As motorcycle enthusiasts know, factory – original parts always seem to lack that certain “oomph” – either their performance can’t keep up with the needs of modification, or their appearance doesn’t match the style of their own bikes. At this point, CNC – customized parts become the top choice for hardcore riders. However, turning a bunch of blueprints into reliable parts that can be screwed onto a motorcycle involves a lot of know – how. Today, we’ll discuss everything from materials, technologies to quality control regarding customized motorcycle CNC parts.
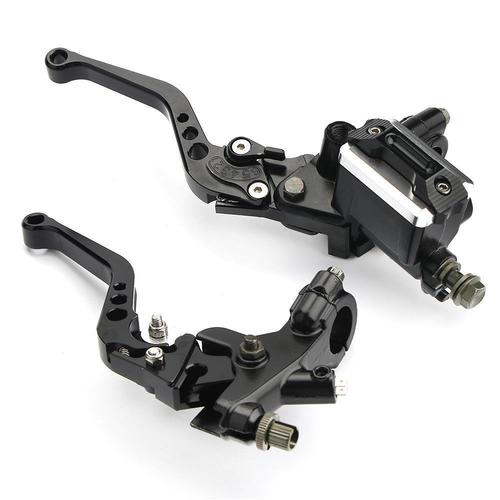
I. Why Choose CNC Customization? These 3 Advantages are Irresistible
Compared with mass – produced universal parts, CNC – customized parts are like “tailor – made” weapons for motorcycles, especially suitable for riders who pursue individuality and performance:
- Precision to the Hair – thin Level: Motorcycle parts require a perfect fit. For example, the clearance between the brake caliper and the disc. A difference of 0.01 mm can cause abnormal noises or weak braking. CNC machining can control the tolerance within ±0.005 mm, which is 3 – 5 times more accurate than factory – original parts. After installation, the smoothness of operation can be visibly improved.
- Capable of Handling Any Shape: non – standard shape footrests and hollow frame connectors for modified bikes can’t be made by traditional stamping or casting processes. CNC milling machines and lathes can cut layer by layer like “3D printing”. Even curved surfaces and interlaced holes can accurately reproduce the design drawings.
- Greater Strength than Factory – original Parts: Factory – original parts often use thin materials or splicing processes to reduce costs. In contrast, CNC customization can process with a whole solid material. For example, for an aluminum alloy rear swingarm, after one – piece forming, the torsional strength can be increased by 40%. You don’t have to worry about deformation when taking sharp turns in gymkhana.
II. Choosing the Right Material is the First Step, Tailoring to Different Parts
Motorcycle parts come in all shapes and sizes, with different stress conditions, environments, and functions. Choosing the wrong material is a waste of money. Newcomers must keep in mind the characteristics and application scenarios of these commonly used materials:
- Aluminum Alloy (6061/7075): The King of Cost – effectiveness, the First Choice for Most Parts
- Suitable Parts: Handlebars, footrests, fuel tank guards, wheels (parts with high lightweight requirements).
- Why Choose It: Its density is only 1/3 that of steel. After processing, the parts are light, reducing the vehicle’s weight. After surface anodizing, it is wear – resistant and corrosion – resistant, and not easy to rust even when riding in the rain.
- Advantages: The tensile strength of 7075 aluminum alloy can reach 570MPa, 30% harder than 6061. It is also reliable for load – bearing parts (such as the rear swingarm), and the processing cost is more than half lower than that of titanium alloy.
- Stainless Steel (304/316): Durable and Rust – resistant, Essential for Outdoor Riding
- Suitable Parts: Exhaust pipes, brake hose connectors, chain adjusters (parts in contact with oil or rain).
- Why Choose It: 304 stainless steel can resist the corrosion of engine oil and mud. 316 stainless steel is even more powerful, not afraid of salt spray when riding by the sea. After three to five years, the surface is still shiny.
- Advantages: It has good toughness and is not easy to break during collisions. For example, for the exhaust pipe fixing bracket, stainless steel is more resistant to deformation than aluminum alloy.
- Titanium Alloy (TC4): The “Ultimate Choice” for High – end Players
- Suitable Parts: Shock absorber links, valve spring seats, high – strength bolts (core parts that pursue extreme performance).
- Why Choose It: Its strength is similar to that of steel, but its weight is 50% lighter than steel and 2 times harder than aluminum alloy. Moreover, its fatigue resistance is extremely high, and it is not easy to crack under repeated stress.
- Advantages: When riding off – road or on long – distance trips, titanium alloy parts can withstand extreme temperature differences (- 50℃ to 150℃). However, the price is relatively high, 3 – 4 times that of aluminum alloy, and it is generally used for high – end modifications.
- Carbon Fiber: The Favorite of Lightweight Fanatics
- Suitable Parts: Fairings, mudguards, seat bases (non – load – bearing appearance parts).
- Why Choose It: Its weight is only 1/2 that of aluminum alloy, but its hardness is 5 times that of steel. It can further lower the vehicle’s center of gravity, making high – speed cornering more stable.
- Note: It can’t be used for load – bearing parts (such as the frame). It is easy to break during collisions, and special tools are required during processing, otherwise, burrs are likely to occur.
