With 26 years of expertise in automotive engine component manufacturing, Xiamen Goldcattle specializes in custom automotive engine parts—tailored for gasoline, diesel, hybrid, and electric vehicle engines. Our product range covers cylinder head covers, oil pans, intake manifolds, valve covers, turbocharger housings, and engine brackets. Leveraging advanced precision casting, CNC machining, and plastic injection molding technologies, we deliver parts that meet strict automotive standards for dimensional accuracy, heat resistance, and durability. Backed by ISO/TS 16949, IATF 16949, and ISO 14001 certifications, we support prototype development to mass production (100,000+ units/month) with ±0.01mm dimensional tolerance, serving 30+ global automakers and engine manufacturers.
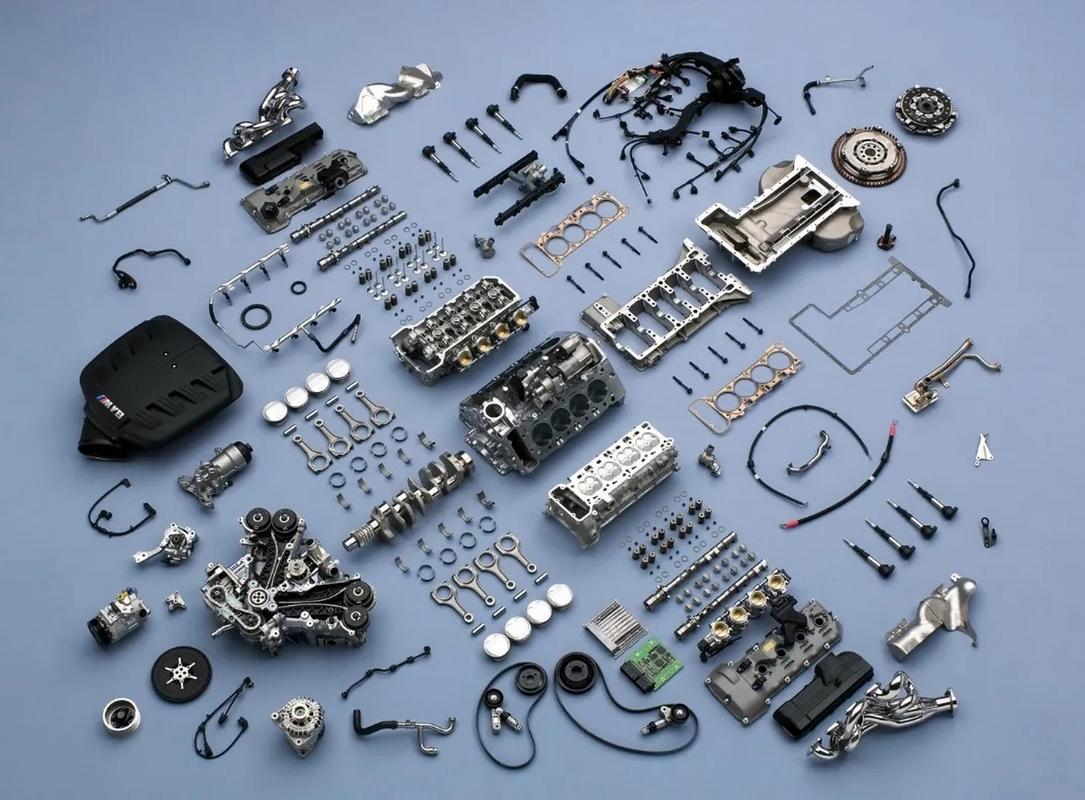
Core Processing Technologies: Engineering for Engine Performance
Automotive engine parts operate in extreme environments—high temperatures (up to 150℃ in engine bays), high pressure, and constant vibration. Goldcattle integrates cutting-edge technologies to ensure parts meet the rigorous demands of engine performance, safety, and longevity.
