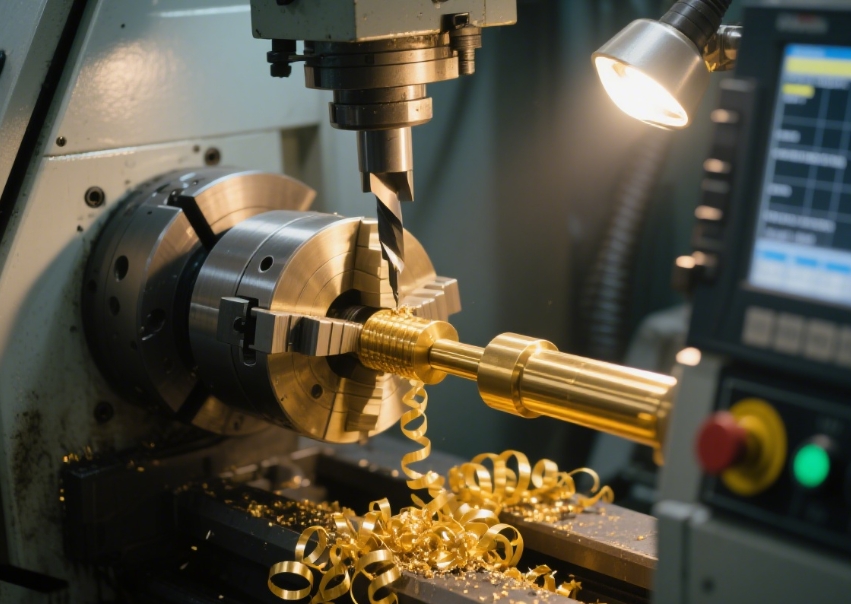
Answer:
A “milling cutter” is a general term for cutting tools used in milling operations, encompassing various types. An “end mill” is one type of milling cutter. The core difference is that an end mill has cutting edges at its end (bottom surface), allowing for axial (Z – axis) feed cutting, while most ordinary milling cutters (such as face mills and slot mills) have no cutting edges at the end and can only cut radially through the circumferential edges. End mills are mainly used for machining grooves, steps, contours, and three – dimensional surfaces, and are one of the most commonly used types of milling cutters.
A “milling cutter” is a general term for cutting tools used in milling operations, encompassing various types. An “end mill” is one type of milling cutter. The core difference is that an end mill has cutting edges at its end (bottom surface), allowing for axial (Z – axis) feed cutting, while most ordinary milling cutters (such as face mills and slot mills) have no cutting edges at the end and can only cut radially through the circumferential edges. End mills are mainly used for machining grooves, steps, contours, and three – dimensional surfaces, and are one of the most commonly used types of milling cutters.
Extended Answer
- Definition and Scope: Subordination and Classification
Milling Cutter
Scope: A general term for all cutting tools used in milling operations, which are divided into different types according to processing requirements.
Classification Basis: It can be classified into end mills, face mills, formed mills, slot mills, ball – nose mills, etc., based on the position, shape, and purpose of the cutting edges.
Nature: It is a broad concept that includes end mills and other various milling tools.
End Mill
Positioning: It belongs to a subset of milling cutters and is one of the most common milling tools.
Core Feature: It has cutting edges both axially (at the end) and radially (on the circumference), and usually has a cutting edge at the center of the end (allowing for axial penetration). - Structural Design: Differences in Cutting Edges and Shanks
Milling Cutter (Taking Face Mill as an Example)
Position of Cutting Edges: The cutting edges are mainly distributed on the circumferential side (such as in a cylindrical mill) or at the edge of the end face (such as in a face mill), and there are no cutting edges at the center of the end (no axial feed is possible).
Shank Structure: Some milling cutters adopt an indexable insert design (such as face mills), and the shank and the cutter body are detachable, which is suitable for large – plane machining.
Typical Shapes: Disk – shaped (face mill), cylindrical (slot mill), shaped – contour (such as gear milling cutter).
End Mill
Position of Cutting Edges:
End Face: There is a cutting edge at the center (flat – end end mill) or an arc – shaped edge (ball – nose end mill), enabling vertical plunge (Z – axis feed).
Circumference: Spiral or straight edges are used for radial cutting.
Shank Structure: It is made of integral carbide or high – speed steel. The shank is mostly a straight shank or a tapered shank, directly connected to the machine tool spindle.
