
0.8 |
5,000 |
- Technical Input:
- Customer-provided engine parameters + reverse engineering (±0.02mm scanning)
- Material Selection:
- DEFORM simulation + full lifecycle cost analysis
- CAD Modeling:
- CATIA V5 surfaces with G0 continuity + modular sensor integration
- CAE Validation:
- ANSYS thermal flow (5-8m/s coolant velocity) + modal analysis (±10% frequency margin)
- Rapid Prototyping:
- SLM titanium (99.9% density) + sand-cast aluminum (±0.1mm tolerance, 72-hour delivery)
- Testing:
- Hydrostatic test (12MPa/30min) + 100-hour durability test (<0.3% failure)
- Process Parameters:
- Aluminum finishing: Vc=300m/min, f=0.08mm/z
- Cast iron honing: 0.03-0.05mm stock removal
- Quality Control:
- CMM inspection (crank bore coaxiality ≤0.015mm) + penetrant testing (Level 2 sensitivity)
- Modular Delivery:
- Raw casting (75% material utilization) to fully finished assemblies
- Aftersales Service:
- 2-hour remote diagnostics + annual performance upgrades
- Material: Ti-6Al-4V
- Technology:
- Five-axis bore machining (0.003mm cylindricity)
- Laser clad tungsten carbide (0.2mm thickness)
- Performance:
- 15,000rpm, 1.2kW/cm³ power density
- 55% weight reduction, 500-hour lifespan
- Design: Magnesium-steel explosive welding
- Specifications:
- 60% reduced hydrogen embrittlement, 150W/(m·K) thermal conductivity
- 65% efficiency, 850km range
Q1: What is the minimum order quantity?
A: 50 units with shared tooling, offering 20% cost savings over traditional methods.
Q2: How is complex water jacket quality ensured?
A: Five-axis helical milling achieves Ra≤1.6μm and <2% flow rate deviation.
Q3: What are new energy block requirements?
A: Integrated battery thermal management with 80L/min flow and 12MPa pressure resistance.
Q4: What is composite block lead time?
A: 72-hour prototype delivery and 8-week production with 40% efficiency gains.
Whether for lightweight racing blocks, hybrid integrations, or specialized explosion-proof designs, our services deliver micron-level precision and lifetime support.
Click below for a free technical consultation and quote!
- Technical Edge: German five-axis machines + ultrasonic systems for 1:50 deep hole titanium machining
- Service Promise: 72-hour prototypes, 100% in-process inspection, and lifetime maintenance
- Industry Leadership: Proven solutions for racing, EVs, marine, and industrial applications
Let’s redefine engine performance together with cutting-edge manufacturing!