1. Precision Casting for Complex Engine Components
- Investment casting (lost-wax casting): Ideal for complex-shaped metal parts such as cylinder heads, intake manifolds, and turbocharger housings. Using ceramic molds with 0.05mm surface finish accuracy, this technology achieves intricate internal passages (e.g., coolant channels in intake manifolds) with minimal post-processing. A cast aluminum intake manifold for a 2.0L turbo engine produced this way reduced airflow resistance by 18% compared to welded assemblies.
- Sand casting with 3D printing molds: For large parts like engine blocks and oil pans, 3D-printed sand molds (0.1mm dimensional accuracy) enable rapid prototyping and small-batch production. This process cuts mold development time by 40% and allows for design iterations—critical for testing new engine layouts. A European engine manufacturer used this method to test 3 prototype oil pans in 6 weeks, vs. 12 weeks with traditional sand casting.
- Die casting for high-volume aluminum parts: Equipped with 200-1250 ton cold chamber die casting machines, we produce lightweight aluminum parts (e.g., valve covers, timing chain covers) with tight tolerances (±0.03mm). The high-pressure casting process ensures uniform material density, with tensile strength ≥220MPa—suitable for withstanding engine vibration.
2. High-Precision CNC Machining for Critical Fit
- 5-axis CNC milling: Used for finishing critical engine parts like camshaft covers, crankshaft bearings, and fuel injector mounts. With ±0.005mm positioning accuracy, it machines complex surfaces (e.g., sealing faces on cylinder head covers) to ensure leak-proof performance. A CNC-machined cylinder head cover for a hybrid engine achieved a flatness of 0.02mm/m, eliminating oil leaks even under 10bar pressure.
- Turn-mill machining: For rotational parts (e.g., crankshaft pulleys, water pump housings), this process combines turning and milling in one setup, reducing part handling and improving concentricity (≤0.01mm). A custom crankshaft pulley for a racing engine reduced rotational imbalance by 70%, minimizing vibration at high RPMs.
- Grinding technology: Cylindrical grinding (±0.001mm tolerance) and surface grinding (Ra ≤0.05μm) ensure precision on mating surfaces—such as the contact face between the oil pan and engine block, which must seal against 8bar oil pressure.
3. Advanced Plastic Molding for Lightweight Engine Parts
- Engineering plastic injection molding: For lightweight, corrosion-resistant parts (e.g., valve covers, air intake resonators), we use glass fiber-reinforced PPA (polyphthalamide) and PPS (polyphenylene sulfide). These materials withstand 150℃ continuous operating temperatures and resist engine oils/fuels. A PPA valve cover for a 1.5L gasoline engine reduced weight by 45% vs. aluminum, improving fuel efficiency by 1.2%.
- Insert molding: Integrates metal inserts (e.g., threaded bushings, heat sleeves) into plastic parts during molding, enhancing structural strength. A plastic oil filter housing with metal thread inserts passed 50,000+ pressure cycles (5-8bar) without leakage—meeting the 10-year/150,000km durability requirement.
4. Surface Treatment for Extreme Durability
- Ceramic coating: Applied to piston crowns and exhaust manifolds, this coating (thickness 50-100μm) withstands temperatures up to 800℃, reducing heat transfer to the engine block by 30% and improving thermal efficiency.
- Electroplating: Hard chrome plating on camshaft lobes and valve stems increases surface hardness (up to 65 HRC), reducing wear by 50% compared to uncoated parts.
- Anodizing: For aluminum parts like oil coolers and turbocharger intercooler end tanks, anodizing creates a 10-20μm protective layer that resists corrosion from coolants and road salts—tested to withstand 1,000 hours of salt spray (ASTM B117) with no rust.