Typical Shapes: Flat – end (flat – bottom), ball – nose, bull – nose (with an R – corner), etc., with a diameter range usually from 1 – 200 mm. - Cutting Methods: Feed Directions and Machining Capabilities
Milling Cutter (Non – End Mill Types)
Feed Limitation: It cannot directly penetrate the workpiece along the Z – axis axially and needs to penetrate radially (for example, a face mill needs to start from the edge of the workpiece).
Cutting Movement: It mainly relies on the relative movement between the rotation of the tool and the lateral movement (X/Y – axes) of the workpiece to complete the cutting, and is suitable for simple structures such as planes and grooves (except for some slot mills).
Limitation: It cannot machine closed cavities (such as blind – ended slots) and needs to drill a hole first before the tool can be inserted.
End Mill
Feed Flexibility:
Axial Feed (Z – axis): It can directly penetrate the workpiece vertically, machining closed grooves, blind holes, or three – dimensional surfaces.
Multi – axis Linkage: It can cooperate with the X/Y – axes to achieve contour milling, helical interpolation (such as thread milling).
Cutting Movement: It has both axial penetration and radial cutting capabilities. For example:
When machining a keyway, it can plunge axially to the required depth and then feed along the X – axis for cutting.
When machining a surface, it can fit the surface contour with a ball – nose end mill through the linkage of the X/Y/Z – axes. - Application Scenarios: Typical Parts and Industry Cases
Milling Cutter (Non – End Mill Types)
Face Mill: It is used for machining large planes (such as machine tool worktables, automotive panel mold planes), with high efficiency and low surface roughness.
Formed Mill: It is used for machining specific contours (such as gear tooth profiles, cam grooves), and the tool shape matches the cross – section of the part.
Slot Mill (without axial edge): It is used for machining through – slots (such as circuit board slots) and needs to penetrate from one end of the slot.
Industry Applications: Machining large structural part planes in aerospace, machining the parting surfaces of automotive molds, etc.
End Mill
Flat – End End Mill:
Machining grooves (such as T – slots, dovetail slots), step surfaces, and circuit board mounting holes.
Machining square cavities in mechanical parts (such as the internal slots of a gearbox housing).
Ball – Nose End Mill:
Machining curved surfaces in the mold industry (such as injection mold cavities, toy mold surfaces).
Machining the three – dimensional contours of aero – engine blades and automotive interior parts.
Bull – Nose End Mill:
It can be used for both planar and surface machining and is often used for the rough machining of molds to reduce tool wear. - Sub – classification of Tool Types: Diversity of End Mills and Expansion of the Scope of Milling Cutters
Sub – types of End Mills
According to End Shape:
Flat – End (Flat – Bottom) End Mill: Used for planes and right – angled grooves.
Ball – Nose End Mill: Used for curved surfaces and arc contours.
Bull – Nose (R – corner) End Mill: It has a rounded corner at the end, combining strength and surface – machining capabilities.
According to the Number of Teeth: 2 – flute (good for chip evacuation, suitable for aluminum parts), 4 – flute (high rigidity, suitable for steel parts), etc.
According to Material: High – speed steel (suitable for low – speed machining), carbide (suitable for high – speed cutting), ceramic (wear – resistant, used for hard materials).
Other Types of Milling Cutters (Non – End Mills)
Face Mill: Disk – shaped, with multiple inserts, used for large – plane machining.
Slot Mill: Some types have no axial edge and are only used for machining through – slots.
Form – copying Mill: Custom – made according to the part shape, such as gear milling cutters, thread milling cutters.
Roughing End Mill: It has a large helix angle and multiple teeth, used for roughing to remove a large amount of material. - Machining Efficiency and Precision: Flexibility of End Mills vs. Efficiency of Special – purpose Milling Cutters
End Mill
Efficiency: Since it needs to balance both axial and radial cutting, its rough – machining efficiency is lower than that of special – purpose milling cutters (such as face mills), but it is suitable for multi – feature composite machining (reducing tool – changing times).
Precision: Through multi – axis linkage, it can achieve high – precision surface machining (such as a mold precision of ±0.01 mm), and the surface roughness can reach below Ra 0.8 μm.
Other Milling Cutters
Face Mill: With a large diameter (such as 100 – 300 mm) and multiple inserts, it has high rough – machining efficiency, and the flatness can reach ±0.05 mm.
Formed Mill: It can machine a specific contour in one cut, with high efficiency but high tool cost, suitable for mass production.
In conclusion, “milling cutter” is a general term, and “end mill” is one of the most flexible types among them. Its axial cutting ability makes it a core tool for groove, contour, and surface machining. In actual production, the choice between them depends on the part structure, machining efficiency, and precision requirements, and they are often used in combination with other types of milling cutters.