In the context of modern manufacturing’s trend toward precision, lightweight design, and integration, custom die casting services have emerged as a core manufacturing support for high-end sectors such as automotive, electronics, and aerospace. Leveraging high precision, consistency, and efficient production, this article presents a professional, data-driven solution for custom die casting, covering technical processes, material systems, quality control, and application scenarios.
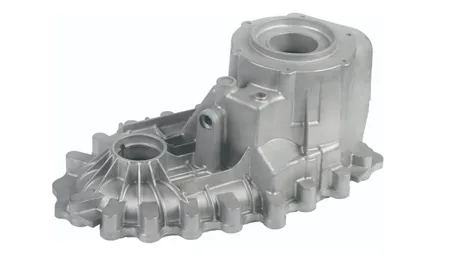
- Pressure System: Utilizing 800–4,500-ton servo die casting machines, injection pressure ranges from 10 to 175 MPa, ensuring molten metal fills molds at high speeds (5–50 m/s). This capability meets the forming requirements for thin-walled parts (minimum wall thickness 0.5mm) and complex structures.
- Temperature Control: Mold temperature control systems achieve ±2℃ accuracy, with molten alloy temperature fluctuations ≤±5℃. Real-time thermocouple monitoring minimizes defects like cold shuts and shrinkage porosity, maintaining a finished product yield stability of over 98%.
- Dimensional Accuracy: Complying with GB/T 6414-1999 Casting Dimension Tolerances and Machining Allowances, standard dimensional tolerances reach CT4–CT6 grades (e.g., ±0.3mm for 100mm dimensions), while precision molds achieve CT3 grade accuracy (±0.15mm).
- Material Selection: H13 (4Cr5MoSiV1) hot-work tool steel is used, with a hardness of 48–52HRC and resistance to thermal fatigue exceeding 500,000 cycles—30% longer lifespan than conventional molds.
- Digital Design: UG/NX and Moldflow are employed for mold flow analysis, optimizing gate positions with an error ≤0.5mm and controlling runner system pressure loss within 15%, reducing material waste and forming defects.
Material Type |
Density (g/cm³) |
Tensile Strength (MPa) |
Thermal Conductivity [W/(m·K)] |
Application Scenarios |
Surface Treatment Compatibility |
Aluminum Alloy (ADC12) |
2.7 |
310–350 |
180 |
Automotive structural parts, electronic radiators |
Anodizing, electrophoresis, powder coating |
Zinc Alloy (ZA27) |
6.6 |
400–430 |
113 |
Precision hardware, toy mechanisms |
Electroplating (Ni/Cr), baking paint |
Magnesium Alloy (AZ91D) |
1.8 |
240–260 |
156 |
3C product casings, aerospace lightweight components |
Chemical conversion coating, micro-arc oxidation |
Copper Alloy (CuZn38Pb2) |
8.5 |
300–350 |
260 |
Conductive connectors, corrosion-resistant valves |
Silver plating, passivation treatment |
- High-Temperature Alloys: Capable of die casting Inconel 718 (service temperature ≤650℃) for short-cycle aerospace engine components, with tensile strength ≥1,220 MPa and fatigue life (σ=450MPa) ≥10⁷ cycles.
- Semi-Solid Metals: Using rheo-die casting technology, primary α-Al grain size is controlled ≤50μm, increasing elongation by 20%—ideal for high-toughness automotive suspension components.
- Material Testing: Direct-reading spectrometers (accuracy 0.01%) analyze alloy composition, while hydrogen-oxygen analyzers control hydrogen content in aluminum melt ≤0.15ml/100g to prevent gas porosity.
- Dimensional Inspection: CMM (Coordinate Measuring Machine, accuracy ±0.005mm) scans full dimensions, with 100% inspection for critical dimensions and AQL=1.0 sampling per GB/T 2828.1 for non-critical dimensions.
- Internal Defect Detection: X-ray flaw detectors (resolution ≤0.2mm) identify shrinkage and inclusions, while ultrasonic thickness gauges (accuracy ±0.01mm) monitor wall thickness uniformity in thin-walled parts.
Quality management systems are certified to IATF 16949:2016. Materials comply with RoHS 2.0 and REACH regulations, and aerospace components can provide NADCAP certification and material traceability reports.
- Case: Custom battery trays for an automaker, produced using a 6,000-ton die casting machine. Single-part dimensions: 1,200mm×800mm×150mm, weight reduced by 35% compared to traditional welded parts, with dimensional deviation ≤±0.5mm.
- Technical Highlights: Integrated vacuum die casting (cavity vacuum degree ≤5kPa) reduces porosity to 0.3%, meeting IP67 waterproof and 800V high-voltage insulation requirements.
- Requirement: High-frequency signal connectors with surface roughness Ra≤0.8μm and conductivity ≥85%IACS.
- Solution: High-conductivity copper alloy (Cu-0.5Zr) is used, with oxygen injection die casting to eliminate internal pores. Subsequent precision milling achieves contact resistance ≤50mΩ and salt spray test (NSS) ≥200 hours without corrosion.
- Requirement Alignment: 24-hour response with a DFM (Design for Manufacturability) report, clarifying mold costs and timelines.
- Mold Development: Standard molds leverage CAD/CAE collaborative design; precision molds optimize gate positions via mold flow analysis (error ≤0.5mm) to shorten development cycles.
- Production Manufacturing: Mass production capacity ranges from 500–1,000 pieces/hour (depending on part size), supporting low-volume trial production (minimum order quantity 500 pieces).
A: Standard aluminum alloy parts have a minimum wall thickness of 0.8mm; zinc alloy parts can achieve 0.5mm. Special structures via mold flow optimization can reach 0.3mm (mold life assessment required).
A: For annual purchases ≥50,000 pieces, mold costs can be prorated into unit costs, with specific policies evaluated based on product complexity.
A: One-stop solutions include anodizing (film thickness 5–25μm), electroplating (nickel layer 10–20μm), and powder coating (film thickness 60–100μm), supporting high-corrosion resistance (salt spray test ≥1,000 hours).
A: Sample production (including mold design) is completed within 7–15 working days after receiving 3D drawings. Rush sampling (for simple structures) is available within 3 days for urgent needs.
Custom die casting is more than just part manufacturing—it’s a systematic engineering process from material selection to process optimization. With 15 years of industry experience, serving over 200 high-end clients and delivering 100,000+ die casting products, we maintain a 98.7% good product rate. Whether for automotive lightweight components, precision electronic structures, or high-reliability aerospace parts, we provide end-to-end technical support from design optimization to mass production.
Click to Leave a Message and share your product requirements (material type, dimension range, performance specifications). Our technical team will provide a preliminary solution and quote, making professional customization accessible.