Material Expertise: Matching Materials to Engine Environments
Engine parts face diverse stressors—from high heat in combustion chambers to chemical exposure in oil systems. Goldcattle selects and modifies materials to optimize performance and longevity:
Material | Modified Formulations | Application Scenarios | Key Technical Properties |
---|---|---|---|
Gray Cast Iron | Ni-resist (for high temperature), pearlitic | Cylinder blocks, exhaust manifolds | High compressive strength (≥300MPa), excellent heat retention, cost-effective for heavy-duty engines. |
Aluminum Alloy (A356, 6061) | T6 heat treatment, 10-20% silicon | Cylinder heads, intake manifolds, oil pans | Lightweight (density 2.7g/cm³), good thermal conductivity, 30% weight reduction vs. cast iron. |
Ductile Iron | Spheroidal graphite, copper alloying | Crankshafts, camshafts | Tensile strength ≥600MPa, impact resistance (-40℃), fatigue resistance for high-stress rotating parts. |
PPA (Polyphthalamide) | 30-50% glass fiber reinforcement | Valve covers, sensor housings | Heat resistance (continuous use at 150℃), chemical resistance to engine oil/fuel, low moisture absorption. |
Titanium Alloy (Ti-6Al-4V) | Beta heat treatment | Racing engine connecting rods, turbocharger parts | High strength-to-weight ratio, corrosion resistance, 40% lighter than steel with similar strength. |
Customization Capabilities: From Prototype to Production
Engine development requires tight collaboration—Goldcattle supports automakers and Tier 1 suppliers through every stage of the product lifecycle:
- DFMEA & design optimization: Our engineering team conducts Design Failure Mode and Effects Analysis (DFMEA) to identify potential issues (e.g., oil leakage, vibration fatigue) early. For a new diesel engine oil pan, we redesigned the gasket groove to reduce sealing pressure requirements by 20%.
- Rapid prototyping: Uses CNC machining (for metal parts) and SLA 3D printing (for plastic prototypes) to produce functional samples in 3-5 days. A US engine manufacturer tested 2 prototype turbocharger housings in 2 weeks, accelerating their development timeline by 30%.
- Low-volume production: 10-1,000 units via investment casting or CNC machining, ideal for engine testing, racing teams, or vintage car restorations. A classic 1960s Ford V8 engine rebuild project required 50 custom aluminum intake manifolds, produced to original specs with modern materials.
- Mass production: 10,000+ units/month with automated lines (robotic loading/unloading, in-line inspection) to ensure consistency. A global automaker’s 1.5L turbo engine program uses our cylinder head covers (100,000 units/month) with 99.98% first-pass yield.
Case Studies: Solving Engine Performance Challenges
-
High-performance racing engine cylinder head:
Challenge: A motorsport team needed a lightweight cylinder head with improved airflow for their 4.0L V8 race engine.
Solution: Goldcattle used 3D-printed sand molds to cast the head from high-silicon aluminum (A356-T6), then CNC-machined the ports with 5-axis milling for 25% increased airflow. Result: 12% more horsepower, 8% weight reduction vs. the stock head, and a podium finish at the regional endurance race. -
Diesel engine oil pan for heavy-duty trucks:
Challenge: The client’s existing oil pan suffered from vibration-induced cracks after 200,000km.
Solution: We switched from mild steel to 4140 alloy steel, added ribbed reinforcement via FEA simulation, and applied a stress-relief heat treatment. Result: Cracks eliminated, service life extended to 500,000km, and warranty claims reduced by 95%.
Why Partner with Goldcattle for Engine Parts?
- Automotive focus: 26 years of exclusively serving the automotive industry, with 100+ engine part designs validated by OEMs.
- Quality control: Every part undergoes 100% dimensional inspection (CMM), material testing (spectroscopy), and pressure/vibration testing—meeting IATF 16949’s strict traceability requirements.
- Cost efficiency: Design-to-cost engineering (e.g., integrating multiple parts into one casting) reduces production costs by 15-25% without compromising performance.
- Global compliance: Parts meet EU REACH, China GB/T, and US EPA standards for heavy metals and emissions-related components.
Start Your Engine Part Project Today
Whether you’re developing a new engine platform, upgrading existing parts, or restoring a classic, Goldcattle’s precision and expertise ensure your engine components perform under the hood.
Contact our engine team: Send your 3D models (STEP/IGS) or technical drawings, and receive a feasibility report, material recommendations, and quote within 24 hours.
“Goldcattle’s custom cylinder head covers for our hybrid engine program exceeded our expectations—their attention to sealing detail eliminated oil leaks, and the lightweight PPA material helped us meet our fuel efficiency targets.” — Engineering Manager, a global automaker’s powertrain division