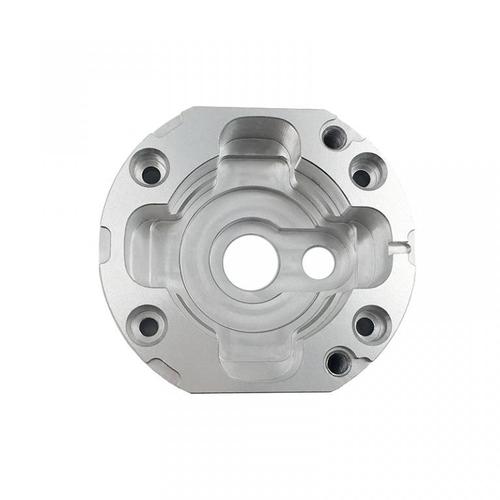
Core Processing Technologies: Engineering for Complex Shapes
1. Multi-Axis CNC Machining
- 5-axis simultaneous machining: Handles 3D curved surfaces and undercuts (e.g., aerospace engine brackets with 15° tilted holes) in one setup, reducing alignment errors by 90%. A medical device frame with 8 irregularly placed mounting points achieved ±0.005mm position tolerance.
- 3+2 axis machining: Optimizes production of semi-complex parts (e.g., automation robot arms) by fixing multi-angle features, cutting cycle time by 40% vs. 3-axis methods. A 300mm-long aluminum robotic arm with 6 asymmetric joints maintained ±0.01mm dimensional stability.
- High-speed CNC milling: 30,000 RPM spindles machine thin-walled Special-Shaped features (0.5mm thickness) on titanium parts without deformation, critical for lightweight aerospace components.
2. 3D Scanning & Reverse Engineering
- Precision digitization: Artec Micro 3D scanners (0.005mm accuracy) capture physical samples of legacy parts, creating 3D models for CNC replication. A 1980s industrial valve body (no CAD files) was reverse-engineered with 99.8% geometric fidelity.
- Design optimization: Engineers overlay scanned data with client requirements, adjusting wall thickness and fillets to enhance structural strength—e.g., a curved automation bracket was redesigned to withstand 500N lateral force (30% higher than original).
3. EDM & Wire Cutting for Intricate Details
- Sinker EDM: Creates blind holes, slots, and cavities in hardened steel (up to 60 HRC) with ±0.002mm accuracy—ideal for mold inserts and precision jigs. A 50mm-diameter die-casting mold cavity with 0.1mm micro-grooves achieved Ra 0.05μm surface finish.
- Wire EDM cutting: Produces complex 2D profiles (e.g., irregular gears, decorative screens) in metal/plastic with ±0.003mm tolerance. A stainless steel medical instrument guard with 0.5mm-wide curved slots maintained burr-free edges.
4. Quality Testing for Complex Geometry
- 3D dimensional inspection: CMMs with 5-axis probing systems verify 1000+ data points on irregular parts, ensuring all features (holes, curves, slots) align with CAD models (deviation ≤0.01mm).
- Structural analysis: FEA software simulates load distribution on asymmetric parts (e.g., cantilever brackets), ensuring they withstand 120% of rated load without deformation.
- Coordinate measuring: Laser trackers validate large-scale Special-Shaped parts (1m+ length) for straightness (≤0.05mm/m) and parallelism, critical for automation assembly lines.
Material Expertise: Matching Materials to Special-Shaped Part Requirements
Material
|
Key Properties
|
Application
|
Advantages
|
Aluminum Alloy (6061, 7075)
|
Easy machining, lightweight, 310MPa tensile strength
|
Automation brackets, consumer electronics enclosures
|
40% lighter than steel; ideal for 5-axis curved surface machining.
|
Stainless Steel (304, 316)
|
Corrosion resistance, 515MPa tensile strength
|
Medical instrument parts, marine hardware
|
Withstands 1,000+ hours salt spray; suitable for hygienic environments.
|
Titanium Alloy (Ti-6Al-4V)
|
High strength-to-weight ratio, 895MPa tensile strength
|
Aerospace components, high-stress brackets
|
45% lighter than steel; maintains strength at 300℃.
|
PEEK (Engineering Plastic)
|
Heat resistance (260℃), chemical resistance
|
Medical device components, high-temperature insulators
|
Machines into complex shapes with low tool wear; biocompatible (ISO 10993).
|
CNC Special-Shaped Parts Machining Technologies
- 5-axis simultaneous machining centers: Enable continuous cutting of 3D curved surfaces (e.g., turbine blade prototypes) with ±0.005mm contour accuracy, eliminating the need for multiple setups.
