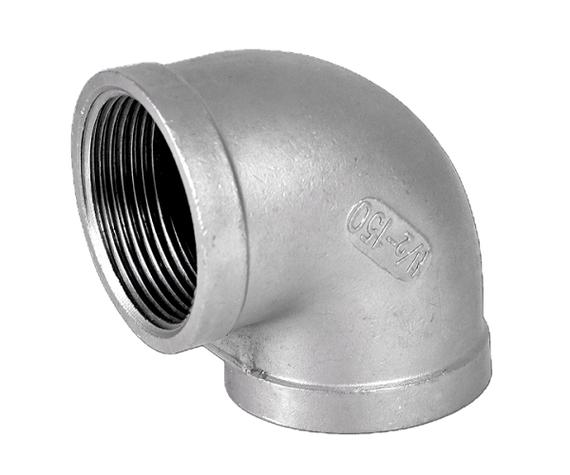
Core Processing Technologies: Engineering for Leak-Proof Performance
1. Precision Thread Machining
- CNC thread turning: Produces NPT, BSP, metric, and custom threads with ±0.005mm pitch tolerance and 6g/6H fit class. A 2-inch NPT steel elbow achieved 100% thread engagement with no cross-threading, maintaining seal integrity at 300bar pressure.
- Thread milling: Creates internal/external threads on thick-walled pipes (≥10mm) with complex shapes (e.g., tees with 3 threaded ports), ensuring uniform thread depth (±0.01mm) across all ports. A 3-way stainless steel tee for chemical pipelines maintained ±0.008mm thread runout.
- Roll threading: Strengthens threads on thin-walled pipes (2-5mm thickness) by cold working, increasing tensile strength by 20% vs. cut threads. A 1-inch aluminum threaded pipe for HVAC systems withstood 10,000+ assembly cycles without thread stripping.
2. Surface Treatment & Corrosion Resistance
- Electroless nickel plating: Applied to carbon steel fittings, providing 500+ hours salt spray resistance and a smooth (Ra 0.2μm) thread surface that reduces galling during assembly.
- Passivation: For stainless steel fittings (304, 316), removes free iron from surfaces to enhance corrosion resistance—316 fittings passed 1,000-hour salt spray testing, suitable for marine and coastal applications.
- PTFE coating: Applied to thread surfaces of high-pressure fittings, reducing friction by 30% and enabling leak-proof sealing at 1000bar without thread sealant.
3. High-Pressure Testing & Quality Validation
- Hydrostatic pressure testing: 100% of fittings undergo 1.5x working pressure tests (e.g., 450bar for 300bar-rated fittings) for 30 minutes with zero leakage, meeting ASME B31.3 standards.
- Thread gaging: Uses master thread plugs/ring gages (calibrated to ISO 1502) to verify thread size, pitch, and flank angle, ensuring 6g/6H fit class compliance.
- Surface finish inspection: Optical comparators check thread flank roughness (Ra ≤0.8μm) to prevent fluid seepage—critical for toxic or high-purity fluid applications.
4. CNC Turning for Pipe Geometry
- Multi-axis CNC turning: Machines complex pipe shapes (e.g., elbows with 45°/90° angles) with ±0.01mm angular tolerance, ensuring aligned threads (≤0.02mm offset) for proper pipe assembly. A 90° stainless steel elbow for oil pipelines maintained 0.01mm alignment between inlet/outlet threads.
- CNC boring: Creates precise internal diameters (±0.005mm) in seamless pipes, ensuring uniform flow velocity (±5%) and reducing pressure drop in high-flow systems. A 6-inch aluminum pipe for water treatment achieved 0.008mm ID tolerance, minimizing turbulence.
