In the maritime industry, stainless steel parts are critical components for ensuring vessel safety, reliability, and longevity. From ship engines to offshore structures, the precision, corrosion resistance, and structural integrity of these parts directly impact operational efficiency. CNC (Computer Numerical Control) machining has emerged as the gold standard for crafting high-quality marine stainless steel parts, offering unmatched accuracy and material compatibility. This article explores the technical advantages, material selection, manufacturing processes, quality control, and applications of custom CNC marine stainless steel parts.
Recommended Reading
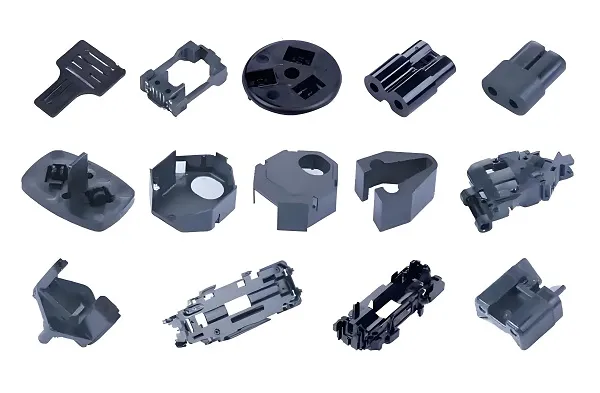
Custom Polycarbonate Injection Molded Parts
Polycarbonate (PC) is a thermoplastic engineering plastic with high strength, high transparency, high temperature and impact resistance. Its excellent physical properties and weather resistance make Polycarbonate injection molded parts widely used in…
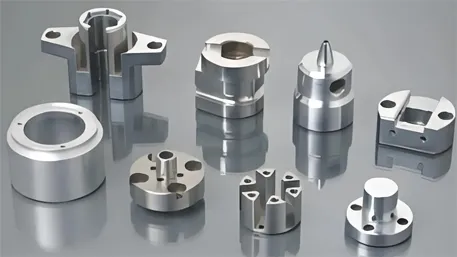
Unleashing Precision: The Power of CNC Machining and Manufacturing
Introduction In the dynamic realm of modern manufacturing, CNC machining and manufacturing have emerged as cornerstones, revolutionizing the way products are designed, prototyped, and produced. From the sleek components of high –…
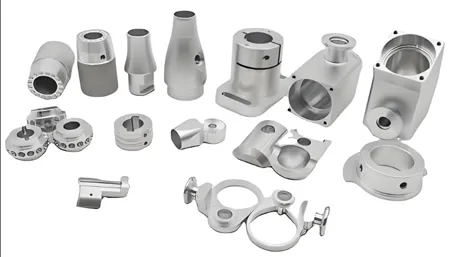
Global Landscape and Technological Innovation in the CNC Industry
As the global manufacturing industry transforms towards digitalization and intelligence, the Computer Numerical Control (CNC) industry is facing unprecedented opportunities and challenges. Based on recent domestic and international news reports…
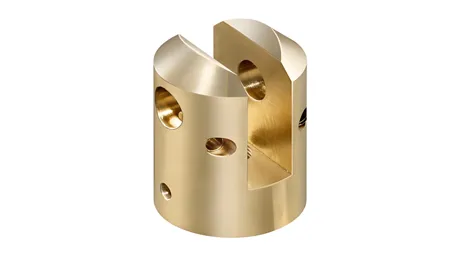
Custom CNC Brass Milling Parts Service: High – Precision Manufacturing Solution
In modern manufacturing, brass, with its excellent electrical conductivity, thermal conductivity, and corrosion resistance, has become an important material in fields such as electronics, decoration, and valves. The custom CNC milling parts…
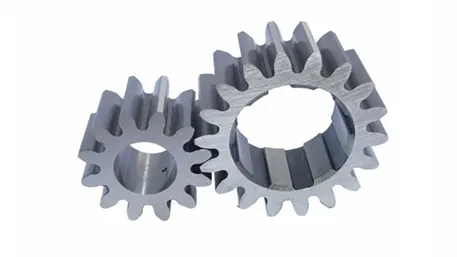
Custom CNC Variable Speed Pump Gears
I. Customization Technology System: Deep Reconstruction from Parameters to Materials The customization service for variable speed pump gears centers on multi-dimensional parameter reconstruction, covering geometric design, material selection, and process optimization….
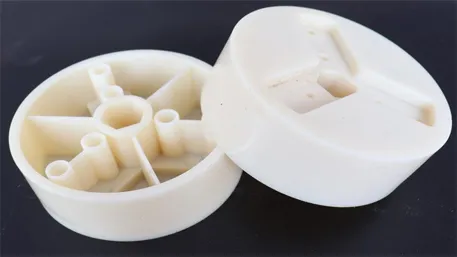
Custom ABS Plastic Parts
In industrial manufacturing and consumer sectors, ABS plastic stands out as a premier material for customized parts due to its excellent comprehensive properties and processing flexibility. This article systematically explores…