In modern manufacturing, turning parts, as the basic components of mechanical systems, their precision and performance directly affect the stability and efficiency of equipment. With the development of industrial demands towards precision and personalization, CNC (Computer Numerical Control) turning technology, with its excellent processing capabilities and automation advantages, has become the core support for customizing high – precision turning parts. This article will systematically analyze the technical logic and engineering value of custom CNC turning parts from dimensions such as technical advantages, materials engineering, processing techniques, quality control, and industry applications.
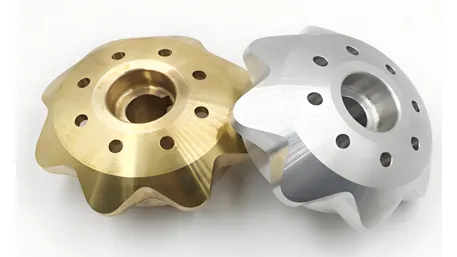
CNC turning provides three core technical supports for turning part processing through digital programming and servo – control systems:
The positioning accuracy of CNC lathes can reach ±0.002mm, the repeat positioning accuracy is ±0.005mm, and the surface roughness Ra≤0.4μm. For example, when processing precision shaft – type parts, the roundness error of the journal can be controlled within ±0.001mm, ensuring dynamic balance during high – speed rotation and reducing mechanical wear.
CNC lathes equipped with power turrets can achieve multi – process composite machining such as turning, milling, and drilling, completing special – shaped structures that are difficult to achieve with traditional processes. For example, when processing eccentric shafts, multi – stepped shafts, and complex parts with radial holes, all processing can be completed in one clamping, with a position accuracy of ±0.01mm.
CNC turning is compatible with various materials such as stainless steels (304, 316L), aluminum alloys (6061, 7075), titanium alloys (TC4), copper alloys (H62), and engineering plastics (PEEK). According to the characteristics of different materials, cutting parameters can be optimized: when processing aluminum alloy, using high – speed cutting (HSC) technology with a rotational speed of 10000r/min and a feed rate of 0.3mm/r, the efficiency can be increased by 50%; when processing titanium alloy, applying high – pressure internal – cooling tools can extend the tool life by 3 times.
Material selection is a crucial step in customizing turning parts and needs to be scientifically matched according to working – condition requirements:
- High – load Scenarios: Select 42CrMo alloy steel (tensile strength ≥ 1080MPa, yield strength ≥ 930MPa), which is suitable for heavy – load components such as drive shafts and gear shafts.
- Lightweight Requirements: Use 6061 aluminum alloy (density 2.7g/cm³, tensile strength 290MPa) or magnesium alloy, reducing the weight by 40% while ensuring structural strength.
- Corrosive Environments: 316L stainless steel (PREN value ≥ 25) is used for parts of chemical equipment, which can withstand the corrosion of media such as hydrochloric acid and brine, with a service life of more than 15 years.
- High – temperature Working Conditions: Select Inconel 718 superalloy, which can maintain high strength (tensile strength ≥ 1290MPa) at 650℃, suitable for parts of aircraft engines.
- Economical Solutions: Q235 carbon steel after surface quenching treatment, with a hardness of HRC40 – 45, and the cost is 60% lower than that of alloy steel, is suitable for ordinary mechanical structural parts.
- High – end Applications: Although the cost of titanium alloy (TC4) parts is relatively high, lightweight design (density 4.5g/cm³) can reduce the weight of components by 40% while maintaining a tensile strength of ≥ 895MPa, which is suitable for aerospace precision parts.
In response to the diverse needs of turning parts, CNC turning processes achieve a double breakthrough in efficiency and quality through the following technological innovations:
- When processing high – strength steel, use CBN tools in combination with high – feed milling (HFC) technology. The cutting speed can reach 300m/min, and the material removal rate is increased by 60%.
- When processing stainless steel, apply TiAlN – coated tools and high – pressure internal – cooling technology. The cutting temperature is reduced by 30%, and the tool life is extended by 2 times.
Through the power turret, turning, milling, drilling and other multi – processes are integrated. For example, when processing a drive shaft with a keyway, outer – circle turning, keyway milling and radial hole processing can be completed in one clamping. The efficiency is increased by 70%, and the position accuracy reaches ±0.01mm.
