As a national high-tech enterprise with 15 years of expertise in die casting, GOLDCATTLE Die Casting is committed to “Precision Customization · Uncompromising Quality,” providing zinc alloy die-casting solutions to over 50 global mainstream automotive brands. With an annual production capacity exceeding 8 million pieces, a critical dimension accuracy rate of 99.2%, and salt spray resistance exceeding 1,000 hours without corrosion, we set the benchmark for automotive parts through end-to-end digital control.
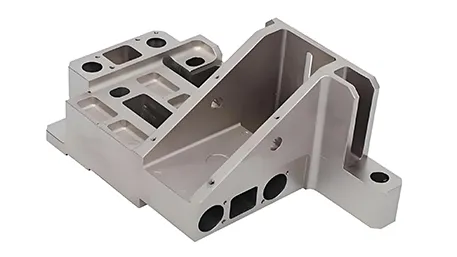
- Why Zinc Alloy Die-Casting Is the Optimal Choice for Automotive Parts
- Five-Dimensional Customization Process: From Blueprint to Finished Product
- Three Core Technologies: Redefining Industry Precision Standards
- Full-Process Quality Management: The Foundation of Defect-Free Delivery
- One-Stop Service System: Value Beyond Manufacturing
- Zinc Alloy Die-Casting FAQs: Answers to Your Key Questions
Zinc alloy stands out for its superior comprehensive performance, making it the top choice for lightweight, high-reliability automotive components:
- Exceptional Mechanical Properties: Tensile strength ≥ 380MPa (20% higher than industry standard 350MPa), yield strength ≥ 270MPa, ideal for load-bearing parts like steering systems and chassis connectors.
- Precision Molding Advantages: Shrinkage rate as low as 0.3%-0.6%, enabling 0.8mm thin-wall parts (dimensional tolerance ±0.03mm) for precise assembly in automotive connectors and sensor housings.
- Superior Corrosion Resistance: After electroless nickel-chrome plating, salt spray test passes 1,000 hours without white rust (NSS standard), 50% better than aluminum alloy counterparts.
- Cost-Effective Balance: Material costs 30% lower than aluminum alloy, mold life up to 800,000 cycles (H13 steel + PVD coating), reducing total lifecycle costs by 25% for customers.
Typical applications: automotive door lock housings, wiper gearboxes, and car charger casings, with 3 million+ defect-free deliveries.
- Dedicated project managers conduct 1:1 consultations, locking core parameters via the Automotive Parts Customization Requirement Form—material (Zamak 3/5), dimensions (CT4 precision grade), and surface treatment (plating/painting).
- Provide DFM (Design for Manufacturability) analysis reports, optimizing draft angles (recommended 2°-3°) and wall thickness uniformity (difference ≤1.5mm), reducing post-mold modification risks by 90%.
- German Zeiss CMM (accuracy ±0.005mm) inspects mold cavities; critical cores formed via slow wire EDM (surface roughness Ra ≤0.2μm).
- Moldflow simulation predicts filling pressure (80-120MPa) and shrinkage risks, designing 3 overflow systems to boost trial mold pass rate to 95%.
- Equipped with 200-800T hot-chamber die-casting machines, controlling injection speed (5-10m/s) with clamping force error ≤1% (800T machine actual pressure ≥792T).
- Collect 20+ parameters per cycle (mold temperature 180±5℃, holding time 3±0.5s), achieving 100% traceability via MES system.
- CNC machining reserves 0.3mm allowance, using Haas machining centers (positioning accuracy ±0.01mm) for assembly holes with H7-grade tolerance.
- Three-step pre-surface treatment (ultrasonic degreasing + pure water rinsing + drying) ensures plating adhesion ≥5N/cm (cross-cut test).
From first-article full-dimension inspection (26 critical dimensions Cpk ≥1.67) to mass production sampling (5 pieces/hour, 1,000 consecutive defect-free pieces for approval), our outgoing standards are 30% stricter than industry norms.
- Innovative conformal cooling channels (3D-printed molds) improve temperature uniformity by 40%, with cavity temperature difference ≤±3℃, solving “zinc pest” caused by local overheating.
- Mold life management system monitors core wear, automatically replacing molds when diameter wear >0.02mm to ensure dimensional fluctuation ≤±0.015mm in continuous production.
- Servo-direct drive injection system (response time ≤1ms) adjusts pressure with ±1% accuracy, achieving 100% filling for 0.8mm thin walls (industry average 85%).
- Pressure build-up time ≤3ms, holding pressure stability ≥98%, reducing internal shrinkage from common 3% to <0.8%.
- Each product embeds a traceability code linked to mold number, casting parameters, and test data (5-year storage), locating defect sources in 10 seconds.
- AI visual inspection (0.02mm resolution) identifies surface defects (>0.1mm burrs/0.2mm² pores) with 99.8% accuracy, Missed detection rate ≤0.01%.
- Strict selection of zinc alloy ingots (impurities Pb+Cd+Hg ≤0.005%), spectral analysis per batch (0.01% accuracy), and nitrogen protection during melting (oxidation slag rate <0.2%).
- Density testing (≥6.6g/cm³) ensures internal compactness ≥98%, exceeding the automotive industry’s 95% standard.
- Thermal cycle test (-40℃~85℃, 500 cycles), dimensional change rate ≤0.05%.
- Vibration test (10-2000Hz, 20g acceleration), 100,000 cycles without cracks, surpassing IATF 16949 requirements.
- Water-based release agents (VOC <5%), tertiary wastewater treatment (COD ≤50mg/L) with 70% recycling rate.
- Full certifications including RoHS, REACH, and IATF 16949 for global market access.
- Mold development in 4-6 weeks (6-8 weeks for complex structures), first sample delivery ≤15 days, mass production lead time 20-30 days (adjustable by order quantity).
- Support low-volume trials (MOQ 500 pieces), bonded warehouse services, and 48-hour emergency response.
- Early-stage material selection advice (e.g., ZA27 alloy for high-wear parts, hardness ≥120HB), mid-stage DFM optimization (average 20% mold cost reduction for customers), and post-stage assembly validation (matching tolerance ±0.02mm).
- Free replacement for non-human defects during warranty, 24-hour complaint response (solution within 48 hours), and quarterly quality inspections (127+ design optimizations for customers to date).
A: MOQ is 500 pieces for standard parts. Mold costs range from $7,000 to $42,000 USD based on complexity, with 50% reimbursement for orders over 50,000 pieces.
A: Standard process: 3 days for requirement confirmation → 7 days for mold design → 25 days for mold machining → 5 days for trial molding → 3 days for production readiness, totaling ~45 days.
A: Yes, including IATF 16949, PPAP, 1,000-hour salt spray test reports, and spectral analysis—fully compliant with OEM entry requirements.
A: Mold life management and parameter solidify technology ensure dimensional fluctuation ≤±0.02mm and material composition deviation <0.1% over 100,000 pieces with the same mold.
Choose GOLDCATTLE Die Casting for Full-Process Quality Assurance
From 0.8mm thin-wall precision parts to complex load-bearing structures, our 15 years of industry expertise deliver end-to-end solutions from material R&D to delivery. Leave a message with your customization requirements today to receive a tailored technical proposal and cost quote—let every die-casting be a testament to quality!
(Message: Please specify application, material requirements, and annual quantity. We’ll respond within 24 hours.)