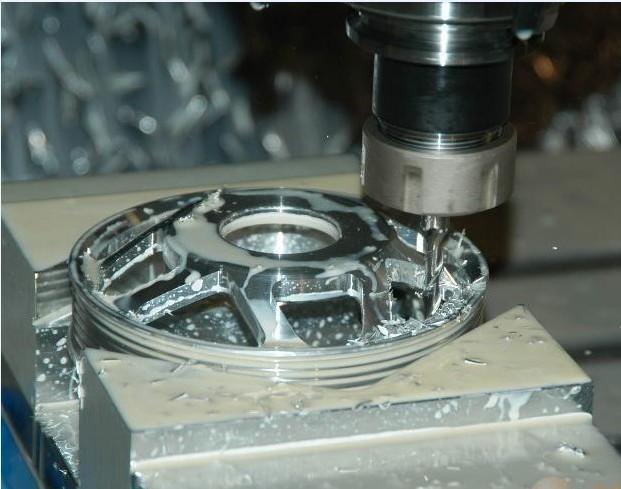
The cost of CNC machining varies widely and cannot be generalized, as it is influenced by multiple factors. For simple parts like ordinary small aluminum components, the cost per piece may be as low as tens of yuan. However, complex, high-precision parts made from special materials (such as titanium alloy) can cost hundreds or even thousands of yuan per piece. In mass production, the unit cost decreases due to fixed cost allocation—for example, producing 1,000 simple plastic parts may reduce the cost per piece from 7 $ to around 4 $.
CNC machining costs are affected by the following factors:
– Complexity of Part Design
- Geometric Shape: Simple, regular shapes (e.g., cubes, cylinders) incur low costs because machining paths are easy to plan, reducing processing time. Complex curved surfaces, multiple grooves, or internal structures (e.g., aerospace engine blades) require more programming time and sophisticated techniques, increasing costs.
- Precision Requirements: High-precision tolerances (e.g., ±0.01mm) are far costlier than standard tolerances (±0.1mm). They demand more precise equipment, high-quality tools, and frequent measurements/ adjustments, escalating both time and labor costs.
- Feature Details: Micro-features (e.g., tiny holes, narrow slots) are difficult to machine, requiring special tools and meticulous operations, which raises costs.
– Material Type
- Material Cost: Among common materials, plastics are relatively inexpensive (tens of yuan per kilogram). For metals, aluminum costs moderate (about 20–50 yuan/kg), while precious metals or special alloys (e.g., titanium) can cost hundreds or more per kilogram, directly impacting total machining costs.
- Machinability: Soft, easy-to-cut materials (e.g., aluminum alloys) cost less due to minimal tool wear and fast processing. Hard, high-strength materials (e.g., stainless steel, titanium) require specialized tools and longer processing times, increasing costs.
– Production Quantity
- Batch Effect: For low-volume production, fixed costs (e.g., programming, equipment setup) are high per piece. As batch sizes increase, fixed costs are spread, lowering unit costs. For example, a custom part may cost 200 yuan, but producing 100 pieces could reduce the unit cost to 100 yuan.
– Machinery and Tools
- Machine Type: High-end 5-axis CNC machines can process complex parts but come with high depreciation and maintenance costs, making them costlier than standard 3-axis machines. Simple parts can be machined by 3-axis machines at lower costs.
- Tool Selection: Specialized tools (e.g., custom tools for super-hard materials) are expensive. Frequent tool wear and replacement also add to costs, increasing both processing time and procurement expenses.
– Labor Costs
- Skill Level: Experienced technicians for programming, operation, and quality inspection command higher salaries. Complex parts require skilled labor, driving up labor costs.
- Regional Differences: Labor costs vary by region—developed areas have higher costs than less-developed regions, affecting overall machining expenses.
– Post-Processing and Other Factors
- Surface Treatment: Processes like anodizing, chrome plating, or polishing add costs. Different treatments vary in expense (e.g., chrome plating is costlier than simple painting).
- Logistics: Large, heavy parts incur high transportation costs, especially over long distances, impacting total machining costs.