Material Expertise: Matching Metals to Fluid Environments
Material
|
Key Properties
|
Application
|
Advantages
|
Carbon Steel (A105)
|
High strength (600MPa), cost-effective
|
Oil & gas pipelines, high-pressure hydraulic systems
|
Withstands 1000bar pressure; ideal for non-corrosive fluids (water, oil).
|
Stainless Steel (304, 316)
|
Corrosion resistance, 515MPa tensile strength
|
Chemical processing, food-grade plumbing
|
304: 500+ hours salt spray; 316: 1,000+ hours (resists chloride solutions).
|
Aluminum Alloy (6061-T6)
|
Lightweight, 310MPa tensile strength
|
HVAC, compressed air systems
|
30% lighter than steel; easy to machine; suitable for low-pressure (≤100bar) applications.
|
Titanium Alloy (Ti-6Al-4V)
|
Extreme corrosion resistance, 895MPa strength
|
Offshore oil, desalination plants
|
Withstands seawater and acids; 45% lighter than steel.
|
CNC Threaded Pipe Fittings Machining Technologies
- CNC multi-spindle turning centers: Produce small threaded fittings (½-2 inches) with 4-6 spindles, achieving 50,000+ units/day with consistent thread quality (±0.005mm pitch).
- Thread grinding machines: Create precision threads (class 4g/4H) on high-pressure fittings, ensuring Ra 0.05μm surface finish for gas-tight sealing in semiconductor vacuum systems.
- Automated inspection cells: Vision systems check thread dimensions (pitch, major diameter) and surface defects at 100 parts/min, maintaining 99.98% defect-free rate.
Custom CNC Threaded Pipe Fittings Manufacturing Process
- Design & DFM: Engineers analyze client drawings (STEP/IGS) to optimize thread geometry—e.g., adding 0.5mm chamfers to thread starts to prevent cross-threading during assembly.
- Material selection: Choose 316 stainless for corrosive fluids, carbon steel for high pressure, or titanium for offshore applications based on client specs.
- CNC machining: Turning creates pipe OD/ID; threading (turning/milling/rolling) forms precise threads; milling adds ports or flanges for multi-way fittings.
- Surface treatment: Plating, passivation, or coating applied per corrosion requirements—e.g., electroless nickel for carbon steel in humid environments.
- Quality validation: Hydrostatic testing, thread gaging, and salt spray trials ensure compliance with ASME B1.20.1 and client pressure/leak standards.
Custom CNC Threaded Pipe Fittings Application Fields
- Oil & gas industry: High-pressure carbon steel NPT fittings (2-12 inches) for wellhead pipelines, rated to 1000bar and -40℃ to 120℃.
- Chemical processing: 316 stainless steel BSP fittings with PTFE coating, resistant to acids and solvents (pH 1-14) in reactor systems.
- Plumbing & HVAC: 6061 aluminum metric threaded elbows and tees, lightweight and corrosion-resistant for potable water and air conditioning.
- Semiconductor manufacturing: Titanium fittings with ultra-precise threads (class 4g), ensuring vacuum-tight sealing (≤10^-8 Pa) in gas delivery systems.
- Marine engineering: Duplex stainless steel threaded pipes, withstanding seawater corrosion and 500bar pressure in offshore rigs.
Customization Capabilities: From Prototype to Production
- Thread customization: Produce NPT, BSP, metric (M), UN, and custom threads (e.g., 11 TPI special for legacy equipment) with 6g/6H to 4g/4H fit classes.
- Special shapes: 3-way tees, 45° elbows, reducers (e.g., 3-inch to 2-inch), and flanged-threaded combinations with precise port alignment (±0.01mm).
- Production scale: 10-100 prototypes (3-5 days) via CNC machining; 10,000-50,000+ units/month with multi-spindle automation (e.g., 30,000 1-inch stainless tees for plumbing suppliers).
Common Processing Questions
- Q: How to ensure thread seal in high-vibration environments (e.g., pump pipelines)?
- Q: What’s the lead time for 1,000 custom 3-inch NPT carbon steel elbows?
- Q: Can fittings withstand 500℃ high-temperature fluids (e.g., steam pipelines)?
- Q: How to prevent galling in stainless steel thread assembly?
Why Choose Goldcattle?
- Thread expertise: 26 years in precision threading, with 200+ fittings designs meeting ASME, ISO, and API standards for pressure and thread quality.
- Quality assurance: 100% hydrostatic testing, thread gaging, and material certification (3.1B); full traceability from raw material to delivery.
- Cost efficiency: Multi-spindle automation reduces production costs by 20% for high-volume orders; design optimization (e.g., integrated flanges) cuts assembly time.
- Global compliance: Fittings meet NORSOK M-630 (oil & gas), FDA 21 CFR 177.2600 (food contact), and REACH (chemicals), suitable for global projects.