The cost to machine aluminum varies widely due to multiple factors and can’t be precisely generalized. Simple aluminum parts like ordinary aluminum gaskets with basic cutting or drilling may cost as low as a few dollars per piece. However, complex, high-precision aluminum components for aerospace applications can cost hundreds or even thousands of dollars. Batch processing reduces unit costs through fixed cost allocation—for example, producing 1,000 simple aluminum brackets might lower the cost from $50 to around $30 per piece.
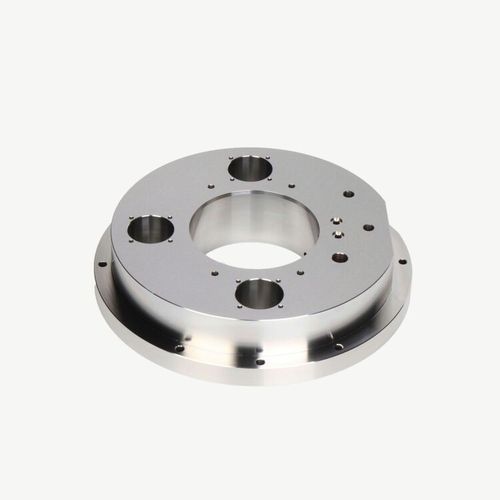
Aluminum machining costs are influenced by the following factors:
– Part Design Complexity
- Geometric Shape: Simple, regular shapes (e.g., aluminum cuboids) are low-cost due to easy machining path planning. Complex curved surfaces or intricate internal structures (e.g., aluminum engine blocks for cars) require sophisticated programming and multi-step processes, significantly increasing costs.
- Precision Requirements: Standard precision (±0.1mm) incurs lower costs, while high precision (±0.01mm) demands advanced equipment, premium tools, and frequent inspections, extending processing time and expenses.
- Feature Details: Micro-features like tiny holes or narrow slots require specialized tools and meticulous operations, driving up costs.
– Aluminum Material Type
- Alloy Type: Common 6061 aluminum is cost-effective with good machinability, while special alloys like 7075—though stronger—are harder to machine and pricier, raising overall costs.
- Material Condition: Pre-stretched or aged aluminum may incur different costs. For example, solution-treated aluminum has higher hardness, accelerating tool wear and increasing tool replacement and processing time costs.
– Machining Processes and Equipment
- Processing Methods: Milling or turning on CNC machining centers have predictable costs, while special processes like EDM (electrical discharge machining) for complex holes in aluminum parts carry higher equipment operation costs.
- Equipment Precision: High-end 5-axis machines handle complex parts but come with steep purchase and maintenance costs, driving up fees. Basic 3-axis machines are cheaper for simple parts.
– Production Volume
- Batch Effect: Low-volume production spreads high fixed costs (e.g., equipment setup, programming) per piece. Larger batches reduce unit costs—e.g., a custom aluminum part costing $200 individually may drop to $100 when producing 100 pieces.
– Post-Processing Requirements
- Surface Treatment: Anodizing (improving corrosion resistance) costs tens of dollars per square meter, while special treatments like hard chrome plating (complex processes) can cost over $100 per square meter.
- Heat Treatment: Processes like quenching or tempering to improve material properties add extra equipment, energy, and labor costs.
– Regional and Labor Costs
- Geographic Differences: Developed regions (e.g., coastal first-tier cities) have 20–50% higher machining costs than less-developed areas due to labor and rent expenses.
- Labor Skill Level: Experienced technicians ensuring precision in complex parts command higher wages, particularly for high-tolerance aluminum components where expertise is critical.