Yes, aluminum 6061 is highly machinable and widely used in CNC machining. Its excellent machinability stems from balanced mechanical properties—medium strength, good ductility, and low work-hardening rate, making it suitable for various processes like milling, turning, drilling, and tapping. The cost to machine 6061 aluminum typically ranges from $5 to $500 per piece, depending on part complexity, precision, and batch size. For example, a simple 6061 aluminum bracket with basic features may cost $10–$30 per piece in small batches, while complex aerospace components with tight tolerances (±0.01mm) can cost $200–$500 each.
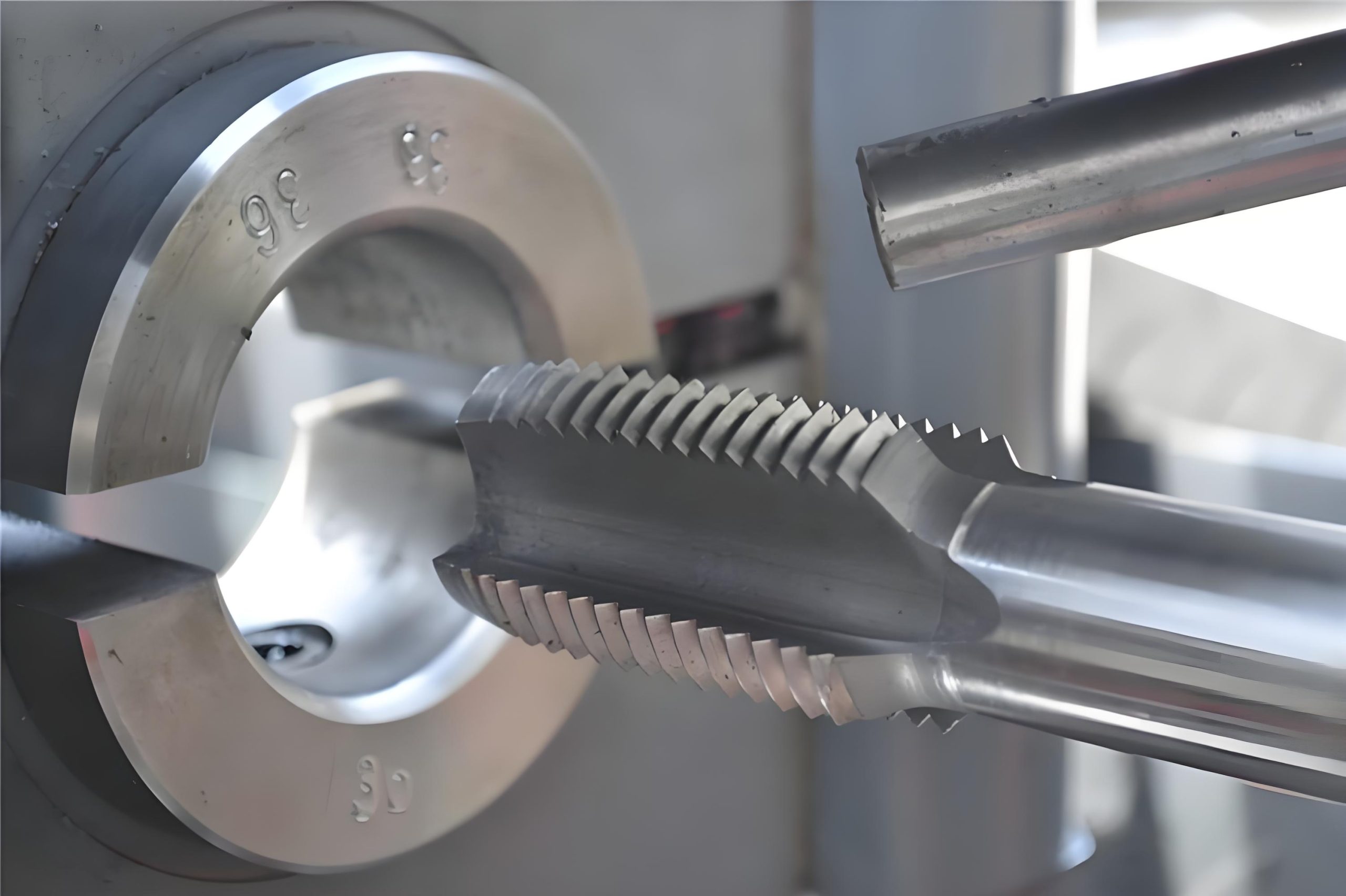
– Why Aluminum 6061 Is Machinable?
