Choosing a CNC parts manufacturer involves 6 key steps:
1) Define your needs (material, tolerance, volume);
2) Evaluate their equipment (5-axis machines, precision levels);
3) Check quality systems (ISO certifications, inspection tools like CMMs);
4) Review industry experience (e.g., aerospace, medical);
5) Compare costs, lead times, and scalability;
6) Validate communication and after-sales support to ensure reliability.
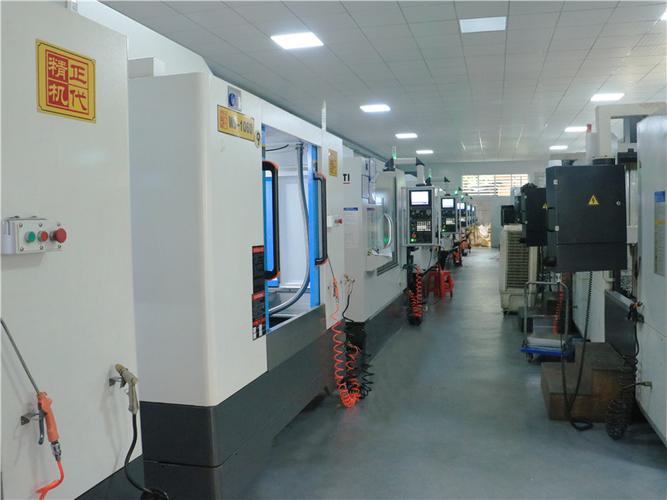
Detailed Analysis of Selecting a CNC Parts Manufacturer
1. Technical Capabilities & Equipment
A manufacturer’s technical infrastructure directly determines their ability to produce precise, complex parts:
-
Machine Portfolio: Prioritize shops with diverse CNC equipment tailored to your part’s complexity:
- 3-axis machines: Suitable for simple flat or cylindrical parts (e.g., brackets, shafts) with tolerances of ±0.01mm.
- 5-axis machining centers: Essential for complex geometries (e.g., turbine blades, mold cores) requiring multi-angle cuts. Look for machines with positioning accuracy ±0.001mm (e.g., Haas UMC-750 or DMG Mori NHX series) to handle tight tolerances.
- High-speed machining (HSM) capabilities: Critical for hard materials (Inconel, titanium) or thin-walled parts (0.5–2mm). HSM (10,000–40,000 RPM) minimizes heat and deformation, a must for aerospace or medical components.
-
Precision & Tolerance Range: Verify the shop’s ability to meet your specs. For example:
- General industrial parts (e.g., automotive brackets) require ±0.01mm, achievable with standard CNCs.
- High-precision parts (e.g., medical implants, optical components) need ±0.001mm or better—ensure the shop uses CMMs (Coordinate Measuring Machines) with ±0.0005mm accuracy for validation.
-
Tooling & Software: Advanced CAM software (e.g., Mastercam, SolidWorks CAM) ensures efficient toolpaths for complex parts. Shops with in-house tooling (custom fixtures, high-precision end mills) reduce lead times and errors compared to those relying on external suppliers.
2. Quality Management Systems
Rigorous quality control prevents costly defects and ensures compliance with industry standards:
-
Certifications: Look for relevant accreditations based on your industry:
- ISO 9001: Basic quality management, suitable for general industrial parts.
- AS9100: Mandatory for aerospace parts (e.g., engine components), ensuring traceability and process control.
- ISO 13485: Required for medical devices (e.g., surgical tools), with strict documentation for material sourcing and sterilization compatibility.
- ITAR registration: Necessary for defense-related parts to comply with export controls.
-
Inspection Processes: A reliable shop implements multi-stage checks:
- In-process inspection: Use of probes (e.g., Renishaw) integrated into CNC machines to measure critical dimensions during production, catching errors early.
- Final inspection: CMMs, optical scanners, or profilometers verify GD&T (Geometric Dimensioning and Tolerancing) features (flatness, concentricity) and surface finish (Ra values). For example, a shop producing hydraulic valves should validate seal surfaces to Ra <0.8μm to prevent leaks.
- Traceability: Ability to track materials from raw stock to finished part (e.g., heat treat certificates for aluminum or steel) is critical for aerospace or medical applications, where material defects can cause failures.
