In the fields of education, healthcare, industrial training, and product design, custom injection – molded simulation parts, with their high degree of authenticity, functional diversity, and cost – effectiveness, have become core tools for simulating real – life scenarios. This article systematically analyzes the technical logic and industry value of custom injection – molded simulation parts from aspects including material selection, process technology, application scenarios, and quality control, providing professional decision – making references for those in need.
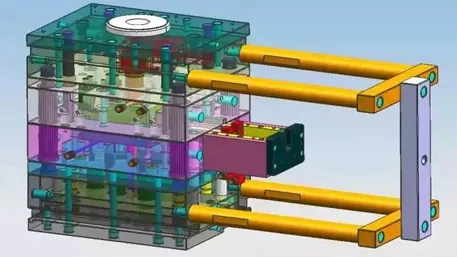
The materials for custom injection – molded simulation parts need to balance physical simulation effects, safety, and processability. The following are the key characteristics and typical applications of commonly used materials:
- Characteristics: Good softness and elasticity (Shore hardness 10 – 80 Shore A), excellent biocompatibility, high – temperature resistance (-50℃ to 200℃), and strong moldability.
- Applications: Medical simulation organs (such as heart and liver models), baby pacifiers, due to their realistic touch and non – toxicity.
- Characteristics: High strength (tensile strength 40 – 50 MPa), surface can be electroplated or painted, impact – resistant, and easy to form complex structures.
- Applications: Simulation models of automotive parts, training aids for industrial equipment, meeting the needs of high durability and visual authenticity.
- Characteristics: Low cost, softness can be adjusted by plasticizers (Shore hardness 50 – 100 Shore A), and chemical – corrosion resistant.
- Applications: Simulation pipeline systems for teaching, children’s water – playing toys, suitable for scenarios sensitive to flexibility and cost.
- Characteristics: High transparency (light transmittance > 90%), impact strength of 60 – 70 kJ/m², and good dimensional stability.
- Applications: Transparent simulation electronic components, optical instrument models, meeting the needs of visual teaching.
- Characteristics: Elongation at break of 500% – 800%, excellent oil and weather resistance, and different hardnesses can be customized (Shore A 60 – D 80).
- Applications: Simulation human skin models, simulated parts of sports protective gear, providing a realistic touch and elastic feedback.
Through precise material selection, custom simulation parts can achieve a high degree of matching between physical properties (such as hardness, transparency) and functional requirements.
- Use simulation software such as Moldflow to optimize the injection molding process, predict melt flow, cooling uniformity, and stress distribution, ensuring the molding accuracy of complex structures (such as the blood vessel patterns of simulation organs), and controlling the warpage deformation within 0.1 mm/m.
- Mold design combines 3D scanning and reverse – engineering technologies to replicate real objects 1:1. The surface roughness of the cavity Ra≤0.4 μm, ensuring the restoration of details.
- Multi – material injection molding (such as 2K injection molding) realizes the combination of hard and soft materials. For example, in a simulation hand model, silicone (soft skin) and ABS (supporting skeleton) are injected to improve functional simulation.
- Surface treatment technologies (such as UV printing, laser engraving) add textures, logos, or anti – counterfeiting patterns to simulation parts, enhancing visual authenticity.
- 3D printing technology is used to make mold prototypes, shortening the development cycle from 4 weeks to 72 hours, suitable for small – batch customization (such as 10 – 100 pieces) of teaching models.
- Micro – injection molding technology enables the production of micro – simulation parts (such as electronic component models), with dimensional tolerances controlled within ±0.01 mm.
- Surgical Training Models: Silicone – injection – molded human organ models simulate the softness and anatomical structure of real tissues, used for minimally invasive surgery training.
- Rehabilitation Aids Simulation: TPU – injection – molded joint models provide mechanical feedback to assist in the design of rehabilitation treatment plans.
- Teaching Demonstration Models: PC or ABS – injection – molded transparent engine models display the internal structure, improving students’ understanding efficiency.
- Vocational Skill Training: PVC – injection – molded simulation parts of pipeline systems are used for practical pipeline connection training for plumbers.
- Prototype Verification Models: Injection – molded simulation parts are used to test product human – machine interaction (such as the grip of a handle), replacing traditional handmade samples and reducing development costs.
- Equipment Operation Simulation: ABS – injection – molded control panel models of industrial equipment are used for new employee operation training, reducing equipment wear.
- Toys and Collectibles: Silicone – injection – molded anime character figurines restore details with high precision, meeting the collection needs of fans.
- Virtual Reality (VR) Accessories: TPU – injection – molded VR handle simulation parts provide a realistic grip, enhancing the immersive experience.
- Medical simulation parts need to pass the ISO 10993 biocompatibility certification to ensure no cytotoxicity (for example, the hemolysis rate of silicone ≤ 5%).
- Children’s toy parts need to comply with standards such as EN71 or GB 6675, and the use of harmful substances such as phthalates is prohibited.
- Physical Property Testing: Measure indicators such as hardness and elastic modulus to ensure consistency with real objects (error ≤ 5%).
- Dimensional Accuracy Detection: A coordinate measuring machine (CMM) verifies key dimensions, with tolerances controlled within ±0.05 mm to ensure assembly simulation.
- High – low – temperature cycle testing (-20℃ to 60℃) verifies material stability, ensuring the performance consistency of simulation parts in different environments.
- Aging resistance testing (QUV accelerated aging for 1000 hours) evaluates problems such as surface fading and cracking, ensuring long – term use effects.
- Injection – molded simulation parts integrated with sensors can feedback data such as pressure and temperature in real – time, used for operation evaluation in medical training or fault simulation of industrial equipment.
- Develop bio – based simulation materials (such as plant – starch – based PLA), which can be 100% biodegradable while ensuring simulation effects, reducing the environmental burden.
- Combine digital twin technology to optimize the design through the virtual model of injection – molded simulation parts, realizing rapid iteration from concept to physical object, shortening the customization cycle by more than 30%.
Q1: How long is the development cycle of custom injection – molded simulation parts?
A: Sampling of simple parts takes about 3 – 5 days, complex mold development takes 2 – 4 weeks, and mass production is adjusted according to the order quantity, with a monthly production capacity of over 50,000 pieces.
Q2: How to ensure that the touch of simulation parts is consistent with real objects?
A: By matching material hardness (such as the Shore hardness of silicone is close to that of human tissues), designing surface textures (such as the unevenness of the skin), and adjusting mechanical properties, a high degree of simulation can be achieved.
Q3: Does small – batch customization support complex structures?
A: Yes. 3D – printed molds and micro – injection molding technology can achieve small – batch (10 – 100 pieces) customization of complex structures, such as the blood vessel network of simulation organs.
Q4: What are the surface treatment options for simulation parts?
A: Common treatments include painting, UV printing, laser engraving, flocking, etc., which can be customized according to needs for textures, colors, or logos to enhance authenticity.
If you need to customize highly – realistic injection – molded parts, please feel free to contact us via online message. Our engineering team will:
- Recommend suitable simulation materials (such as silicone, ABS) according to application scenario requirements;
- Provide a full – process solution from 3D modeling to precision injection molding to ensure the high – reduction and functionality of the parts;
- Strictly follow industry standards and provide third – party test reports to ensure product quality and safety.
Whether it is the precise simulation in medical training or the prototype verification in industrial design, based on material innovation and supported by precision processes, we create customized simulation solutions for you. Click to leave a message and start your professional customization journey!