- Mechanical Properties
- Medium Strength: Tensile strength of ~310 MPa allows efficient cutting without excessive tool wear, unlike harder alloys like 7075 (which requires specialized tools).
- Low Work-Hardening: Unlike stainless steel, 6061 doesn’t harden significantly during machining, preventing tool damage and ensuring consistent surface finishes.
- Thermal Conductivity
- High thermal conductivity (180 W/m·K) dissipates heat quickly, reducing the risk of workpiece distortion and tool overheating during high-speed machining.
- Chip Formation
- 6061 produces short, breakable chips that are easy to remove, minimizing machine jams and improving processing efficiency (critical for automated CNC setups).
– Machining Costs and Influencing Factors
- Part Complexity
- Simple Parts: Basic shapes (e.g., rectangular blocks, flat plates) with standard tolerances (±0.1mm) cost $5–$20 per piece. For instance, a 6061 aluminum plate (100x50x10mm) with drilled holes may cost ~$15 in a batch of 50.
- Complex Parts: Curved surfaces, thin walls, or intricate internal structures (e.g., motor housings) require multi-axis machining, raising costs to $50–$200 per piece.
- Precision Requirements
- Tight tolerances (±0.02mm) demand high-precision equipment (e.g., 5-axis CNC machines) and longer setup times, increasing costs by 30–50%. A 6061 aerospace bracket with ±0.01mm tolerance might cost $300–$500 per piece.
- Batch Size
- Small Batches (1–100): Fixed costs (programming, tooling) dominate, with unit costs averaging $20–$100.
- Large Batches (1,000+): Economies of scale reduce unit costs to $5–$30. For example, 1,000 6061 aluminum washers (standard size) may cost $8 each.
– Optimal Machining Practices for 6061
- Tooling Recommendations
- Use carbide or high-speed steel (HSS) tools with sharp edges to minimize burrs. Coated tools (e.g., TiN coating) extend tool life by 2–3 times, reducing replacement costs ($10–$50 per tool).
- Cutting Parameters
- High spindle speeds (3,000–6,000 RPM) and moderate feed rates (100–300 mm/min) optimize material removal while preventing heat buildup. Faster speeds can reduce machining time by 20–30%, lowering labor costs ($20–$50/hour).
- Surface Finishing Costs
- Anodizing (common for 6061) costs $2–$5 per square foot, enhancing corrosion resistance. Polishing or powder coating adds $5–$10 per part, depending on complexity.
– Comparative Machinability vs. Other Alloys
Alloy | Machinability Rating | Relative Cost | Typical Applications |
---|---|---|---|
6061 | 4/5 (excellent) | Low ($5–$500/part) | Prototypes, automotive parts |
7075 | 2/5 (moderate) | High ($100–$1,000/part) | Aerospace components |
2024 | 3/5 (good) | Medium ($20–$800/part) | Aircraft structures |
– Real-World Cost Examples
- Example 1: 100pcs 6061 aluminum brackets (simple L-shape, 50x30x5mm, ±0.1mm)
- Material cost: $2/piece
- Machining cost: $8/piece
- Total: $10/piece ($1,000 for the batch)
- Example 2: 10pcs 6061 custom parts (complex curved surface, ±0.02mm, with anodizing)
- Material cost: $15/piece
- Machining cost: $80/piece
- Anodizing: $5/piece
- Total: $100/piece ($1,000 for the batch)
– Tips to Reduce Machining Costs
- Simplify Design: Avoid unnecessary tight tolerances or complex features. For example, changing a tolerance from ±0.01mm to ±0.05mm can reduce costs by 40%.
- Opt for Standard Sizes: Use 6061 extruded profiles (e.g., 10mm thickness) to minimize material waste, saving $2–$5 per part.
- Consolidate Batches: Ordering 500 pieces instead of 100 can lower unit costs by 35–50%, as seen in mass-produced 6061 consumer electronics casings.