3. Material Expertise
A manufacturer’s ability to handle your part’s material impacts quality and consistency:
-
Material Range: Ensure the shop has experience with your material’s unique challenges:
- Metals: Aluminum (6061, 7075), steel (304 stainless, 4140), titanium (Ti-6Al-4V), and superalloys (Inconel 718). For example, machining titanium requires specialized coolants and tooling to avoid heat-induced warping—ask for case studies with similar materials.
- Plastics & composites: ABS, PEEK, or carbon fiber-reinforced polymers (CFRP). Shops working with composites must manage fiber fraying and resin adhesion, requiring expertise in low-force cutting.
-
Material Sourcing: Reputable shops source from certified suppliers (e.g., Alcoa for aluminum, Timet for titanium) and provide material certificates (mill test reports) to confirm chemical composition and mechanical properties—critical for parts under load (e.g., structural brackets).
4. Production Capacity & Scalability
Evaluate whether the manufacturer can meet your volume and lead time requirements:
-
Volume Flexibility:
- Prototyping & small batches (1–100 parts): Shops with quick-change setups and digital workflows (e.g., 3D-printed fixtures) reduce lead times to 1–5 days.
- Mass production (10,000+ parts): Prioritize shops with automated cells (robotic loading/unloading) and statistical process control (SPC) to maintain consistency. For example, automotive suppliers often use dedicated lines for high-volume parts (e.g., sensor housings) with cycle times <2 minutes.
-
Lead Time Reliability: Ask for historical data on on-time delivery (target >95%). Shops with ERP systems (e.g., SAP, QuickBooks) for production planning are more likely to avoid delays from material shortages or machine downtime.
-
Scalability: If your project may grow (e.g., from prototype to 10,000 units), ensure the shop can scale without sacrificing quality. This includes having spare machine capacity and a supply chain capable of sourcing bulk materials.
5. Industry Experience & Case Studies
A manufacturer’s track record in your industry indicates familiarity with unique requirements:
-
Aerospace: Look for experience with lightweight materials (titanium, CFRP) and strict traceability (each part linked to raw material batches). Shops should understand aerospace standards like NADCAP (for special processes like heat treatment).
-
Medical Devices: Prioritize shops experienced with biocompatible materials (titanium, PEEK) and cleanroom machining (Class 8 or better) to avoid contamination. They should comply with FDA regulations for documentation and validation.
-
Automotive: Experience with high-volume, cost-sensitive parts (e.g., aluminum castings machined to ±0.02mm) and IATF 16949 certification ensures adherence to automotive quality standards.
-
Electronics: Shops handling small, precise parts (e.g., connector pins, heat sinks) should demonstrate expertise in micro-machining (features <1mm) and tight tolerance control (±0.005mm).
6. Cost, Communication & Support
Beyond technical capabilities, practical factors influence long-term partnership viability:
-
Cost Transparency: Avoid shops with vague quotes. Detailed breakdowns (material, labor, setup, inspection) help identify cost drivers. For example, complex 5-axis parts may have higher setup costs but lower per-unit costs at scale.
-
Communication: Choose manufacturers with clear, responsive communication. They should provide design for manufacturability (DFM) feedback early (e.g., suggesting fillet radii to reduce machining time) and share production updates (e.g., via project management software).
-
After-Sales Support: Reliable shops offer post-delivery services: rework for out-of-spec parts, replacement of defective units, or adjustments to tooling for future runs. This is critical for long-term projects (e.g., annual production of machinery components).
7. Red Flags to Avoid
Watch for warning signs that indicate poor reliability:
- Lack of certifications or unwillingness to share quality reports.
- Limited equipment (e.g., only 3-axis machines for 5-axis parts).
- Inconsistent lead times or vague commitments.
- Poor communication (delayed responses, unclear quotes).
Xiamen Goldcattle
We are a national grade high-tech enterprise which professionally speciallized in R&D and manufacture high precise injection parts, high precise machining parts, stamping parts, plastic injection parts and injection molded parts. We plastic injection parts manufacturer provide total solution to customers including molding design and manufacture, parts mass production and assembly.
As an OEM and ODM factory, we have a team of experienced and skillful industrial designers and engineers who are engaged in mold designing, manufacturing and CNC programming. With the principle of “high-quality, efficiency, honesty and service”, the aim of “sustainable operation, customers uppermost” and the good attitude of work and service, we are looking forward to building long-term and win-win business relationships with clients from all over the world.
In summary, selecting a CNC parts manufacturer requires balancing technical capabilities, quality systems, industry experience, and practical factors like cost and communication. By systematically evaluating these areas, you ensure a partner capable of delivering precise, reliable parts that meet your project’s needs.