Brass machining is a manufacturing process that shapes brass alloys into precise parts via cutting, drilling, milling, or turning. Leveraging brass’s excellent machinability (due to its low hardness and high ductility), the process involves material selection, prepping blanks, precision cutting with CNC or manual tools, and post-treatments (deburring, polishing) to achieve desired dimensions and surface finishes, used for parts from plumbing fittings to electronics.
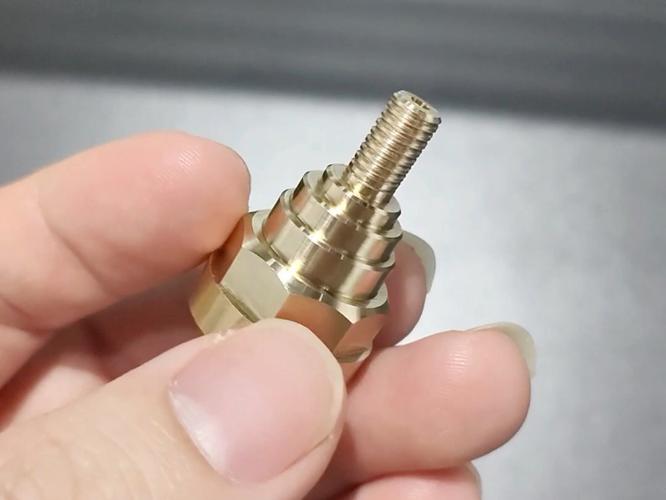
Detailed Analysis of Brass Machining Process
1. Core Process Steps
Brass machining follows a structured workflow to balance precision and efficiency:
-
Material Selection & Preparation
- Alloy Choice: Brass alloys (copper-zinc with optional additives) are selected based on application. Leaded brass (e.g., C36000, 2–3% lead) offers superior machinability for high-volume parts (fittings, connectors) due to reduced tool wear. Unleaded brass (e.g., C69300, zinc-tin-copper) is used in potable water systems or food-grade parts, requiring slightly adjusted cutting parameters.
- Blank Preparation: Raw brass (bars, sheets, or rods) is cut to near-net shape using saws or shears, leaving 1–5mm of stock for machining. Deburring initial edges prevents tool damage during subsequent steps.
-
Primary Machining Operations
- Turning: Rotates the brass blank while a stationary tool cuts outer diameters, tapers, or threads. Ideal for cylindrical parts (valve stems, bushings). CNC lathes operate at 1,000–3,000 RPM with feed rates of 0.1–0.3 mm/rev, leveraging brass’s low cutting resistance to achieve tight tolerances (±0.01mm).
- Milling: Uses rotating multi-tooth cutters to shape flat or complex surfaces (e.g., gear teeth, mounting flanges). CNC mills with 3–5 axes handle intricate geometries, such as slots or pockets, with spindle speeds of 2,000–4,000 RPM to avoid heat buildup.
- Drilling & Tapping: Creates holes (for fasteners or fluid flow) using twist drills or specialized bits. Brass’s ductility reduces chipping, allowing high feed rates (0.2–0.5 mm/rev). Tapping (creating internal threads) is efficient in brass due to its ability to form clean threads without cracking.
- Grinding (Optional): For ultra-smooth surfaces (Ra <0.8μm) or tight dimensional control (±0.001mm), surface grinders refine critical features (e.g., seal faces on valves).
-
Post-Machining Treatments
- Deburring: Removes sharp edges using tumbling (with abrasive media) or robotic brushes, critical for safety (e.g., plumbing parts) and assembly (prevents seal damage).
- Polishing: Achieves decorative finishes (mirror-like or satin) via abrasive belts (80–600 grit) or buffing wheels with compounds (rouge for luster). Polished brass parts (e.g., musical instrument valves) enhance aesthetics and corrosion resistance.
- Plating (Optional): Electroplating with nickel, chrome, or gold improves wear resistance or appearance. For example, brass electrical connectors are often nickel-plated to prevent tarnishing.