- Adaptive machining systems: Sensors adjust cutting parameters in real-time when machining uneven material blanks (e.g., castings), ensuring consistent dimensional accuracy across 10,000+ parts.
- Robotic loading cells: Automate handling of irregularly shaped parts (e.g., asymmetric manifolds), reducing human error and increasing production efficiency by 35%.
Custom CNC Special-Shaped Parts Manufacturing Process
- Design & DFM: Engineers analyze client 3D models (STEP/IGS) to identify machining challenges—e.g., adding 0.2mm fillets to sharp corners of a medical bracket to prevent tool breakage.
- 3D scanning (if applicable): For legacy parts or physical samples, 3D scanning creates digital models for CNC programming, ensuring replication accuracy (±0.01mm).
- CNC programming: CAM software generates toolpaths for 5-axis machining, optimizing cutting order to minimize vibration on thin-walled features.
- Multi-axis machining: 5-axis mills shape complex contours; EDM/wire cutting adds precision details (micro-holes, slots); high-speed spindles refine surfaces (Ra 0.8μm).
- Surface treatment: Anodizing, powder coating, or passivation applied per environment (e.g., 316 parts with electropolishing for medical use).
- Quality validation: CMM inspection, 3D model overlay analysis, and functional testing (e.g., load testing for brackets) ensure compliance with specs.
Custom CNC Special-Shaped Parts Application Fields
- Automation & robotics: 5-axis machined aluminum robotic arms with curved joints (6061-T6) for flexible manufacturing lines.
- Medical equipment: Titanium alloy surgical instrument holders with irregularly placed clamps (biocompatible, ISO 13485 compliant).
- Aerospace: 7075 aluminum fuel line brackets with multi-angle bends (withstand 100,000+ pressure cycles at 200℃).
- Energy industry: 316 stainless steel Special-Shaped manifolds for solar panel tracking systems (resistant to desert sand and corrosion).
- Consumer electronics: PEEK Special-Shaped insulators for 5G base stations (heat resistance up to 200℃, low dielectric constant).
Customization Capabilities: From Prototype to Production
- Rapid prototyping: 1-100 units via 5-axis machining, with prototypes delivered in 3-5 days (e.g., a new energy vehicle battery bracket prototype for design validation).
- Low-volume production: 100-5,000 units for specialized equipment (e.g., custom automation fixtures for electronics assembly lines).
- High-volume scalability: 5,000-30,000 units/month with dedicated tooling and automated lines (e.g., 10,000 aluminum camera brackets for security systems).
Common Processing Questions
- Q: How to ensure 0.01mm accuracy on a 300mm-long curved bracket?
- Q: What’s the maximum size of Special-Shaped parts you can machine?
- Q: Can you machine parts with both metal and plastic components?
- Q: What’s the lead time for 500 custom titanium Special-Shaped parts (100mm size)?
Why Choose Goldcattle?
- Special-shaped machining expertise: 26 years of experience in 5-axis machining, with 200+ custom Special-Shaped part designs validated by clients in high-precision sectors.
- Quality assurance: 100% CMM inspection and 3D model overlay analysis; full traceability from raw material to finished part, meeting ISO 9001 and medical ISO 13485 standards.
- Technical problem-solving: In-house engineers collaborate with clients to overcome machining challenges (e.g., thin-walled stability, complex cavity cooling).
- Global compliance: Parts meet FDA, RoHS, and aerospace standards, suitable for export to EU, US, and Asian markets.