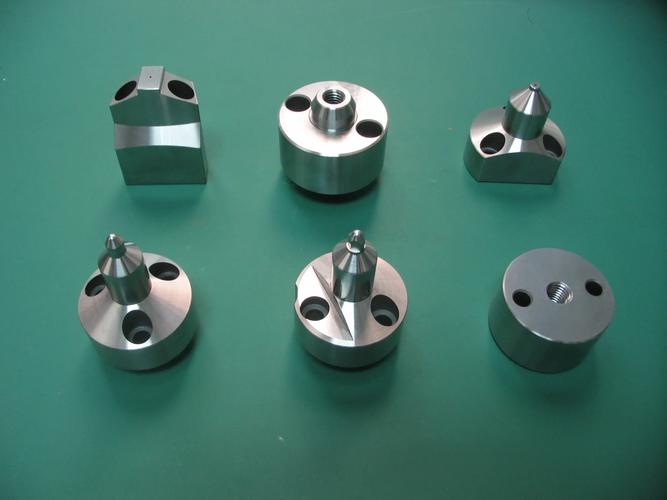
Core Processing Technologies: Engineering for Precision & Strength
1. Investment Casting (Lost-Wax Casting)
- Ceramic shell molding: Creates parts with complex internal structures (e.g., valve bodies with multi-way flow channels) and ±0.03mm dimensional tolerance. A 3-inch stainless steel valve core achieved Ra 1.6μm surface finish, eliminating post-machining for fluid-tight sealing.
- Wax pattern injection: Produces precise wax replicas (±0.02mm) for small-to-medium parts (5-500g), ensuring consistent casting accuracy across 10,000+ units. A copper alloy gear with 24 teeth maintained ±0.01mm tooth spacing, reducing noise by 15% in transmission systems.
- Vacuum casting: Prevents gas porosity in high-strength parts (e.g., aerospace brackets), achieving 99.9% material density and tensile strength ≥600MPa for 4140 steel castings.
2. Sand Casting with 3D Printing
- 3D-printed sand molds: Accelerates prototype development of large parts (5-50kg) like machine bases and pump housings, cutting mold lead time by 50% vs. traditional sand casting. A 500mm-long carbon steel machine frame achieved ±0.1mm tolerance, suitable for industrial machinery assembly.
- Resin-coated sand casting: Enhances surface finish (Ra 3.2μm) for medium-precision parts (e.g., motor housings), reducing machining allowance by 30%. A 200mm aluminum alloy motor shell cast this way required only 0.5mm post-machining.
3. Precision Post-Casting Machining
- CNC milling for critical features: Refines mating surfaces and mounting holes (±0.01mm tolerance) on cast parts, ensuring assembly accuracy. A stainless steel flange with 8 bolt holes achieved 0.02mm position tolerance, eliminating leakage in high-pressure pipelines.
- Grinding for flatness: Achieves ≤0.01mm/m flatness on sealing surfaces (e.g., valve flanges), critical for leak-proof performance. A 150mm-diameter cast iron flange ground this way maintained tight sealing at 200bar pressure.
4. Surface Treatment & Performance Enhancement
- Electroplating: Applies nickel, chrome, or zinc coatings to improve corrosion resistance (500+ hours salt spray for zinc-plated carbon steel parts) and wear resistance (60HRC for chrome-plated gears).
- Heat treatment: Normalizes cast steel parts to reduce internal stress (≤50MPa residual stress) and tempering to balance hardness (20-30HRC for ductile iron parts). A cast steel gear treated this way endured 1 million+ rotation cycles without fatigue failure.
- Passivation: For stainless steel parts, removes free iron to enhance corrosion resistance—316L castings passed 1,000-hour salt spray testing, suitable for marine environments.
Material Expertise: Matching Alloys to Application Needs
Material
|
Key Properties
|
Application
|
Advantages
|
Stainless Steel (304, 316L)
|
Corrosion resistance, 515MPa tensile strength
|
Valves, marine hardware, food machinery
|
304: 500+ hours salt spray; 316L: 1,000+ hours (resists chloride corrosion).
|
Carbon Steel (45#, 4140)
|
High strength (600-800MPa), cost-effective
|
Gears, brackets, machine frames
|
Ideal for high-load (≤200kN) industrial applications; easy to weld.
|
Aluminum Alloy (A356, 6061)
|
Lightweight (2.7g/cm³), good thermal conductivity
|
Automotive brackets, heat sinks
|
30% lighter than steel; suitable for weight-sensitive parts.
|
Copper Alloy (Brass, Bronze)
|
Electrical conductivity, wear resistance
|
Connectors, bearing sleeves
|
Brass: 60% IACS conductivity; bronze: low friction (ideal for sliding parts).
|
Precision Cast Hardware Parts Manufacturing Process
- Design & DFM: Engineers analyze client 3D models (STEP/IGS) to optimize casting feasibility—e.g., adding 2° draft angles to a valve body to ensure easy mold release.
- Mold development: For investment casting, wax injection molds are CNC-machined (±0.01mm); for sand casting, 3D-printed sand molds are produced in 3-5 days.
- Casting production:
-
- Investment casting: Wax patterns → ceramic shell → dewaxing → molten metal pouring (1,400-1,600℃) → shell removal.
-
- Sand casting: Molten metal poured into 3D-printed sand molds → cooling → shakeout.
- Post-processing: CNC machining refines critical features; heat treatment enhances mechanical properties; surface treatment (plating/passivation) adds corrosion resistance.
- Quality validation: CMM inspection (±0.01mm), X-ray for internal defects, and tensile testing ensure compliance with ASTM B637 standards.
Custom Precision Cast Hardware Parts Application Fields
- Automotive industry: 316 stainless steel turbocharger housings (withstand 800℃), A356 aluminum suspension brackets (lightweight).
- Plumbing & valves: Brass ball valves (leak-proof at 100bar), 304 stainless steel pipe fittings (corrosion-resistant for potable water).
- Industrial machinery: 4140 steel gearbox housings (high load capacity), ductile iron bearing blocks (vibration damping).
- Electrical equipment: Copper alloy terminal blocks (high conductivity), aluminum heat sinks (thermal management).
Customization Capabilities: From Prototype to Mass Production
- Complex geometry customization: Produces parts with undercuts, internal cavities, and thin walls (≥2mm) via investment casting—e.g., a medical device bracket with 0.5mm-thick ribs.
- Material customization: Adjust alloy compositions (e.g., 316L with 2% molybdenum for enhanced corrosion resistance) to meet client performance requirements.
- Production flexibility: 10-50 prototypes (7-10 days) via 3D-printed molds; 10,000-100,000+ units/month with automated casting lines (e.g., 50,000 brass connectors for electrical industry).
Common Processing Questions
- Q: How to ensure 0.05mm tolerance for a complex gear with 50 teeth?
- Q: What’s the lead time for 1,000 investment-cast 304 stainless steel valves?
- Q: Can cast parts withstand -40℃ low temperatures (e.g., outdoor machinery)?
- Q: How to reduce porosity in large castings (e.g., 500mm machine frames)?