2. Technical Considerations
Brass’s unique properties dictate specific machining techniques:
- Machinability Factors: Brass (hardness 50–100 HB) cuts easily due to its low shear strength, producing continuous, manageable chips. Lead additions (in C36000) act as internal lubricants, reducing friction between tool and workpiece, extending tool life by 30–50% vs. lead-free alloys.
- Tool Selection: High-speed steel (HSS) tools suffice for low-volume jobs, while carbide tools (coated with TiN or TiAlN) are preferred for high-speed CNC machining (3,000+ RPM) to resist wear. For fine finishes, sharp tools with positive rake angles (5–10°) minimize burr formation.
- Coolant & Lubrication: Soluble oils or synthetic coolants are critical to dissipate heat (preventing brass softening) and flush chips. This is especially important for deep drilling or threading, where chip buildup can cause tool breakage or surface defects.
3. Key Parameters for Precision
Optimal parameters vary by operation but follow general guidelines:
- Turning: Spindle speeds of 1,000–3,000 RPM; feed rates 0.1–0.3 mm/rev. For thin-walled brass parts (e.g., instrument tubing <1mm thick), reduce feed to 0.05–0.1 mm/rev to avoid deformation.
- Milling: 2,000–4,000 RPM with feed rates 50–200 mm/min. Climb milling (tool moves with the workpiece) reduces chatter, improving surface finish on flat parts (e.g., switch plates).
- Drilling: Drill speeds 1,500–3,000 RPM; feed rates 0.1–0.2 mm/rev. For small holes (<3mm), use high-speed steel drills with parabolic flutes to enhance chip evacuation.
4. Materials: Alloy Variations & Impact
Different brass alloys require adjusted approaches:
- Leaded Brass (C36000, “Free-Cutting Brass”): Contains 2–3% lead, which acts as a chip breaker and lubricant. Ideal for high-volume, automated machining (e.g., plumbing elbows, electrical terminals) due to minimal tool wear and fast cycle times.
- Unleaded Brass (C69300, C70600): Used in potable water systems (to avoid lead leaching) or food-contact parts. Harder than leaded brass, it requires slower feeds (0.05–0.2 mm/rev) and sharper tools to prevent work hardening.
- High-Zinc Brass (C46400, “Naval Brass”): Contains 39–42% zinc, offering strength for marine hardware (valves, fittings). Machining requires higher cutting forces, so carbide tools and increased coolant flow are necessary.
5. Typical Products & Applications
Brass machining produces parts across industries, each with unique requirements:
- Plumbing & HVAC: Fittings (elbows, tees), valves, and pipe nipples. Machining focuses on tight dimensional tolerances (±0.02mm) for leak-free seals and smooth internal bores to reduce pressure drop.
- Electronics: Connectors, terminals, and heat sinks. Precision milling ensures pin alignment (±0.01mm) for reliable electrical contact, while polished surfaces prevent corrosion in humid environments.
- Automotive: Fuel line fittings, sensor housings, and bearing cages. Brass’s corrosion resistance and machinability make it ideal for under-hood parts, with machining prioritizing vibration-resistant geometries.
- Musical Instruments: Trumpet valves, horn slides, and guitar tuning pegs. Polished surfaces (Ra <0.05μm) enhance sound resonance, while tight tolerances (±0.005mm) ensure smooth valve operation.
6. Challenges & Solutions
Brass machining has unique hurdles, addressed with targeted strategies:
- Burr Formation: Brass’s ductility leads to burrs on edges, especially in low-speed machining. Solutions include using sharp tools, high feed rates (to break chips), and post-machining tumbling with ceramic media.
- Work Hardening: Excessive cutting forces (e.g., in deep milling) can harden brass, making subsequent operations difficult. Mitigation: Use low-force, high-speed cutting and anneal parts (heat to 400–500°C) for large batches.
- Tarnishing: Uncoated brass oxidizes (turns green) in humid environments. Post-treatments like clear lacquering or passivation (with chromic acid) preserve finishes, critical for decorative parts (e.g., door handles).
In summary, brass machining combines material-specific techniques, precision tooling, and tailored parameters to leverage brass’s machinability, producing durable, high-precision parts across plumbing, electronics, automotive, and more. The process balances efficiency and quality, making brass a staple in manufacturing.