Introduce AI algorithms to monitor parameters such as cutting force and temperature in real – time, and dynamically adjust the feed rate and rotational speed. The processing efficiency is increased by more than 20%, and tool wear is reduced at the same time.
To ensure that products meet industry standards and customer requirements, custom CNC turning parts need to go through a strict quality control process:
- Use a coordinate measuring machine (CMM) for full – size scanning. The tolerance of key dimensions (such as the diameter of shaft – type parts) is controlled within ±0.003mm.
- Geometric tolerance detection: roundness error ≤ 0.002mm, coaxiality ≤ 0.005mm, ensuring the assembly accuracy of parts.
- Use spectral analysis to confirm the material composition. For example, the chromium content of 42CrMo alloy steel should be ≥ 0.9 – 1.2%, and the molybdenum content should be ≥ 0.15 – 0.25%.
- Conduct tensile tests, impact tests, and hardness tests to ensure that the mechanical properties meet standards such as GB/T 3077. For example, the yield strength of 42CrMo should be ≥ 930MPa.
- Use a roughness tester to detect the surface Ra value. Precision parts need to reach Ra≤0.2μm.
- Nondestructive testing: Use X – ray or ultrasonic testing to detect internal defects, ensuring the reliability of safety – critical parts (such as parts of pressure vessels).
- Custom – made 42CrMo alloy steel crankshafts are turned by CNC and quenched. The hardness of the journal is HRC50 – 55, and the service life is extended by 3 times, which is suitable for high – speed engines.
- 6061 aluminum alloy wheel hubs are turned by CNC and anodized. The dimensional tolerance is ±0.005mm, and the corrosion resistance is improved, ensuring driving safety.
- TC4 titanium – alloy aerospace bolts are turned by CNC and surface – polished. The tensile strength is ≥ 895MPa, and the weight is reduced by 40%, meeting the lightweight requirements of spacecraft.
- Inconel 718 superalloy turbine shafts are turned by CNC and precision – ground. The surface roughness Ra≤0.4μm, and they can be used for a long – term at 650℃.
- 316L stainless – steel medical implant rods are turned by CNC and electro – polished. The surface roughness Ra≤0.1μm, with excellent biocompatibility and an implant life of more than 15 years.
- PEEK plastic precision screws are formed by CNC turning. The pitch tolerance is ±0.01mm, which is suitable for the transmission systems of medical equipment.
- What level of precision can custom CNC turning parts achieve?
CNC turning can achieve a dimensional tolerance of ±0.002mm, a repeat positioning accuracy of ±0.005mm, and a surface roughness Ra≤0.4μm, meeting the needs of most precision industries.
- How to choose the suitable materials?
It is necessary to choose according to the functions and working conditions of the parts. For example, choose alloy steel for high – load, aluminum alloy for lightweight, stainless steel for corrosion – resistance, and superalloy for high – temperature scenarios.
- How long is the production cycle for custom turning parts?
The production cycle depends on the complexity of the parts, the type of material, and the order quantity. Simple parts usually take 3 – 5 days, and complex parts may take 7 – 15 days. Urgent customization is supported to shorten the delivery time.
- Can CNC turning process parts with complex shapes?
Yes, CNC lathes equipped with power turrets can achieve multi – process composite machining such as turning, milling, and drilling, completing complex structures such as eccentric shafts, multi – stepped shafts, and parts with radial holes.
- What is the cost of custom turning parts?
The cost is affected by materials, processing complexity, accuracy requirements, and batch size. Generally, the cost of small – batch customization is relatively high, but CNC technology can reduce the unit cost by optimizing the process. In the long run, it is more cost – effective than traditional processes.
Inquire now and get a customized solution!
Whether it is the high – wear – resistant crankshafts of automobiles, the lightweight bolts of aerospace, or the precision implant rods of medical equipment, our professional team will rely on the high – precision advantages of CNC turning technology, combined with materials engineering and process innovation, to provide you with a full – process customization service from design, processing to inspection. Click to leave a message, and let us, with a rigorous technical system and reliable quality assurance, customize high – performance and high – precision turning part solutions for your project, helping you achieve technological breakthroughs and industrial upgrades in the field of industrial manufacturing!