III. Don’t Choose Processing Technologies Blindly, Select “Tools” According to Part Complexity
CNC machining is not just about “milling” and “turning”. Different technologies are suitable for different – shaped parts. Choosing the wrong one will affect accuracy and cost:
- Three – axis Machining: The Cost – effective Choice for Simple Parts
- Suitable Parts: Planar parts (such as engine side covers), regular cylindrical parts (such as handlebar risers).
- Characteristics: The tool can only move up – down, left – right, and front – back. It is efficient for processing planes or simple curved surfaces, with a low unit price, suitable for mass customization.
- Five – axis Machining: The “Exclusive Skill” for Complex and Irregular Parts
- Suitable Parts: Curved wheels, hollow frames, polyhedron connection seats (parts with inclined angles or complex cavities).
- Characteristics: The spindle can rotate at multiple angles. For example, when processing the irregular connection head of a motorcycle front fork, all surfaces can be cut in one clamping without having to be repeatedly removed and re – oriented. The accuracy can be increased by 2 – 3 levels.
- Disadvantages: The equipment is expensive, and the processing cost is twice that of three – axis machining. The cost is relatively high for small – batch customization.
- Electrical Discharge Machining (EDM): The “Nemesis” of Hard Materials or Fine Structures
- Suitable Parts: Molds, high – hardness gears (such as precision gears inside the engine), fuel injectors with small holes.
- Characteristics: It doesn’t require direct contact between the tool and the material. It processes by electric spark corrosion. It can handle hard steel with a hardness above HRC50. Even micro – holes of 0.1 mm can be accurately drilled, suitable for parts with extremely high precision requirements.
IV. Want to Ensure High – quality Parts? Keep an Eye on These 3 Links in the Processing
Even if the materials and technologies are selected correctly, cutting corners during the processing can still lead to problems with the finished product. Reliable manufacturers will strictly follow these steps:
- Pre – production Drawing Review: Don’t Let the Design “Trip Up” the Processing
After receiving the drawings, professional manufacturers will first conduct DFM (Design for Manufacturability). For example, if there is a deep hole with a diameter of 5 mm and a depth of 50 mm on the part, they will remind you that “a depth – to – diameter ratio of 10:1 is likely to break the tool, it is recommended to change it to a 6 – mm diameter” to avoid repeated waste during processing. If it is a mating part (such as a bearing and a bushing), they will also check whether the tolerances match to prevent problems such as non – fitting or being too loose. - “Three – inspection System” during Processing: First – piece Inspection, In – process Inspection, and Final Inspection are Indispensable
- First – piece Inspection: First, make 1 – 2 parts from the first batch. Use a coordinate measuring machine to measure key dimensions (such as hole – spacing, flatness). Only if they are qualified will mass production proceed.
- In – process Inspection: Randomly inspect one part every 20 parts processed. For example, check the perpendicularity of the handlebar. If the deviation exceeds 0.02 mm, stop the machine and adjust it to avoid batch problems.
- Final Inspection: After all parts are completed, scan them with a laser scanner to generate a 3D model and compare it with the drawing. Parts with excessive errors are directly scrapped, without any compromise.
- Surface Treatment: The “Last Barrier” for Appearance and Durability
- For aluminum alloy parts, it is recommended to do hard anodizing with a film thickness of 15 – 20 microns. It can’t be scratched by a fingernail and can be dyed (black, silver, blue, etc.), maximizing personalization.
- For stainless – steel parts, electrolytic polishing can be done to reduce the surface roughness to Ra0.02 microns. Oil is not easy to adhere, and it is more convenient to clean.
- Note: Burrs must be removed before surface treatment (using ultrasonic cleaning + manual polishing), otherwise, it may cut hands or damage other parts when installing.
V. 3 Pit – avoiding Tips for Newcomers
- Don’t Just Look at the Price: For aluminum alloy handlebars, small factories may process with waste materials, resulting in poor accuracy and easy breakage. Big factories use national standard 6061 materials and add 3 more inspection procedures in the processing. Although it is 20% more expensive, it is more reassuring to use.
- Request for Material Certificates: Regular manufacturers will provide a “material list” marked with material grades, hardness, and mechanical properties. For example, the hardness of 7075 aluminum alloy must reach above HB150 to avoid being replaced with 6061.
- Sample First, Then Mass – produce: Even if you only need to make 10 parts, ask the manufacturer to make 1 sample for trial installation first. Check whether it matches the vehicle body and whether there are abnormal noises. Only if there are no problems, proceed with mass production to avoid rework and waste of money.
The core of customizing motorcycle CNC parts is “precise matching” – the part function, material characteristics, and processing technology should be in harmony. If chosen correctly, your motorcycle will not only have a significant boost in appearance but also an upgrade in performance. If chosen wrongly, you may spend money but also affect riding safety. If customizing parts for imported motorcycles (such as Harley – Davidson, Ducati), it is best to find a manufacturer with export experience. They are more familiar with European and American standards (for example, the surface treatment must pass the 48 – hour salt spray test), and pay more attention to details.
If you have any questions about customizing motorcycle CNC parts, such as material selection, determination of processing technology, etc., you can leave an online message for consultation. We will provide you with professional answers and suggestions. Good parts are “polished” out. Spending a little more time on communication and screening will definitely not disappoint you with the finished product.