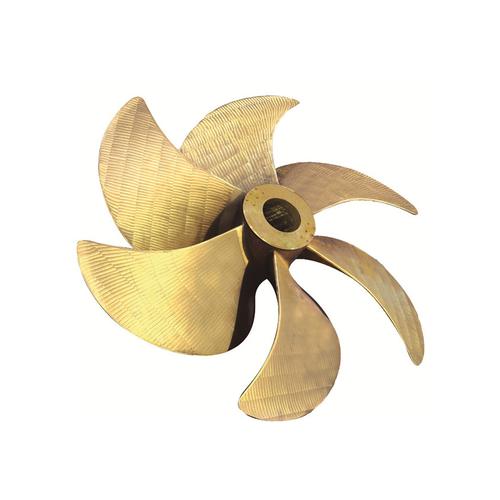
1. Why Custom Marine Propeller Parts
2. Marine Propeller Parts Processing Technologies
- CNC Machining: Uses computer-controlled mills/lathes to shape metal blanks into precise propeller blades. Ideal for high-strength materials like bronze, offering tight tolerances (±0.1mm) for complex geometries.
- Casting (Sand or Investment): Sand casting is cost-effective for large, thick blades (cargo ships), while investment casting produces intricate, thin-walled designs (yachts). Both methods mold molten metal (bronze, nickel-aluminum-bronze) into blade shapes.
- Forging: Compresses heated metal to improve density and strength, suitable for propellers in high-stress applications (military ships, fast ferries). Reduces internal defects, enhancing resistance to fatigue.
- 3D Printing (Additive Manufacturing): Emerging for prototyping or small propellers, using metal powders (titanium, stainless steel) to build complex blade designs with internal cooling channels, useful for research vessels.
3. Marine Propeller Parts Processing Flow
- Design & Simulation: Engineers use hydrodynamic software to model blade performance, testing factors like cavitation, thrust, and efficiency. 3D CAD models refine pitch, chord length, and thickness distribution.
- Material Selection & Preparation: Choosing alloys (bronze, NAB) based on vessel type, then melting/casting or forging into blanks. Forging involves heating metal to 800–1200°C for shaping.
- Rough Shaping: CNC cutting or casting creates the basic blade form, removing excess material while preserving critical dimensions.
- Finishing: CNC grinding polishes blade surfaces to reduce drag; balancing machines ensure even weight distribution to prevent vibration.
- Surface Treatment: Applying anti-corrosion coatings (e.g., epoxy paints, chrome plating) or electrolytic treatments to resist saltwater erosion.
- Quality Testing: Hydrodynamic testing in water tunnels verifies performance; ultrasonic inspection checks for internal cracks. Balancing tests ensure smooth rotation at high speeds.
4. Marine Propeller Parts Materials
- Nickel-Aluminum-Bronze (NAB): Most common for large ships, offering excellent corrosion resistance, strength, and cavitation resistance. Withstands saltwater and high speeds, used in cargo and military vessels.
- Manganese Bronze: Cost-effective for medium-sized ships (fishing boats, ferries). Good machinability and corrosion resistance, though less durable than NAB in extreme conditions.
- Stainless Steel (316): Resists corrosion in brackish or polluted waters, suitable for small boats (yachts, research vessels). Lighter than bronze but pricier.
- Titanium Alloys: Used in high-performance applications (military, racing boats) for their strength-to-weight ratio and corrosion resistance. Expensive but ideal for reducing hull drag.
5. Marine Propeller Parts Applications
- Cargo Ships: Large, slow-turning propellers with wide blades (NAB material) to generate high thrust for heavy loads, prioritizing durability over speed.
- Cruise Ships & Ferries: Medium-sized propellers with optimized pitch for fuel efficiency and reduced noise, often using NAB to resist corrosion in busy coastal waters.
- Military Vessels: Stealth-designed propellers with irregular blade patterns to reduce noise and cavitation, made from forged NAB for combat durability.
- Fishing Boats: Compact, robust propellers (manganese bronze) that withstand debris (nets, rocks) in shallow fishing grounds.
- Yachts & Recreational Boats: Sleek, lightweight propellers (stainless steel) for speed and maneuverability, with polished surfaces to minimize drag.
6. Marine Propeller Parts Performance Additions
- Cavitation Resistance: Blades are polished to a mirror finish and coated with anti-cavitation paints (e.g., silicone-based) to reduce bubble formation and erosion.
- Corrosion Protection: Electroplating with chromium or applying epoxy coatings creates a barrier against saltwater, extending blade life by 30–50%.
- Balancing: Dynamic balancing ensures even weight distribution, reducing vibration that strains the engine and hull, improving fuel efficiency.
- Blade Twisting Optimization: Custom pitch variation along the blade (more twist at the tip) maximizes thrust across the entire surface, boosting speed and reducing energy waste.
7. Marine Propeller Parts Common Questions
How long do custom propellers last?
With proper maintenance (cleaning, anti-corrosion treatments), NAB propellers last 10–15 years in saltwater; stainless steel for yachts lasts 8–12 years.
Are custom propellers more fuel-efficient?
Yes—optimized blade designs reduce drag and cavitation, improving fuel efficiency by 5–15% compared to standard propellers, offsetting initial costs.
Can parts be repaired if damaged?
Minor damage (scratches, small cracks) can be welded and re-machined. Severe erosion may require blade replacement, but custom designs allow for easy matching of replacement parts.
What’s the lead time for a custom propeller?
Design and prototyping take 4–6 weeks; production (casting + machining) for large propellers (cargo ships) takes 8–12 weeks. Smaller yacht propellers take 6–8 weeks.